WEF: making manufacturing more sustainable after COVID-19
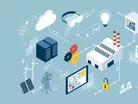
The COVID-19 pandemic is impacting global manufacturing demand and supply chains, workforce availability, energy use and CO2 emissions. As a result, global energy-related CO2 emissions are set to reduce almost 8% in 2020 to their lowest level in a decade. The UN advises global emissions must be reduced to this same extent, each year, for the next decade to limit global warming to 1.5˚C.
Over the past three months, manufacturing has been forced to transform at an unprecedented rate, both to find ways to innovate given the scarcity of resources and to scale digital transformation. The emissions reductions caused by crisis constraints is insightful and provides hope that dramatic change is possible — but it is essential to act now. With a plethora of resources, people will not be driven to innovate or challenge the status quo. By engineering within our planet’s constraints, industry can set the baselines for what must be considered and elevate what can be achieved sustainably.
Companies with a greater commitment to environmental, social and governance (ESG) benchmarking and reporting regimes continue to prove their ability to weather periods of uncertainty in the market better than their peers. According to a recent Blackrock report, despite the recent turmoil, companies with a record of good customer relations or robust corporate culture are showcasing resilient financial performance. Over 90% of sustainable indices have outperformed their parent benchmarks during the COVID-19 pandemic.
In reshaping the world towards a new normal, the industry should leverage digital transformation at an accelerated pace. This is typically for productivity, digital transformation is equally effective in achieving economic and environmental resilience. To capitalise on the convergence of Industry 4.0 and ESG goals, industry leaders must enable operational efficiency, leverage renewable energy, practice lifecycle thinking and promote supply chain data transparency.
Most production facilities are passive participants in the global energy supply chain. They monitor overall energy use and costs associated with available sources, however, are often overlooked by the controllable factors inside operations that enable consumption management in a way that brings value to the business. Manufacturers must evaluate and optimise individual, energy-intensive processes within operations by monitoring and measuring the process units, lines and machines consuming energy and then controlling overall consumption, economics and emissions.
The cost of renewable energy is driving its exponential adoption. Based on the levelised cost of energy, the cost of solar panels per watt in 1977 was $77, while in 2020 it is $0.14. Favourable economics paired with modern business models allow highly decentralised and digitised assets to be successful. Digital technologies that enable bi-directional control and connectivity when paired with distributed energy resources - such as solar plus battery storage - unlock new opportunities for flexible demand and curtailment. This includes peak load shedding, participation in automatic demand response management, buying and trading energy into the market, or dynamically shifting operations to match the availability of solar power and battery storage systems.
- The University Manufacturing Circuit Boards from LeavesSustainability & ESG
- Schneider Electric's Commitment to Sustainable ManufacturingSustainability & ESG
- Lenovo & Saudi Alat Building Green Manufacturing FacilitySustainability & ESG
- Nissan Brings Biodiversity to the Factory through RewildingSustainability & ESG