Fraunhofer IWS: Sustainably Manufacturing Battery Electrodes
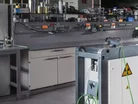
The Potential to Revolutionise the Manufacturing of Battery Electrodes
With the Federal Ministry for Economic Affairs and Energy (BMWi) predicting that Germany will consume roughly 655 terawatt-hours of electrical energy in 2030 - an increase of 20% compared to today - it is clear that society’s energy demand is continuously increasing.
Adding in the growing electromobility sector, this industry, in particular, is looking for new ways to reduce the energy required to manufacture batteries, which would result in a more cost-effective and more environmentally friendly solution.
DRYtræc: A Promising Solution
Being a key component of any battery, electrodes consist of a metal foil with a thin coating. It is this coating that contains the active components responsible for storing energy. “The conventional coating process uses a wet chemical method that applies what is known as slurry,” explained Dr Benjamin Schumm, Group Manager for Chemical Coating Technologies at Fraunhofer IWS.
To make the coating, the active material, conductive carbon and binders are dispersed into a solvent to make a paste, which is initially applied to the metal foil forming a wet coating. “Extremely large machines with very long drying tracks are needed to ensure that the solvent will evaporate afterwards. With DRYtraec®, we can design this process more efficiently,” adds Dr Schumm.
Developed by an interdisciplinary research team at Fraunhofer IWS in Dresden, the DRYtræc process uses similar raw materials to the slurry process, however, the dry coating technology works without solvents; instead, it uses a special binder.
Combined, the materials create a dry mixture that is then fed into a calender gap; a gap between two rollers rotating in opposite directions, with one rotating faster than the other. By doing this the process induces a shear force to ensure that the binder forms thread-like networks called fibrils. “Imagine it as a spider’s web that mechanically embeds the particles,” says Schumm.
Transferring the film in a second calender gap onto a current collector foil allows both sides to be coated simultaneously without significant additional work. Final steps of the process include the coil being cut to the required size. The individual parts are then stacked appropriately in order to produce the finished battery cell.
Combining the Expertise of Chemistry and Manufacturing Engineering
Fraunhofer IWS emphasises the clear ecological and economic advantages of DRYtraec, compared to existing battery electrode coating processes.
“Removing toxic solvents and long, energy-intensive drying machines from the process benefits the environment. The new process also accelerates production and requires only one-third of the equipment space of a conventional solution, saving costs in a number of ways,” says Fraunhofer IWS.
“The success of the DRYtraec® process comes primarily from the diversity of expertise in the research team at Fraunhofer IWS. Colleagues with a background in chemistry worked on the optimum powder mixture, but experts in manufacturing engineering, for example, developed equipment that prevents the dry film from ever being self-supporting, ensuring that it remains stable,” stated Schumm.
Industry Applications
Fraunhofer IWS’s first prototype of the DRYtraec systems were commissioned as part of the ‘DryProTex’ funding project. The project demonstrated the possibility to manufacture electrodes continuously regardless of the type of battery.
“The range of possible uses for the technology is not limited to a particular cell chemistry,” said Schumm.
“It could equally be used on lithium-ion cells as on lithium-sulfur or sodium-ion cells. We are even looking at solid-state batteries. These will be increasingly important in the future, but the materials cannot tolerate wet chemical processing. Thus, DRYtraec® allows us to offer a very promising solution to this problem.”
The process has reportedly picked up interest from the industry, with discussions underway with several automotive and cell manufacturers for the construction of pilot systems.
“Beyond manufacturing electrodes with DRYtraec®, the researchers at Fraunhofer IWS are engaged in many other research projects to examine the entire battery cell development process chain. By doing so, they are playing a key role in shaping the future of the battery,” concluded Fraunhofer IWS.
- The University Manufacturing Circuit Boards from LeavesSustainability & ESG
- Schneider Electric's Commitment to Sustainable ManufacturingSustainability & ESG
- Lenovo & Saudi Alat Building Green Manufacturing FacilitySustainability & ESG
- Nissan Brings Biodiversity to the Factory through RewildingSustainability & ESG