How technology can support behavioural safety in the manufacturing industry
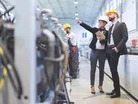
We all have bad habits – whether it’s interrupting our boss or forgetting to turn off our computer at the end of the day. Our minor faults can cause friction in the workplace, yet when bad habits extend into health and safety, the consequences can become very serious indeed.
Changing people’s behaviour isn’t easy, but it’s essential if we’re going to protect ourselves and our colleagues at work. In the UK’s manufacturing sector over the past five years, 22 people died in workplace accidents on average each year, with more than 3,000 suffering major injuries and a further 4,100 hurt badly enough to be off work for seven days or more, according to the Health & Safety Executive (HSE).
Why the focus on behaviour – isn’t health and safety all about rules and procedures? Well, no. A good health and safety management system documents the most serious hazards and communicates the measures required to manage them. It cannot possibly address every workplace hazard without lapsing into an impenetrable bureaucratic jungle. In any case, managing those hazards that are documented usually requires a combination of measures including safe behaviours.
So, establishing a strong safety culture, one which guides day-to-day behaviours, lies at the heart of reducing the number of deaths and injuries in our workplaces. A popular intervention to establish that culture is a behavioural safety programme (BSP).
Employee engagement sits at the top of the list of challenges facing manufacturers because if employees aren’t engaged then they will take shortcuts and ignore rules. BSPs use psychology to engage with employees and change attitudes, values, beliefs and behaviours so that health and safety becomes part of everyone’s job and not just a task carried out by a specialist group of people.
Engaging in this way with employees is difficult, but that’s where technology comes into play. After all, we use our smartphones and tablets to order our dinner, move money between our bank accounts, and turn our central heating off and on, so why should health and safety be any different?
Getting the basics right
BSPs need to have firm foundations if they are to succeed. The health and safety management system must present safe systems of work that are relevant and practical – and naturally adopted as “going with the flow” of operations. A solid process for reporting hazards, recording and investigating incidents, and analysing data maximises learning opportunities. Employees must be involved in the process so that they are engaged and feel empowered to act, and managers need to be accountable and “walk the walk”, leading by example.
These factors feed off one another, and this combination of engaged employees, committed leadership and the right tools – all supported by robust policies and procedures – can be a very powerful force for making workplaces safer. Technology provides one of the keys to ensuring that employees are engaged by making it easy for them to report hazards and record incidents, by involving them in the creation of practical risk assessments, and by making relevant information available based on context, skills and experience.
Disrupting the old ways
When it comes to the fast-paced world of manufacturing, health and safety can’t happen behind a desk. Employees and their managers are often responsible for quick turnaround times within strict deadlines – yet many are still expected to use old-fashioned and time-consuming paper forms or spreadsheets to report on health and safety.
Employment has changed dramatically over the past 10 years, especially in manufacturing, where working patterns are no longer as simple as they were. A worker will perhaps visit multiple locations across several sites, or their first language may not be the same as that used to create the company’s standard reporting system. Employees may have to work unsociable hours, during which they won’t have access to incident books or be able to contact support staff based in an office.
In those scenarios, reliance on traditional “paper and pen” or spreadsheet-driven reporting methods makes the risk of incidents going unreported – and potentially occurring again – unacceptably high. These bureaucratic and time-consuming processes do not engage employees. There’s a clear case for a radical overhaul that positions safety at the heart of the operation.
See also
- Daimler and BMW further cement their partnership in the future of mobility
- Field Service Palm Springs 2019
- Strata Manufacturing is set to further digitise its manufacturing operations
Harnessing new technology
As developments in health and safety management software gather pace, businesses are choosing to invest in disruptive mobile apps that link to web-based systems. Instead of filling in a form using a pen or going back to a computer to fill in a spreadsheet, workers can use their smartphone or tablet to log a hazard or near-miss straightaway. Basic psychology comes into play – the process is simple and straightforward and therefore it will be more easily adopted.
No matter where an employee is working, safety teams can get instant information. Such tools can have multilingual functions, meaning that workers can record observations in their first language, reducing the risk of information being lost in translation.
Health and safety software can also help to eliminate the administrative burdens faced by safety managers, freeing up time that can be put to better use learning lessons, benchmarking, identifying trends and taking preventative action. The ease of reporting and managing actions provided by technology means that safety becomes part of “the way we do things” for a company; employee engagement grows, and a robust, sustainable safety culture begins to emerge.
Using the data
Once incidents have been recorded and hazards have been reported out in the field, that data can then be fed into broader safety management systems. Too often though, complying with legislation is the primary objective of such systems, creating a paper trail that documents how a company has met its obligations.
Instead, technology can be used to make this information more relevant and useful to managers and workers. For example, technology can help the relevant information about specific chemicals to be selected and presented in an easy-to-use fashion, meaning workers can have task-specific risk assessments detailing the steps they need to take to keep themselves and their colleagues safe.
Workers can be sent up-to-date information that’s relevant to their specific location or their task. If employees have reported hazards then they can be kept abreast of investigations and what’s being done to minimise the risk. This again feeds back into employee engagement – if they can see how data is being used then they are more likely to take health and safety seriously.
Building from a solid platform
Once these basics are in place, and health and safety is regarded as “part of the day job” and not an additional administrative burden, then an organisation is ready to adopt a BSP. Again, technology can help – making it easy to record safe and unsafe acts or other observations. These data sets make great leading indicators for future safety performance.
Employees will see that managers are taking health and safety seriously too. If leaders are committed and are available to answer questions, then workers take notice. Seeing managers using healthy and safety reporting technology on their phones and tablets would be a great way to demonstrate to workers that the system is working.
Reaping clear benefits
The fundamental advantages of innovative technologies in health and safety management are clear, particularly when applied to high-risk, fast-paced industries such as manufacturing. Companies embracing this opportunity ensure that they are compliant, that costs are controlled, and most importantly, that workers are kept safe.
Matthew acquired SHE Software in 2011 and took on the role of CEO in 2014. Holding an MBA from INSEAD and first-class degree in Engineering, Economics and Management from Oxford University, he began his career as an engineer, before spending six years at McKinsey & Company as a Management Consultant.
Matthew has extensive executive experience leading both large and small businesses, including as CEO of ESR Technology (t/o £10mn) and Managing Director of Atkins Management Consulting (t/o £70mn). As SHE Software continues its rapid growth across the UK, US and New Zealand, Matthew heads up the development of the business, ensuring that SHE Software continues to lead the market