Manufacturing modernisation, spreadsheets & PIM strategy
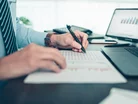
Industry 4.0. Smart factories and the IoT. Digital twins. Manufacturing leaders are rushing into modernisation initiatives to increase output, hone cost efficiency, and outpace (or at least keep up with) competitors. But all this progress makes one legacy tool stand out even more: the antiquated spreadsheet as a means for tracking product information.
Here, Justin Perkins, CTO at Image Relay, explores manufacturing modernisation.
Product information management (PIM) strategy in manufacturing
“Manufacturers are still using spreadsheets to track ever-more-detailed product data and SKUs are doing so at their peril. As a product information management (PIM) strategy, spreadsheets are tediously manual, slow, and—arguably most concerning—error-prone,” explains Perkins. “Manufacturers’ product lines can include thousands of products, each of which requires near-continual updates. Relying on spreadsheets to handle this crucial data erodes accuracy and brand trust, ultimately risking partner relationships and delays in getting products to market. Sure, it may not be as exciting as adding smart sensors to a factory floor to precisely predict equipment failure, but the efficiency advantages of modernising away from spreadsheets—and bringing simplicity to a complex data challenge—can be no less important.”
Here are seven areas where spreadsheets create issues when utilised for PIM, and how manufacturers can apply modernised strategies to help their teams manage and track a constant stream of product information and data:
Constant manual data entry makes errors unavoidable
“Managing complex product information with spreadsheets brings the speed and accuracy of data entry and data retrieval down to human limits,” says Perkins. “Teams deal with myriad spreadsheet tabs and long turns of their scrolling wheels whenever they need to access a particular product SKU. Inevitably, someone enters a product data update in the wrong cell, which is easy to do with copy-pasting and for product lines with minute differences between models. That inaccurate data then gets shared with customers and go-to-market partners, resulting in confusion, distrust, and interruptions in getting products onto shelves.
“Modern digitalisation strategies address these risks by enabling users to enter updates and additions to a database a single time and have them propagate wherever they need to be, reducing manual work and mistakes.”
Every partner needs a customised spreadsheet copy, which just multiplies work
“With spreadsheets, each customer and go-to-market partner needs their own unique duplicate documentation customised to the specific products they carry,” adds Perkins. “This means massive folders of spreadsheets and a complex (and time-consuming) process for entering product updates into each. Even with manufacturers expending tremendous efforts, timely delivery of new information is all but impossible. The odds of inadvertently introducing costly errors, such as missing key updates or sharing the wrong information, also rise with each duplication. These errors and delays risk damaging relationships and missing sales opportunities.
“Modernised manufacturers solve this by establishing a single source of truth with their product data and structuring data for easier export across various channels. Updates are entered once and instantly reach partners’ unique collections—accelerating manufacturers’ sales process and freeing their marketing teams to focus on more impactful tasks.”
With spreadsheets, certain employees become the source of truth
“When teams rely on manual spreadsheets to cobble together product data, they’re often actually relying on a certain individual employee who is the “agency of record”—with all the responsibility and knowledge of how everything works actually siloed within them. When that individual takes a vacation or leaves for a new opportunity, a long hard process begins where new employees scramble to understand where data is located across disparate spreadsheets. “Product history information is often unrecoverable because no current employee knows that history. While new employees learn to source crucial data, opportunities fall by the wayside.
Replacing spreadsheets and their individual caretakers with a modern PIM strategy must include a shift to universally accessible and accurate digital asset storage. This resource enables manufacturers to achieve continuity across employee transitions by maintaining clear product and information records, while also archiving historical data for easy centralised access,” says Perkins.
Version control becomes unwieldy
“Manufacturers continuously launch new product models and expand lines, creating the challenge of storing past version data without inadvertently sharing it as new. Spreadsheets have no advanced archiving features for preserving historical product information. Outdated information mistakenly presented as describing new product models can result in purchasing errors, expensive product returns, and upset customers.
“To solve these issues, manufacturers are utilising digital asset strategies that can give them full control over product versioning, making it clear which version is current and shareable, and which are safely archived.”
Spreadsheets don’t offer enterprise-grade security
“Relying on spreadsheets to keep production information secure simply isn’t effective. Manufacturers can’t expect to control who can see sensitive product and pricing information with spreadsheets at the heart of their PIM strategies. That makes for significant risks of key data being exposed.
“By replacing spreadsheets with a protected database, more modern approaches feature customisable data access controls for each internal team member or external customer, achieving security in step with the needs of manufacturing organisations.”
Spreadsheets can’t put product information in context
“Spreadsheets display thousands of cells worth of data, but offer few tools for comparing or contextualising how those data points connect or relate. That means leaving valuable data insights and sales opportunities on the table.
“Manufacturers that shift to robust modern data storage methods for their PIM requirements make it possible to visualise product data, intuitively recognize content performance, and rapidly pursue optimised product and marketing strategies.”
Product assets and spreadsheets don’t mix
“Manufacturing marketing teams need to track vast amounts of product content, from copy to digital assets. However, spreadsheets are a cumbersome approach to managing long-form copy, and can only hold links to digital asset files and folders. This leads to tedious manual effort and frustration when a link is wrong or broken, and assets become difficult to locate.
Modern strategies solve this by providing full management and customisation of a teams’ complete product information library—including all copy and assets regardless of data format. “By implementing a universal hub to organise all of a product’s assets for easy and direct access, organisations are that much more capable of delivering timely, accurate, and effective content to partners and customers.”
Spreadsheets’ day has passed
To do their best work, avoid costly mistakes, and operate at a modern competitive pace, manufacturers can’t keep crossing their fingers with spreadsheets to manage product information.
“A modernised and customised PIM strategy accelerates time to market by eliminating tedious and troublesome practices of the past, giving teams a trustworthy foundation from which to deliver their best work,” says Perkins.