Toshiba: model-based development in automotive manufacturing
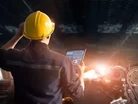
In recent years, model-based development (MBD) has become an increasingly popular and productive technique within the manufacturing sector, offering a number of advantages over alternative methods. Nowhere has this been more evident than within the automotive industry, where – through MBD’s process of simulating vehicular components against external models which emulate various traffic conditions – it has helped manufacturers to accelerate the development process of individual components, and prevent costly reworks.
However, that same speed of innovation which drove auto-makers towards MBD is arguably also now responsible for them outgrowing it as a technique in its current form. The recent emergence of CASE technologies – those which revolve around the development of Connected, Autonomous, Shared and Electric vehicles – has naturally come to the forefront of automotive development, in turn introducing new complexities for manufacturers as they strive to ensure these new systems can work effectively together.
This is where MBD hits a stumbling block. While it is effective in testing the efficiency of individual components, it struggles to keep pace with the interconnectivity of today’s cars following the arrival of numerous various electronic components and systems within the CASE fields – all of which need to be able to work together. For manufacturers who are operating in a fast-moving and highly competitive sector, it is imperative that they are able to test the viability of these technologies against one another to ensure they will work seamlessly together within the final car.
The challenge comes not only in bringing these proprietary technologies together in one place for testing and verification, but also in doing so early enough in the process to be able to identify problems and avoid expensive reworks down the line.
A cyber-physical era of model-based development
By applying a cyber-physical approach to model-based development, this problem can be overcome. This firstly raises the question, what does a cyber-physical approach entail? In principle, cyber-physical systems (CPS) are defined as those which collect real-world data and analyse it within cyber or digital environments – using technologies like Artificial Intelligence (AI) – before then applying the learnings back within the physical world to create added value. Such methodology is being applied today across the manufacturing sector and beyond, by companies like Toshiba, to help organisations build transformative, more sustainable solutions in a more effective way.
In the context of MBD, while many companies have to date purchase their own simulation tools from a vendor, the landscape is currently fragmented with these models operating independently of one another, and therefore being difficult to connect. This is where a cyber-physical approach has the potential to revolutionise what can be achieved, and subsequently simplify the challenges facing automotive companies today. Toshiba’s Distributed Co-Simulation Platform, for example, deploys a cyber-physical system to model-based development, essentially evolving it to a new level of large-scale simulations which connect multiple models – owned by different automakers and parts suppliers – within a single digital testing environment.
Such solutions allow automakers to create a fully virtual prototype of the car, enabling them to perform the necessary verifications of today’s complex automotive control systems much earlier in the process – and in turn, significantly improve quality and productivity. Connections between different suppliers can be automated to reduce man-hours, while simulations can be executed via the cloud to reduce latency and considerably accelerate the wider verification process.
At the same time, by bringing different companies together for joint verification while simultaneously maintaining the confidentiality of sensitive information for all participants, more automotive companies will be encouraged to collaborate within such environments. Efforts are already in place to set standards and shape the future of MBD within the automotive industry, with initiatives for a more cooperative approach being led by Japan’s Ministry for Economy, Trade and Industry (METI), as well as private vendor-neutral organisations like Germany’s Prostep AG. This can only be a good thing in terms of quickening the mainstream arrival of CASE vehicles, given the potential benefits they offer from an environmental and sustainability perspective.
The collaborative nature of cyber-physical systems like Toshiba’s Distributed Co-Simulation Platform will continue to become increasingly important within the automotive and wider manufacturing sectors, and not just for the cost and productivity efficiencies they bring. Within the current landscape, as global societal and business environments change, organisations will become ever more reliant on knowledge and information sharing to advance technological solutions and create a more sustainable society. A joint approach to techniques such as model-based development may be a first step, but as the physical and digital worlds continue to converge, we will undoubtedly see the emergence of more cyber-physical systems which transform the way in which we work and live across multiple domains.
- Digitalisation as a Strategy to Attract and Retain WorkersDigital Factory
- UPDATED VENUE & DATE – Manufacturing LIVE Chicago 2025Sustainability & ESG
- ABB Cuts Industrial E-Waste in Quest for CircularitySustainability & ESG
- Why Are Manufacturers Doubling Down On Digital Twins?Digital Factory