Top 10 ways to develop a world-class manufacturing safety strategy
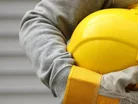
Manufacturing executives shouldn’t overlook health and safety management. Failure to develop and maintain an effective strategy could result in poor financial results, negative branding or in the worst-case scenario serious injury or death.
Large accidents relating to safety can incur painfully high penalties, set back production and cause insurance premiums to skyrocket.
How can manufacturing executives develop a health and safety system that protects its people, products and bottom line?
10. Have a handle on first aid.
In the event of an emergency easy access to medical equipment is crucial. The manufacturing facility should be well stocked with essential and job-specific first aid equipment, and each item should be well identified. All employees should have at least minimal training when it comes to using first aid equipment. In many cases, it is necessary to have staff members who are specially trained in first aid, CPR or confined-space rescue.
9. Know where you stand from a legal standpoint.
Make sure everyone is well aware of his or her accountability and responsibilities. Many countries and/or jurisdictions have differing level of liabilities, including personal level liabilities. All stakeholders within the company should be well aware of those liabilities and processes. Documentation should be prepared in accordance with the stakeholders to ensure everyone is protected and practices a safe work environment in their management style and behavior.
8. Restrict access to dangerous areas on site.
Work sites should only be open to the people trained and paid to be there. Friends, family members and employees from other departments should not be granted access to areas where work is being done. Identify restricted areas with signs and tape. In many cases, it is necessary to limit access with locked gates and doors. Let your workers know to report any unauthorized people in your facility and if employees grant unauthorized people access, know they will face stern repercussions.
7. Be aware of permanent risks and hazards and plan accordingly.
Many machines in manufacturing are dangerous regardless of whether they are working exactly as they are intended to. Take chemicals, for example, you can't simply remove the risk of a dangerous chemical by doing a quick check, but you can make sure all chemicals are properly labeled and that employees are equipped to handle them properly. Many machines heat up quickly and pose a fire hazard, even when operating correctly. It's your responsibility to know the limits of your equipment and communicate them to all workers.
Confined spaces are another permanent hazard that can be difficult to address. As confined spaces exist in most manufacturing settings, it is important for your employees to understand the risks of becoming entrapped or finding themselves in an oxygen-depleted area. Address that risk with training, exhaust blowers and confined space rescue equipment, and always make sure employees in such conditions work in pairs.
6. Ensure machinery is properly and regularly maintained.
Machinery and equipment that isn't properly maintained can be very dangerous. Even equipment with fail-safes can malfunction if you do not perform regular maintenance checks. To minimize the risk, have your equipment inspected on a regular basis by a professional, whether in-house or contracted. And don't rely solely on those spaced out inspections; make sure that your employees know how to perform a quick inspection before and after using each piece of machinery. The people who come in regular contact with your equipment should know what a machine looks like, how it smells and how it sounds when operating properly. If a machine is deemed potentially unsafe, it should be shut down immediately for repairs. Onsite workers should not attempt to repair malfunctioning equipment on their own without first alerting a supervisor.
5. Develop a manufacturing safety committee.
Encourage employees to get on board with outlining and maintaining a health and safety strategy by developing a manufacturing safety committee. Each division should elect a number of representatives, who will join a meeting each month or quarter to discuss changes to the safety guidelines of the plant. Each meeting should be an open forum, where all employees at the plant are welcome to join the discussion or bring a concern to the table. During these meetings milestones should be developed, and achievement of milestones should be celebrated, such as no lost time for each month, quarter, and year. Bringing your employees into the debate from the beginning and giving them a voice will motivate them to implement new strategies.
4. Examine processes for fatigue factor, breaks and rotation.
Repetitive actions and activities cause most long ranging issues with employee well being. Fatigue increases as the day goes on. Repetitive actions require synchronization with man, machine and environment, which begin to slow as the day goes by. These can be overcome with effective and frequent rotations, thus bench strength becomes a key to success. Breaks must be designed with these factors in mind and may be allowed differently for different type of jobs considering these load factors.
3. Promote manufacturing safety in groups.
Consider the safety of the group and rally the workforce towards a common goal. This automatically activates accountability to persuade others to act in a certain way, which mirrors the goal of focusing on safety. This is especially effective in more volatile and variable operations where volume surges result in frequent workforce reduction and expansion. Try a buddy system to ensure safety of the individual and that of the group. This team focused system makes it relatively easy to spot and prevent unsafe behavior and practices.
2. Make safety a priority from day one.
Safety standards and expectations need to be highlighted from day one. To build an effective safety program its implementation will need to be part of the company culture. Having an SOP is not enough, it needs to be explained, taught and critically, maintained by management. Floor managers need to watch out for employees cutting corners or ignoring protocols and discipline those employees when necessary.
1. Develop a training program.
A manufacturing facility is only as safe as the people working in it. Detailed training needs to be given to every employee entering the workplace and periodic refreshment courses are essential. Employees should have regular training on equipment, personal safety and first aid – they should be able to recognise if a machine is not working, know who to contact in a medical emergency and how to evacuate the facility. At the end of each training course, those in attendance should sign a form stating they understand the health and safety requirements discussed and that they’ll adhere to them. This information should be saved as part of the employee’s file.