Airbus and Autodesk create the largest 3D printed airplane cabin component
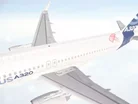
The bionic partition is a structurally integral part of the plane where cabin attendants sit during emergencies. As with many aircraft components, the partition has incredible structural and design requirements, including cut-outs and weight limits. This makes 3D printing a practical approach.
The partition was designed using an algorithm based on cellular growth in bone and used the principles and technology of generative design. This renders the structure stronger and more light-weight than ever. In fact, it’s 45% (30kg) lighter than current designs and is estimated to save 32,800 grams of CO2 per year.
In air travel, reducing weight means reducing emissions. If this new technology and material was applied to the entire cabin and to the current backlog of A320 planes, Airbus estimates that the new design approach can save up to 465,000 metric tons of C02 emissions per year, the equivalent of taking about 96,000 passenger cars off the road for one year.
A first test flight with the new bionic partition is due to be carried out in early 2016.
Follow @ManufacturingGL and read the latest issue of the magazine.