5 minutes with Andreas Koenig on Smart Digital Factories
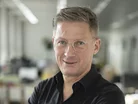
Ensuring global economic prosperity and stability is more important than ever as businesses seek to drive resiliency and growth in the post-pandemic environment. Andreas Koenig, CEO of of award-winning industrial wearables technology provider ProGlove believes there are three fundamental truths the global manufacturing community needs to adhere to today:
- The need to connect the human worker to the Internet of Things
- To enhance human-machine collaboration.
- Finally, to relentlessly drive the digitisation of the shop floor.
According to Koenig, this will allow manufacturers to tap into micro-efficiencies at scale, while raising product quality. At the same time, this will also promote worker well-being and safety, which will be ever important to the Smart Digital Factory of the future.
Hi Andreas! Please introduce yourself and your role.
“I’m Andreas Koenig, CEO of ProGlove. We provide ergonomic wearables and integrated software solutions.”
Tell us more about ProGlove, the company’s mission and a bit about its product line.
“ProGlove provides human-centred technology. We believe in the significance of the human worker as the primary driving force within Industry 4.0 and digital transformation.”
Hold on, why would the human worker be a driving force in Industry 4.0 and digital transformation? One might argue that both objectives aim to remove the human worker.
“Appearances are deceptive. In fact, it is a critical error to assume that technology and human workers are adversaries. Technology works best if it supports human needs. It needs to augment the human worker. Thus, we need to enable better human- machine collaboration – and that is what ProGlove is all about.”
So, how do you do that?
“We provide ultralight wearable barcode scanners that deliver the missing data points from the place where execution is happening. This allows organisations to connect their human workers to the Internet of Things (IoT) in order to drive their digitalisation initiatives across the shopfloor. In combination with our industry analytics solution businesses can not only improve human-machine collaboration, but also enhance their ongoing shopfloor processes and achieve a continual stream of worker-driven productivity gains. Let me give you one instance: At BMW, our wearable barcode scanners help save four million seconds per day because the operators no longer need to pick up and put down a conventional scanner gun. This translates to a save of some US$4,000 per car.”
In other words, you help businesses to turn their operators into flesh robots?
“I’d like to think of it as an opportunity to build the Human Digital Twin. The objective here is to allow for more efficiency, productivity and profitability. What we are doing differently than many other industry 4.0 technology providers is that we always begin with human workers in mind. We take a big burden off their shoulders by addressing issues like worker wellbeing, safety and health concerns. When rightly applied, these objectives allow businesses to reduce errors, achieve faster lead times, or identify best-practices. Not to mention: It is a powerful means to retain existing and attract new staff while making the most of your operational resources and infrastructure.”
But do you have proof to substantiate your claims?
“Why else do you think such renowned brands like Mercedes Benz, VW, BMW, DHL, XPO Logistics or GAP and Staples are relying on our technology - and that is just a short list. We continue to grow at a superfast pace. The secret to our success is in the results we deliver – including a reduction of the error rate by some 33% while saving some 50% of the overall scanning time. Some of our customers have seen efficiency gains of some 40%.”
What industries do your customers typically come from?
“All industries that rely on barcode scanning to move items along their supply chain. This includes retail and e-commerce, logistics and warehousing, post and parcel and certainly manufacturing and automotive.”
What differentiates ProGlove from other industrial wearable technologies?
“It is really a combination of things including the speed and worker-driven productivity, form factor, the ergonomics, the industry ruggedness and the ease of use. But let me put that in perspective: Our scanners only weigh some two ounces and sit at the back of the hand. This allows for hands free scanning with maximum dexterity. Through our worker feedback and display options we can also ensure guidance with all senses to reduce errors and travel times. Last but not least: Our devices leverage various sensors to collect meta datapoints which we can refine with our software solution to narrate the true story of the shop floor.”
Are you saying your solution replaces WMS or ERP solutions?
“No, I am saying we are offing a bottom-up view of the shopfloor. This view can stand alone, but it can also complement the typical top-down view of these enterprise applications. ProGlove is bridging the gap to execution. We are delivering the missing data points from the place where execution is happening. In other words: our software provides an as-is-view to complement an as-expected-view – serving as a system of truth. This will let you identify hotspots, blockers or compare workstation so that you can optimise your workflows, processes or act upon unforeseen obstacles.”
What is the future of human and machine collaboration, or indeed, workforce automation in general? What role does this have in digital manufacturing?
“So many people talk about the promise of the Autonomous Factory but there simply is no such thing as a “Factory of the Future” without people. Furthermore, it cannot be emphasised enough that technology is NOT a means to replace all human workers, rather a way to augment the work that humans perform. This message needs to be firmly anchored in the industry. This is especially true given current challenges such as labour shortages and disruptions in global supply chains.
“The idea of augmenting workers with wearable barcode scanners and cobots can certainly provide impressive efficiency gains. For example, recent benchmarking by VDC Research revealed how ProGloves’s wearable barcode scanners deliver speed increases of 30% while increasing the picking accuracy by 27%.”
What’s next for ProGlove?
“We will continue to expand both our software and hardware offering to provide even more powerful analytics capabilities and add multi-range and high speed scanning solutions.”