Top 10 guide for Plant Managers to track assets
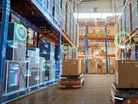
Managing and running a manufacturing plant efficiently is an asset-intensive task. It has numerous mechanisms with several motion control devices, fleets and mechanical infrastructure. While regular maintenance helps keep up machine health, its real impact can be seen with an efficient Enterprise Asset Management system [EAM system].
The importance of asset tracking
Asset tracking for motion control essentially means having an overview of all equipment across the factory. By deploying mobile tracking provisions to assets, the plant manager can control, change and enhance movement across the facility.
The biggest impact of asset tracking is the fact that you can reduce the hassle to optimise production and machine efficiency. An EAM software offers virtual control and real-time visibility into every asset you own. Some of the many benefits of asset tracking through an EAM software include:
1. Getting detailed information about assets
Based on business size, you can configure the EAM tool and you get dashboards, reports, performance, downtime, etc. For example, if you have a small sheet metal fabrication area with a drill, a punching machine, and a bending machine, a dashboard can be created, and insights for each machine can be available all time.
2. Perfect and maintain documentation
Factory shop floors have machines purchased and installed on different dates. Their timely maintenance, warranty, agreements, purchase documents, and invoices all have to be maintained and updated regularly. Asset tracking through a digitalised medium enables you to get into the minute details for all machines and achieve performance excellence by increasing the asset lifecycle.
3. Reduce administrative costs
Project costs can go skyrocketing due to flawed decision-making. An EAM software greatly reduces this risk as it provides insights about your asset performance, asset reliability, data analytics, and more. The decision-makers can easily use the mentioned data in order to make the right, data-driven decisions that will further reduce costs.
4. Bring down human intervention for fewer errors
In large factories with numerous assembly lines and multiple machines, where every piece of information is documented manually, running into errors is common. Duplications, missed data, data entry errors, etc. are small but common issues that get magnified at later stages of decision making.
On the other hand, software-based asset data collection has almost zero human intervention and hence spares you from flawed data. The data is not only accurate but also real-time.
5. Better planning and scheduling
Another important benefit of EAM software is the ability to proactively plan and schedule the maintenance of your assets. With an in-depth insight into work order status, maintenance history, overall technician workload, asset conditions, and more, scheduling timely maintenance work becomes a standard, not an exception.
All of that leads to a reduction in assets downtime and extends the lifetime of your critical machinery.
Impact of using EAM asset tracking software
Here are some ways in which EAM software positively impacts your plant’s overall performance.
6. Increased maintenance efficiency
With an EAM system in place, you can easily connect with the OEM for obtaining documents like SOPs, installation and operation manuals, quality standards, maintenance guidelines, etc. The easy availability of such information enables flexibility in maintenance planning — leading to higher efficiency and reduced downtime.
7. Optimised asset utilisation for all inventory
Detailed reports and dashboards derived from digitized asset tracking platforms help you analyze the utilisation of each asset. You get a clearer idea of whether you need to make new purchases, redeploy assets, or discard them.
8. Increased Asset LCM (Life Cycle Management)
Plant managers struggle with reducing downtime primarily because they lack relevant information beforehand and hence fail to schedule predictive maintenance. EAM tools eliminate this by offering all the information, for all machines, in a single view.
Which EAM software is right for your plant?
Modern EAM software should fit the way work happens on the factory floor. Traditional maintenance software has become obsolete and doesn’t add real value to maintenance teams, resulting in looking for workarounds to avoid using it.
On the other hand, EAM software solutions that fit the needs of the modern factory have a range of features, pricing modules and services — you can pick the one that best suits your plant’s needs.
9. Needs-based EAM software features
As a plant manager, you must define the primary goal of deploying an EAM tool — whether it is to optimise inventory, locate assets at all times, ensure performance management, predict maintenance, or something completely different.
Secondly, you must know whether you want to use it on multiple devices, like mobiles and computers. Cloud-based technology is gaining traction for enterprises as remote work is moving away from being just a passing trend. In this case, a cloud-hosting-enabled EAM works best.
10. Cost
With several players such as Microsoft, Oracle, Siemens, L2L and many more offering digitalised EAM tool development and deployment, the prices vary a great deal — based on the module you select and how the provider’s offerings are structured. It’s important to understand the capabilities and limitations of established providers, and compare those with emerging innovative players in the space.
Final word: The future is digitised, join the foray now!
A global pandemic has transformed the way the manufacturing industry operates. We have moved remote, and this move has increased the demand for flexible and efficient work methods. Machines must be optimised, processed, and must perform better — a clear callout for digitalisation in the coming times.
Knowing your assets thoroughly helps with making informed decisions while you stay remote. Having the right information at the right time is the key, and EAM helps you get that exactly. Research-implement-optimise are the steps tracing the way forward!