Volvo: Automotive Innovation & Digital Transformation
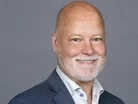
Hello, please introduce yourself
My name is Dan Lämkull and I’m a Technical Expert in Ergonomics at Volvo Cars Manufacturing Engineering.
I have been working for more than 30 years in automotive industry and I have been involved in research related to virtual manufacturing, and how simulation and automation can improve operators’ wellbeing by fitting the task to the human, not fitting the human to the task.
I completed my dissertation in computerised human modelling in 2009 and I was appointed Associate Professor in integrated product and process development in 2022.
Tell us about your role
As a Technical Expert in ergonomics, I am supporting the Manufacturing Engineering organisation in designing processes that will make the manual assembly tasks sustainable and ergonomically sound for our operators in our plants globally.
I am also leading our research projects in how simulations tools can be used to predict working conditions for our operators far before installation and start of production.
Currently, we are looking into how AI-cameras can be used to capture our operators’ motions before importing these motions into a computer and analysing the ergonomics.
Tell us about your work at Volvo?
I am constantly supporting my colleagues in designing sound workstations for our plant operators. Each car project has approximately 1,600 manual operations in the final assembly shops.
While there are manual tasks performed in our stamping shops, painting shops and body shops, the absolute majority of manual operations are done in our final assembly shops.
We are assembling 60 cars per hour in our European plants, which means that an operator has only 60 seconds to perform a task, and then the procedure starts from scratch again.
During one shift, an operator carries out 480 assemblies, which means that it is repetitive work. These kinds of tasks are demanding ergonomically. Parts can get tangled, and some are not very easy to grasp.
If a working posture is unfavourable or an article weighs 3 kg, the load will quickly become unacceptable and in the long run, harmful.
How do you support your team?
One crucial aspect of my role is how we can support our workers with automation as a remedy for bad ergonomics.
I used to tell my colleagues: “If you hate it – automate it!” It doesn’t make sense to let an operator perform repetitive, dull and unqualified work which at the same time endangers their health due to potential musculoskeletal disorders.
Tell us about your sustainability initiatives
Volvo Cars is committed to ensuring there are no work-related fatalities or serious injuries involving any of our employees or contractors. Nothing is more important than safety and wellbeing.
This approach applies all over our company as well as in cooperation with our employees and their representatives/unions.
Our approach to improve Volvo Cars work environment is well structured throughout the whole company with work environment committees, safety walks and inspections, followed up by yearly assessment of Global Minimum Requirements.
In my daily work, I try to minimise or remove strenuous activities that can lead to serious health consequences, by automating them. This is a key part of retaining tenured workers who have often had the same job type for many years.
Adjusting the work environment to address age-related physical requirements can help all manufacturers create a more supportive atmosphere and amplify the input of senior workers.
Do you have any partnerships you can tell us about
We are working with several suppliers of automation solutions. One amongst these is UR, a company with a potential portfolio of cobots and AMRs.
In the future, we will have a much higher degree of cobots and AMRs installed in our plants in pre-assembly stations and in logistics departments.
What do the next 12 months hold for you and the company?
Within 12 months we will inaugurate a new plant in Slovakia, and in 2026 we will start the production of a whole new electrified car in that plant.
We will also introduce the EX30 in the Ghent plant (Belgium) in 2024 – so far EX30 is only produced in China.
******
Make sure you check out the latest edition of Manufacturing Digital and also sign up to our global conference series - Procurement & Supply Chain 2024 & Sustainability LIVE 2024
******
Manufacturing Digital is a BizClik brand.
- Henkel: Optimising Washing Through Autonomous SensorsSustainability & ESG
- BMW: Creating Economic Circularity through Battery CreationSustainability & ESG
- Aggreko: UK Energy Manufacturers must Shore Up Supply ChainSustainability & ESG
- Capgemini: Gen AI Cause of Spiking Semiconductor DemandAI & Automation