3 ways big data is changing the future of manufacturing
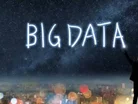
Everyone is talking about big data nowadays – and yes, our databases are immense. A gigabyte used to sound like a lot. Today, we talk about terabytes without blinking.
But big data didn’t grow up over night, in fact, data volumes have grown steadily for many years. But today, the value we get from all those ones and zeroes is increasing exponentially.
This is as true in manufacturing as it is in any other industry. Here are three ways big data is helping manufacturers think bigger than ever before.
1. Monitoring product quality proactively
Cloud computing. Cloud data storage. The Internet of Things. All these factors have collided to create a golden opportunity for manufacturers, who can now use massive data volumes in unexpected new ways.
In a recent Plex survey of manufacturers, 66 percent of respondents said cloud technologies have already improved insights into their business. Some 31 percent are either evaluating their big data needs and opportunities or plan to do so in the coming year – and 35 percent believe data analysis is the most important skill set for the next generation of employees.
All this data enables manufacturers to keep a much closer eye – or ear – on product quality.
Big data doesn’t just reassure manufacturers that they’re producing high-quality products – it also convinces their customers. Manufacturers now provide an incredible breadth and depth of data on their products’ construction and testing, establishing up front that they’ve delivered something of lasting value. Most buyers would agree that hard data beats marketing hype any day of the week.
Stop and think about where these developments are taking us. Manufacturers will soon be able to eliminate statistical process control from their quality control process. Instead, they’ll use today’s increasingly affordable sensors to gather real-time data on every item that comes off the assembly line. I’m talking about dozens of measurements on each product. The bottom line will be greater accuracy with less human involvement.
2. Seeing the future – and changing it
Operational analytics are great at telling us what just happened and why. Manufacturers have been doing that kind of analysis for years. But they’re now using the predictive aspects of big data to monitor their operations against their quality standards. That often means predicting when a machine or tool is about to break – before it starts churning out defective products.
Predictive analytics tell us what’s about to happen. Prescriptive analytics show us how to make machines do what we want. These disciplines are the crown jewels of business intelligence. Both require vast amounts of data – and the ability to analyze it effectively. That’s what big data delivers for today’s manufacturers.
It’s one thing to look at the history of maintenance issues or failures on a specific machine. But today, manufacturers factor in so many other variables. They’re looking at a press and factoring in not only all the metrics around it – such as temperature and tonnage – but also who’s working on the machine, how long of a shift they’ve worked, what tools are in the press, the day and time of year, and much more. They then factor all of this data into their predictions of when future failures will occur.
Predictive analytics isn’t a new discipline. But until recently, its high cost made it practical for only very expensive products or shop equipment. New tools are making predictive analytics a way of life for manufacturers of all sizes. And as the Internet of Things continues to mature, manufacturers are gathering more and more data automatically.
3. Getting customers into the data-collection game
The winners in our new data-driven economy will be the companies that can gather vast amounts of data and turn it into actionable processes within their supply chain. For manufacturers, the data gathering doesn’t stop at the boundaries of the organization – it includes information collected at customer sites.
Sensors come into play here, too. It’s becoming highly cost-effective for manufacturers to embed sensors into the products they deliver to customers – and the data they’re getting back is well worth the small investment in hardware. By extending the quality control process beyond purchase and throughout the life of their products, manufacturers now gather information that catapults their products to higher levels of performance better design, and longer lifespan.
This kind of innovation relies on a delivery agent that can put vast amounts of data at the fingertips of every stakeholder. Traditional ERP systems only create roadblocks. But cloud-based business applications and cloud storage let manufacturers replicate best practices and technical advancements quickly throughout their global enterprises.
With the cloud at your disposal, every worker, every forklift, and even every wrench will tap into vast volumes of data to improve the way they work. It’s your platform for dramatic change on a global scale.
- INDUSTRY 4.0: Big Data transforming manufacturing operations with flexibilityTechnology
- Future Manufacturing 4.0: Toyota innovation, robotics, AI, Big DataTechnology
- Tackling the manufacturing challenge with data and AIAI & Automation
- Expert comment: The future of waste in a digital worldSmart Manufacturing