Smart Manufacturing Explored, From Digital Twins to Gen AI
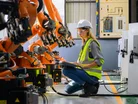
Predictions show the worldwide manufacturing sector will be worth £747.1bn (US$946bn) by 2030. Part of this growth is due to the increased uptake of smart manufacturing technologies, like IoT integration, but this is not a new phenomenon. In fact, 75% of large manufacturers had already implemented IoT technology in their factories before the pandemic.
Carl Johnson, UK Sales Director at Anglo Scottish Asset Finance, is familiar with many of the latest technological developments supporting manufacturing companies. Here, he tells us more.
“The smart manufacturing revolution doesn’t happen without a significant desire for better, more-rounded datasets and simpler ways of acquiring that data,” says Johnson. “Over the last few years, we’ve seen a growing demand for digital twin software amongst larger manufacturers.”
With further-reaching, more complex machine learning than ever, manufacturers are now able to model complex processes, with more reliability than ever.
“Manufacturers might use digital twinning to reproduce their entire factory process and judge procedural efficiency. Equally, they could reproduce a single machine to predict and pre-emptively deal with any machinery issues,” he adds.
Johnson warns that for smaller companies, a comprehensive digital twin strategy might be prohibitively expensive, but it’s undoubtedly something to be aware of.
“In the long term, software costs will inevitably begin to fall as uptake increases,” says Johnson. “The end-to-end insight provided by a digital twin is invaluable, whether you’re considering purchasing new machinery or thoroughly interrogating your productivity.”
Smart manufacturing and sustainability
There’s no getting away from the importance of sustainability, whether you’re in manufacturing or any other sector. Johnson sees that the latest technology offers greater visibility over all aspects of the supply chain, making a huge difference for manufacturing businesses with integrated supply chains.
“Tech-driven solutions like Zeus are leading the way in this aspect, helping companies increase fleet efficiency and reduce administrative hours. The software has helped its clients operate more sustainably, and reduce carbon emissions from shipping by 84%,” continues Johnson. “In the increasingly climate-conscious marketplace, such green initiatives can be a competitive advantage.”
Given the vast amount of power required for industry-scale manufacturing, businesses must show that they’re investing in solutions that limit their carbon footprint in order to retain a strong public perception.
As augmented reality capabilities improve, workplace wearables become more viable. Startup companies, like Tended in the UK and Motion Miners in Germany, are behind the wearable tech used on the factory floor.
“There are a number of benefits that come with using wearable tech,” says Johnson. “Tended’s approach augments your factory’s safety procedures, tracking the team’s movements to detect trips, falls or impacts. The technology also provides a panic alarm for use in an emergency.”
Meanwhile, Motion Miners’ technology optimises worker activity. The technology analyses a manufacturing team’s ergonomics to reduce the manual strain on their bodies.
“The analytics provided by this tech can help increase workplace efficiency and improve your team’s working conditions,” adds Johnson.
The risks associated with smart manufacturing technology
Given the increase in uptake of smart manufacturing technologies, more companies than ever should be – but aren’t always – investing in their cybersecurity practices. A sturdy operational technology (OT) cybersecurity framework is vital to limit the risk of data breaches and productivity loss.
“Too often, manufacturing businesses overlook security measures surrounding their Radio Frequency Identification (RFID) technologies or machinery that utilises IoT. In many cases, these technologies can act as an entry port for cybercriminals to access more business-critical IT functions.”
Cybercriminals can hold sensitive data or essential information for ransom, resulting in a loss of private access for manufacturing companies. This can be hugely damaging to operational capability and reputation.
“Only 35% of manufacturers say they have a single, comprehensive view of OT vulnerabilities – so if your business is not protected in this way, you should consider it a necessary investment for 2024,” says Johnson.
Gen AI’s role in smart manufacturing
In today’s smart factories, artificial intelligence is already present. More often than not, however, it’s predictive forms of AI that are being used to interrogate internal processes. Generative AI – which has the capability of generating imagery, text, audio or data – is also becoming increasingly viable.
“This technology has a number of potential applications for companies operating in the manufacturing sector, perhaps most notably for in-house product development teams. Gen AI can expedite the visualisation process when designing a new product and help anticipate the production needs required,” says Johnson. “Businesses can therefore accelerate product innovation, meaning a quicker route to market for new products as well as cost savings across the product development stage. Gen AI technology has the ability to amend the product visualisation in line with changing parameters, such as product weight, material or maximum cost. Investment in this new technology is therefore likely to cut the overall cost of developing prototypes.”
******
Make sure you check out the latest edition of Manufacturing Digital and also sign up to our global conference series - Procurement & Supply Chain 2024 & Sustainability LIVE 2024
******
Manufacturing Digital is a BizClik brand.
- Schneider Electric's Commitment to Sustainable ManufacturingSustainability & ESG
- Lenovo & Saudi Alat Building Green Manufacturing FacilitySustainability & ESG
- How AI & 3D Scanning Will Shape Manufacturing in 2025AI & Automation
- Nissan Brings Biodiversity to the Factory through RewildingSustainability & ESG