The rise of advanced robotics in industrial manufacturing
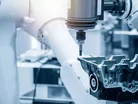
Customization and flexibility are two of the hottest words in industrial manufacturing right now. Customers want something made just for them, whether it is a personalized aftershave with their name on the bottle, a vehicle with all the features they need and none they don’t, or a new phone with the latest radio antenna for 5G connectivity. All this customization leads to one conclusion – manufacturing is moving towards high-mix production and making millions of different products in very small lots.
At the same time, many products made today are far too complicated for established automation technologies alone, forcing manufacturers to augment traditional robotics with manual assembly by human laborers. People are valued for their ability to understand and account for changes in a process very quickly. But what if this flexibility were included in automated processes?
A flexible and automated (even autonomous) production system is the Holy Grail for many manufacturers wishing to overcome the challenge of growing product complexity and simultaneously meet demands for greater customization. The ability to rapidly switch production from one product to another will be a defining feature of businesses on the path to lot sizes of one and the highly customizable products of tomorrow.
Small lot sizes are not inherently a problem, but current production processes cannot easily accommodate this without large investments in an increasingly complex infrastructure. To avoid this problem of exponential investments, which may or may not solve the problem, many businesses are looking for a more flexible approach to production. How can manufacturers make multiple products efficiently with minimal changes to the production floor between products?
Advanced robotics is the answer, and many companies are already on the path to adoption.
The Advanced Robotics Journey
Many factory floors rely on conveyor belt networks to transport everything from raw material to final products. But these networks were not designed to handle thousands of different products going to the constantly changing locations needed in a multi-product manufacturing process. What if a conveyor system could change? Perhaps change paths to avoid congested areas in a factory? Or change destinations to deliver a work piece to the optimal machining station?
These are the kinds of problems advanced robotics solves with the use of automated guided vehicles (AGVs) and autonomous mobile robots (AMRs) in tandem with an advanced software, solutions and application development platform.
Typically, the goal of using the robots is to deliver material from point A to point B with relative ease. But it is not as simple as just introducing AGVs or AMRs to a facility. Much of the investment value comes from the optimization and coordination of the advanced robotic technologies. In our experience, helping companies adopt advanced robotics into their manufacturing processes is a four-stage journey.
Stage one, or the Entrant stage, is defined by the use of fixed automation robotics or similar technologies where most operations are programmed manually. All process planning is done by a human, possibly with the aid of software, and the tasks are then assigned to specific robots to function at specific locations and times. This approach works well when producing high volumes, when changes or modifications to a production line are kept to a minimum. Since every action of a robot is explicitly specified at this stage, the robot must be taken off-line when changes are required and manually reprogrammed. This negatively impacts production times.
The second stage is for Veterans and is the most common stage today for industrial manufacturers. It is characterized by the use of the digital twin for complete system validation and for building control algorithms for the entire production line. Utilizing a digital twin of manufacturing provides deep insights on how to proceed in later stages of the journey by enabling the simulation of the entire facility. Significant productivity improvements at this stage can be achieved from concurrently updating multiple robots running off the same programmable logic controllers, reducing downtime on the production floor.
Progressing into the third or Pioneer stage, manufacturers can start automating more of the production process. Built on top of the insights learned from the digital twin and augmented with feedback from IoT sensors, task-based programming can be implemented for robots throughout the facility. This greatly reduces the time needed to program robots to accommodate a design or process change. Simple commands can be used to automatically adjust the robot based on a closed-loop calibration between the physical environment and the digital twin.
The final stage, called the Visionary stage, is where advanced robotics initiatives become highly autonomous, delivering near complete autonomy of the robots. This is also where AGVs and AMRs become highly effective, replacing static conveyor belts and a linear process path with advanced, mobile robotics. Now production changes can almost be as simple as inputting the number of products required and how many variations are needed. From that information, the system will determine the optimal path of how to produce the desired lot.
Software now determines how many parts are needed from storage room B, for instance, or what machining station will be able to ramp up the fastest to produce the lot. And, if the primary choice is down for maintenance, what is the next best option. The limits of this do not end at the factory walls. The benefits extend beyond to include suppliers and distributers, helping produce the most efficient workload for the factory.
The Visionary stage is the optimal point for implementing AGVs and AMRs, due to complete factory simulations. But advanced robotics can be brought in earlier stages to execute tasks simpler than production scheduling. Some companies have adopted AGVs and AMRS as semi-autonomous picking carts for warehouses, where the robot follows and assists a human worker.
Depending on how the factory is run, there are nearly infinite ways to optimize the facility. That is why the investment in the comprehensive digital twin is so important for this journey. It allows deeper insights of how a factory is running, helping to confidently invest in the future of the business. Advanced robotics is part of Siemens’ Xcelerator portfolio of software, solutions and application development platform where today meets tomorrow for industrial manufacturing.
By: Rahav Madvil, Simulation Product Manager for Siemens Digital Industries Software, and Noam Ribon, Senior Business Consultant at Siemens Digital Industries Software.
- Schneider Electric's Commitment to Sustainable ManufacturingSustainability & ESG
- Lenovo & Saudi Alat Building Green Manufacturing FacilitySustainability & ESG
- Nissan Brings Biodiversity to the Factory through RewildingSustainability & ESG
- Siemens, Sony & NVIDIA Unveil New Industrial AI Tools at CESAI & Automation