The European Nearshoring Shift & its Impact on Manufacturing
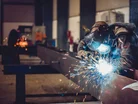
When looking at recent supply chain issues, it’s important to take a big picture approach. These disruptions reflect longer-term issues within traditional supply chain infrastructure and help to bring the conversation of deglobalisation to the forefront.
Many manufacturers, from food to apparel, are pivoting away from global supply chains to build greater resilience. Geopolitical uncertainties, the slowdown of economies and changing consumer-buyer trends are just some of the reasons companies are reevaluating their supply chain strategies. But rather than outright deglobalisation, Dan Benhamou, Senior Vice President at Brookfield, says he sees a trend towards regionalisation.
“Nearshoring is certainly a growing trend and one that we believe should be at the forefront of deglobalised logistics strategies to protect businesses from disruptions,” he says.
But shifting from a global to a regional approach isn’t a simple task.
Autonomising supply chains to build resilience in manufacturing
Brookfield is one of the largest asset managers in the world and through its logistics business in Europe, is on track to exceed over 4m square metres’ worth of logistics parks and warehousing across 80 sites in the region.
Benhamou leads Brookfield’s European logistics platform. Together with his team, they encourage the logistics industry to push the boundaries of supply chain infrastructure and drive global trade that shapes the future.
“We build, own and manage state-of-the-art warehousing for some of the world’s most renowned blue-chip companies, including Goodyear, Hermes, AB InBev and H&M Group,” he says.
Without resilient supply chains, Benhamou argues that manufacturers are going to find it increasingly challenging to bring materials from source to factory and to get completed products to their onward destinations such as distribution hubs, retailers or consumers.
But by reducing the reliance on a single global source and having local hubs, they’re much more able to adapt to unforeseen challenges and changes in demand.
One major industry moving towards nearshoring in Europe, is battery manufacturing.
“Instead of having mega factories in China, they are now spreading their operations across several markets,” explains Benhamou. “This is because companies don’t want to have all their eggs in the same basket and by diversifying their markets, they gain overall protection against anything that may disrupt operations in one region.
“We’re seeing emerging technologies change the game in logistics and warehousing operations, such as using automation to pick orders or using electric vehicles for last-mile deliveries, helping to drive greater operational and sustainable efficiencies. Whilst we are still some way off supply chains being autonomous, we do see the role of technology increasing in the future and organisations should be planning for how they will impact their operations.”
Bringing manufacturing closer to the customers
One of the key challenges organisations will face in the shift to nearshoring in Europe is how the flow of goods changes in the supply chain.
“If you’re importing finished goods, then local storage and distribution centres need to be relatively close to where consumer demand is for efficient and sustainable logistics,” says Benhamou. “But if manufacturing is being brought closer to home, then you’ll need these warehousing spaces to be located nearby with safety stock readily available, such as spare car parts, for example.”
The shift therefore requires some level of planning, as leases on warehouses for storage and distribution can be 10 to 20 years in length and there is currently fierce competition to obtain them in Europe.
“We are advising tenants to plan and secure space for where the company is forecast to be in the future, rather than right now,” says Benhamou.
Manufacturers need to have logistics infrastructure located close to home, both for finished goods for distribution and also safety stock of individual parts.
“If you’re an automotive manufacturer, you want to access spare components in the region rather than needing to wait for shipping as this will slow down operations,” he adds.
Aside from building greater resiliency, moving infrastructure and operations closer to where customers are based improves speed and efficiency in fulfilment, leading to better customer satisfaction, improved reputation and increased sales.
******
Make sure you check out the latest edition of Manufacturing Digital and also sign up to our global conference series - Procurement & Supply Chain 2024 & Sustainability LIVE 2024
******
Manufacturing Digital is a BizClik brand.