The Biggest Safety Concerns of Supply Chain Manufacturing
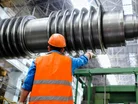
Manufacturing accounts for a significant amount of workplace injuries - and the injuries acquired are typically more disabling than those from less labour-intensive industries. On the factory floor, workers interact with large, high-powered machinery and equipment, and are likely to experience non-fatal strains, cuts, soreness, fractures, contusions and bruises.
In terms of fatal injuries, the manufacturing workforce can experience overexertion, slips, trips, exposure to harmful substances and unwanted contact with heavy objects and equipment. These risks are exacerbated by the traditionally male-dominated nature of manufacturing, where workers are less likely to seek help for injuries and abide by occupational safety and health practices.
These realities have been highlighted and explored by a recent survey by SafetyCulture, a global technology company that works to ensure the safety and success of frontline teams. Its workforce operations platform is used by more than 18,000 UK businesses, delivering lessons and vital resources on safety and risk mitigation in the workplace. Here are the biggest findings from their survey.
03: Employees face disruption and pressure
Manufacturing staff reported feeling stressed and stressed in the survey by external disruption. These are primarily weather-related, with poor air quality, icy weather and hot temperatures posing four of the top five disruptions reported over the past twelve months Road disruption was highlighted as another major concern.
Additionally, nearly a third of workers reported feeling mentally or physically unwell as a result of disruptions. This impact on health only worsens the drain disruptions caused to productivity.
40% of respondents said they arrived to work late and 17% reported being unable, on occasion due to disruptions to attend work at all. And what do people do, when their mental and physical wellbeing is low, their productivity is lessened and they still need to meet ambitious targets? They cut corners in order to keep up.
02: Employees are risking safety to meet targets
More than half of those surveyed (54%) also said they’d risked their health and safety at work, with one in five having done so ‘several times’. Workers said they cut corners because they were under pressure to meet quotas, were understaffed, and poorly equipped.
So why don’t manufacturing employees communicate these realities to higher-ups? The answer to that is a fundamental gap in trust.
01: Employees feedback reflects fundamental gap in trust
The research reveals that 20% of employees reported a near miss to their employer, but felt it wasn’t taken seriously. Another 12% who witnessed a near miss didn’t report it, as they felt their employer wouldn’t take it seriously.
“We know that manufacturers operate in a high-pressure environment, needing to maintain high through output while ensuring precision and quality. It seems that in workers’ efforts to put in a good shift and meet the demands of the job, they are putting themselves at risk.” says Alex Brooks-Sykes, SafetyCulture lead for UK and Ireland.
“Staff absences force manufacturers to continually juggle resources and are another drain on the sector’s productivity. With risk and disruption, communication is key. Management should maintain an open dialogue with staff on the shop floor and take reports seriously, especially as the technology exists to react in real-time and minimise disruption.”
So, how can supply chain manufacturers improve worker safety?
Safety experts typically advise a three-pronged strategy- investment in technology, the creation of a supportive workplace culture and stringent policies and employee training.
03: Investment in technology
Technology, in particular automation, has helped reduce the safety risks posed to the manufacturing workforce. Using robots means that fewer people are directly exposed to the hazards of the production line, rendering damage and injury a concern about cost- not people’s livelihoods. Automated machines perform tasks faster and more consistently than humans, without the risk of boredom or fatigue-related accidents. All around they reduce the risk of human error, which is the primary cause for all manufacturing injuries.
02: Creating a supportive workplace culture
As the results of SafetyCulture’s survey indicate, there is a serious issue with the manufacturing workforce risking their safety at work. This all stems from a lack of trust. The workforce feels that their safety isn’t taken seriously and that there’s nowhere they can go for support. The fact that the workforce, facing intense pressures, a lack of equipment and understaffing problems chooses to risk their safety rather than voice their concerns to higher-ups illustrates this very clearly. This is all compounded by the societal and workplace stigma that exists against men who seek help, being expected to endure hardship and not complain.
The solution is to cultivate a supportive working culture where the workforce is encouraged to voice their concerns and see them being answered with long-term, committed action. Furthermore, manufacturing executives shouldn’t wait for their employees to come to them. They should be continually evaluating and observing the conditions their staff work under, and proposing solutions to enhance productivity, safety and workplace satisfaction. Trust takes time to build, and this culture will take time to build too, but its benefits in terms of enhancing workers' safety are paramount.
01: Investing in employee training and ensuring robust safety protocols
Safe conditions and correct equipment must also be made available. Areas to focus on are ensuring employees have access to correct safety equipment, like PPE, mandating that aisles are kept clear and spills are immediately addressed to avoid slips and falls and preventing cross-contamination with hazardous materials by mandating a stringent use and cleaning process.
The most essential aspect of training employees on safety is leading by example and creating a culture where policies will be observed. Many manufacturers already have policies and training programs for employees, but day-to-day on the factory floor they’re bypassed and ignored to meet productivity targets. Manufacturers must stress to their employees that their safety is the priority, not productivity and profit margins. They must demonstrate this by strictly observing their policies, and reducing the pressure alleviated and advantages experienced when employees bypass them.
******
Make sure you check out the latest edition of Manufacturing Digital and also sign up to our global conference series - Procurement & Supply Chain 2024 & Sustainability LIVE 2024
******
Manufacturing Digital is a BizClik brand.