The next 10 years in manufacturing, from net zero to tech
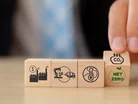
Some of the topics discussed by supply chain leaders a decade ago seem worlds away from current issues facing the manufacturing industry. At SCALA’s annual debate 10 years ago, the focus was on consumers; pleasing customers was going to be the biggest concern for businesses going forward. Some attendees also debated the role of technology in the future of the industry, while others saw ‘soft skills’ such as collaboration as key to future operations.
In part, some of these predictions have come true; while consumer demands have undoubtedly changed, they continue to drive supply, and collaboration has become vital to global supply chain synergy. However, what could never have been predicted was the global disruption that lay ahead for manufacturers, from the implications of the pandemic and Brexit to the Suez Canal crisis, increased global trade tariffs, and a looming recession.
Following this, discussions in 2023 largely revolve around resilience. Operational disturbances have now become commonplace amongst manufacturers, meaning flexibility is now business critical. We’ve examined the current topics on the minds of manufacturing and supply chain leaders and how they are likely to tackle these issues in the next 10 years.
Chris Clowes, Senior Consultant at SCALA
Ongoing geo-political disruption to manufacturing
The ongoing disruption in Ukraine, tensions surrounding China and international trade sanctions are making manufacturing operations increasingly expensive and unpredictable. With this in mind, manufacturers are constantly evaluating the location of their key resources to ensure that the supply chain is adaptable to change in the long-term.
Traditionally, to cope with instability, many businesses have considered offshoring to reduce manufacturing costs and access cheaper, skilled labour. However, the pandemic accelerated a demand for nearshoring and reshoring manufacturing, with most organisations at the mercy of the fractured global trade market. The Kearney Annual Reshoring Index has recently shown that up to 96% of CEOs in the sector are committed to reshoring as a supply chain resilience strategy. This is in an effort to save costs, while reducing the dependency on global market stability.
It seems highly likely that this trend is going to continue for manufacturers across the globe in the coming years. Business leaders need to mitigate the risk of any further disturbances and ensure that the entire supply chain is prepared for long-term instability.
Reaching net-zero in manufacturing
Across all industries, businesses have a big responsibility and role to play in helping to reach net zero. Unfortunately, introducing effective sustainability initiatives can often fall to the wayside for businesses, with cost savings being the main driver of operations. Concerningly, our research revealed that a third (32%) of UK businesses within manufacturing, retail and 3PL have no measures in place to monitor the total environmental impact of their operations. In addition, nearly two-thirds (64%) reported having no plans in place to take any action to reduce the impact of their operations.
Despite the relatively low take-up, we believe that the majority of businesses are committed to making positive changes for the environment, but economic pressures are proving to be the main barrier. With increased global trade tariffs and the rising cost of raw materials, energy and labour, the main priority for most businesses is managing finances.
However, prioritising positive change and introducing more sustainable business practices is becoming urgent, with the goal of reaching net zero by 2050 slipping away for many UK manufacturers.
The problem many companies have when it comes to addressing the sustainability of their business is getting started. Mapping the business, measuring its emissions and identifying the specific areas of the organisation where environmental action can be prioritised is a great place to start. Without having a holistic view of the business, leaders can’t implement impactful changes.
Additionally, within manufacturing a key focus of recent years has been making processes more circular. There are now consumer demands for more sustainable retail with over two-thirds of consumers worldwide purchasing a refurbished or recycled electronic item in the past. Therefore, manufacturers are expected to produce more durable, easier to repair, and easier to recycle products. To facilitate this, manufacturers should take steps such as choosing widely recyclable or compostable materials, clearly labelling products with recycling information and standardising components to make repairs easier.
Investment in technology
We recently surveyed businesses within the manufacturing, retail and 3PL industries and found that two fifths (42%) of businesses are planning to invest equal to or more than their annual warehousing costs in automation over the next five years.
With the total annual warehouse operations cost of those being surveyed being £520m, and the expectation that the equivalent of £470m will be invested in automation over the next five years, this investment is staggering. If this is replicated across the industry, this represents a huge and necessary advancement.
Labour shortages have been a key determiner in this growth, with the research seeing 81% of businesses cite staffing issues as the main driver for future automation. Amplifying the challenge, labour shortages are coupled with rising e-commerce sales that are projected to reach US$7.4trn by 2025.
If manufacturers are to cope with e-commerce then complete reliance on human labour isn’t the answer. Robotic and automated systems should be introduced to streamline and take over time-consuming and labour-intensive tasks, such as item picking and transportation within warehouses.
It’s clear that the manufacturing industry faces a demanding future. With global disruption unlikely to cease, and rising operation costs and environmental pressures posing further challenges, manufacturers have some important decisions to make. However, by building resilience into business strategy, considering small sustainable changes the business can take and embracing new technologies, companies can remain operational and profitable as they tackle what the next 10 years hold.
- Digitalisation as a Strategy to Attract and Retain WorkersDigital Factory
- UPDATED VENUE & DATE – Manufacturing LIVE Chicago 2025Sustainability & ESG
- ABB: 2025 Will Be A Balancing Act for Metals ManufacturersProduction & Operations
- ABB Cuts Industrial E-Waste in Quest for CircularitySustainability & ESG