The Rise of E-Powertrains: Ferrari Leads with New E-Building
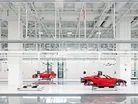
Ferrari has opened a new e-building to manufacture its first fully electric sportscar.
The news comes as the industry has seen an uptick in e-powertrain manufacturing, to support leading business’ sustainability efforts.
E-powertrains remove the need for an internal combustion engine to power the vehicle and include key components such as the electric motor and inverter.
Not just EVs: a look inside Ferrari's new E-building
The new e-building is a significant milestone in Ferrari’s 77 year history, paving the way for future sustainability-focused projects as well as the arrival of the company’s first fully electric model.
The company has been developing its electric expertise since 2009, with next year marking the birth of the first electric Ferrari.
While the concept remains under wraps for now, reports indicate it will have high voltage batteries, electric motors, and axles that are all manufactured in the new e-building.
The building also houses an educational centre and 30% of the space remains free for future development and innovation.
It is designed to reach NZEB performance, with sustainability measures such as the storage and recycling of rainwater, the irrigation of the building’s many green areas, and the insulation and thermal properties which absorb solar radiation in the summer.
None of its energy systems rely on fossil fuels, and its air conditioning uses a fully renewable electric heat pump.
“It has become known as the e-building, for different reasons,” says Ferrari CEO, Benedetto Vigna.
“The e-building is not just about ‘electric’. It will allow us to put all the pieces of the puzzle together so that the entire research and development and manufacturing process is optimal,” Benedetto continues.
UWB technology looks to the future
Inside, industrial robots are used to overcome production constraints and ensure an efficient manufacturing process.
“We tried to understand how this clean sheet of paper could also be a laboratory for what digital technologies can do in a flexible factory environment, where people are at the heart of what we do,” says Silvia Gabrielli, Ferrari’s Chief Digital and Data Officer.
“We did a scouting of all the latest technology that supports this kind of industrial facility, and identified the most promising for the next 20 years,” Silvia continues.
“So the new building is fitted with ultra wide band (UWB) technology, and that has to be integrated into the building’s infrastructure.
“It starts with the network and the cabling. Even AI starts with very physical and basic things. So we’ve put the necessary wiring in everywhere, and we’re ready to adopt an ultra wide band where and when it makes sense to do so.
“There are use cases where you can identify where a very valuable component is,” Gabrielli concludes. “It optimises the process, in terms of efficiency, but also safety. Increased digitalisation in some areas helps the people to focus more on their work.”
Automotive industry faces a "structural shift"
This technological innovation comes during what McKinsey calls a “structural shift”, with 70% of automotive suppliers expecting the industry to consolidate over the next three to five years.
McKinsey says tier-one suppliers are facing pressure from tier-two suppliers, in addition to major cost increases. This is an issue as tier-one powertrain suppliers have few options to pass along this cost, unlike the parts of the supply chain which can pass this cost on to consumers.
Bosch has entered this market, creating a “start-up” e-powertrain which allows automakers to save development time and get their electric vehicles to market faster.
The e-powertrain can deliver between 50 and 300 kilowatts, and is therefore also capable of powering large vehicles such as SUVs completely electrically.
It can also accelerate better and maintain a high speed for a longer period. To achieve this, Bosch has not only redesigned the system as a whole, but also improved the motor and power electronics components.
"Economically speaking, the e-axle may turn out to be a major coup for Bosch,” says Dr. Rolf Bulander, a member of the board of management of Robert Bosch GmbH and Chairman of the Mobility Solutions business sector.
McKinsey’s report predicts that by 2030, OEMs (original equipment manufacturers) will build 70% of all e-motors from scratch.
They also state “most OEMs seek aggressive annual price reductions and remain hesitant to include raw-material indexes in supply contracts.”
“This will lead to a consolidation of the fragmented EDU supplier market, which now has over 20 suppliers offering EDU systems.”
The report concludes that the shift of ICE (internal combustion unit) related portfolios toward e-mobility will allow new suppliers to emerge in the EDU (electric drive unit) space, meaning increasing competition and pressure on suppliers to sustain their market positions.
This will drive higher-quality, specific offerings for specific markets- such as Ferrari’s high-performance EDU.
******
Make sure you check out the latest edition of Manufacturing Digital and also sign up to our global conference series - Procurement & Supply Chain 2024 & Sustainability LIVE 2024
******
Manufacturing Digital is a BizClik brand.