Deloitte’s Jason Bergstrom & Paul Wellener 2023 predictions
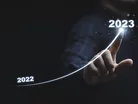
Hi Jason, please introduce yourself and your role.
“I’m Jason Bergstrom, the Go-to-Market leader for Deloitte’s Smart Manufacturing portfolio, The Smart Factory @ Wichita, and principal at Deloitte Consulting LLP.”
Tell us about your smart factory initiatives.
“While manufacturers face inflation, economic instability, workforce challenges, and supply chain issues, many are making investments that lay the technology groundwork for smart manufacturing operations, which help drive future competitiveness that can mitigate risk, improve operational efficiencies, and increase visibility.
“There are many considerations for the unique challenges each company faces. In addition, there’s the complexity of the tech stack and the various types of solutions, technology, and expertise that are needed to make it all fit together. In talking with our clients, we recognise this massive undertaking needs to be done right to be successful and scalable for the future. At Deloitte, we have deep relationships with technology companies and the experience in smart manufacturing to help tackle even the most complex challenges.
“To showcase smart manufacturing possibilities in real life, we built The Smart Factory @ Wichita – an immersive, experiential, sustainable, and education-based facility that showcases an end-to-end smart manufacturing operation. The Factory is made up of an ecosystem of more than 20 world-renowned solution providers, technology innovators, and futurists who bring their technology, knowledge, and vision to the table to help organizations make Industry 4.0 come to life. The idea is that we are working together to bring these companies into the future so they can better respond to the challenges of today and tomorrow.”
Can you tell us about how the long-term semiconductor shortage has impacted you?
“We have seen the semiconductor shortage impact many of our clients across industries. Even if it’s not part of their product, it’s part of their equipment to manufacture the product or other pieces of their operation.
“As a result, we see clients reevaluating the physical location of their operations as this and other shortages make the risk of locating supply far away very apparent. Reshoring – or bringing back domestic production – and nearshoring – establishing new production domestically that was once international – is on the rise in an effort to bring the supply closer to the demand. Industry players in medical technology, batteries, and semiconductors are leading the way with this trend, potentially influenced, at least in part, by government policies and investments from the U.S. in legislation such as the CHIPS Act. This means we’re talking to clients about greenfield/new builds for smart manufacturing facilities, starting from the ground up to create a true Industry 4.0 environment.
"The benefits of a completely new, smart operation also mean that organisations will be able to better predict parts shortages and other supply-chain related issues so that organisations can quickly pivot for less disruption to customers.”
How can Industry 4.0 facilities unlock new decision-making and performance-optimisation capabilities?
“Smart manufacturing can help improve operational efficiencies and increase visibility by day of enhanced data and analytics for improved forecasting, robotics and automation for efficiency, AI/ML to optimise edge computing, as well as cloud and 5G, which is covered in the report. Three top technologies to pay attention to are:
AI/ML: While companies have been using AI/ML on customer sentiment and quality control, implementing it on the factory floor will be key to providing insights and capabilities needed to make their factories more predictive, adaptable, efficient, and competitive.
Digital Twins: Many companies will begin using or enhancing their usage of digital twins to represent the factory’s product and production systems and reduce the time and cost associated with assembling, installing, and validating those systems to ensure they are making timely and insightful decisions based on finances and consumer demand.
Computer Vision: To enhance cobots, quality inspection, factory synchronisation, and inventory accuracy, companies will increase usage of computer vision regardless of their industry.”
Please introduce yourself and your role.
“I’m Paul Wellener, Vice Chair – US Industrial Products & Construction Leader, Deloitte LLP.”
Can you tell us about Deloitte’s newly released 2023 Manufacturing Outlook?
“Our newly released 2023 Manufacturing Outlook highlights five important trends for manufacturing playbooks in the year ahead: managing uncertainty; tackling workforce shortage; driving supply chain resiliency; scaling smart factory initiatives; developing sustainability.
“The sector has demonstrated continued strength in 2022; overall demand and production capacity have hit recent highs. Looking ahead to 2023, Deloitte projections (based on the Oxford Economic Model) anticipate 2.5% GDP growth in manufacturing.
“However, 72% of the respondents for our Manufacturing Outlook survey mention that ongoing supply chain disruptions and part shortages will be the biggest uncertainty for the manufacturers in 2023.
"Given this, and understanding the critical role manufacturing plays in the economy, manufacturers are strengthening their digital muscles and supplier relationship management skills to better address uncertainty and develop supply chain resiliency.
“Several top management priorities emerged from our research including the need to address the talent shortage. Another priority is keeping an eye on the fast-evolving environment, social, and governance (ESG) landscape. While manufacturers have historically been concerned with waste reduction and efficiency, they are expected to increase the focus on areas such as supplier diversity and the possibility of additional reporting standards. All in all, manufacturing is poised for growth despite anticipated challenges.”
What manufacturing trends do you expect to see in the new year?
“Digital Technology: Companies with higher digital maturity have shown greater resilience, and in 2023, we expect the same trend of increased digital investment and accelerated adoption of emerging technologies. More than 60% of surveyed executives are partnering with specialised technology companies to further their smart manufacturing initiatives in the coming years. Leading manufacturers will partner across their value chains to achieve competitive advantage.
“Supply Chain: Manufacturers will continue diversifying their supplier base and adding redundancy in the coming year. The industry may see an acceleration in OEMs taking equity stakes in suppliers or acquiring them to develop capabilities in-house and gain more control over their supply chain.
“Talent: As manufacturers continue to expand their digital initiatives, addressing the talent shortage will remain a top priority for most manufacturers. More than 70% of surveyed executives have highlighted finding and retaining talent as their top challenge in 2023. Manufacturers will continue to focus on advancing their DEI maturity and digital skill capabilities and actively seek ways to rearchitect and adapt to the broader shifts in the work culture.”
How can Industry 4.0 facilities unlock new decision-making and performance-optimisation capabilities?
“Manufacturers are focusing on a range of technologies to increase their operational efficiencies over the next 12 months. Robotics and automation enhance efficiency, whereas artificial intelligence and machine learning capabilities provide the required edge. This adoption makes manufacturers more resilient in the face of the current turbulence in the macro environment.
“Manufacturers are actively engaged in preventive efforts like increased monitoring for abnormal behavior of information technology and operational technology to prevent cyber attacks.
“Smart factories’ frontrunners are enhancing connectivity through the cloud, edge computing, and 5G. Once manufacturers have established the digital core, they invest in disruptive technologies such as AR, AI, IoT, additive manufacturing, blockchain, and advanced analytics.
“Some early adopters are already experimenting with digital technologies to interact and collaborate in creating a seamless unlimited reality experience between the digital and physical universe.
“Our survey highlights that one in five manufacturers is already experimenting with underlying solutions or actively developing an omniverse platform for their products and services.”