Audi to use Stratasys 3D printing to accelerate design verification
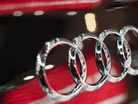
The German automotive manufacturer, Audi, has integrated the Stratasys J750 3D printer into its design operations.
The printer, the world’s only full-colour, multi-material 3D printer, has been adopted by Audi to innovate and accelerate its design process.
The firm has found that it is able to produce prototypes efficiently and effectively through additive manufacturing.
At its Pre-Series Centre in Ingolstadt, Germany, Audi has been able to reduce the prototyping time for its tail light covers by 50% since implementing the Stratasys printer, against methods such as moulding and milling.
"Design is one of the most important buying decisions for Audi customers, therefore it’s crucial we adhere to supreme quality standards during the design and concept phase of vehicle development,” explains Dr. Tim Spiering, Head of the Audi Plastics 3D Printing Centre.
SEE ALSO:
-
Audi has manufactured the largest quantity of e-gasoline in one batch
-
Robots and humans work side by side at Audi in an industry first
“As a result, we need prototypes to have exact part geometries, no distortion and extremely high quality, as well as true-to-part color and transparency.”
“The Stratasys J750 3D Printer will offer us a significant advantage, as it allows us to print the exact textures and colors our design defines.”
“This is essential for getting design concepts approved for production. In terms of 3D printing transparent parts, I have not seen a comparable technology that meets our standards.”
“Using the J750 for the prototyping of tail light covers, we will be able to accelerate our design verification process.”
“We estimate time-savings of up to 50 percent by using this 3D print technique in our prototyping process of tail light covers.”