Conexiom: Measuring impact of 100% accuracy in data entry
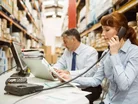
In the complex world of supply chain logistics, dispatching the right product in the right quantity quickly is a competitive edge. For any wholesale manufacturer or distributor, this process needs to be as fast and as error-free as possible. But this is no easy feat. When you’re converting purchase orders into sales orders, there are lots of points where the data entry and order processing process can go awry.
Manual Data Entry Challenges
Any mistake is bad news. Inefficiencies and errors can lead to delayed order cycles, slower payments, smaller profit margins and erosion of customer loyalty. Unfortunately, most organizations still rely on manual sales order processing. The majority of orders come in via email, some of these orders can run to hundreds of lines, making manual data entry and order processing a real challenge. Most orders require at least one or more manual touches before transitioning into sales orders. But each instance of human interference introduces the opportunity for natural human errors. Despite the best intentions, mistakes are unavoidable.
Order Entry Process Improvement
The best solution? Implement the ultimate in order entry process improvement and completely remove the human element from order processing, while still getting data into the ERP system. Relying on EDI and web portals is a good solution for a small number of customers. But for emailed orders (which represent the vast majority of orders), touchless sales order automation is the way to seamlessly transform purchase orders into sales orders.
However, finding the right solution is about more than simply the automation component. It is about finding a solution that offers 100% accuracy in touchless data entry and order processing. Why? Consider the impact of less than accuracy. Imagine your long-time customer Bill places a single 300 line-item order. At 98% accuracy, that would yield a couple of errors. It’s easy to understand why Bill would be unimpressed. He may even be upset enough to consider taking his business elsewhere.
Order Processing Accuracy is Key
Before that happens, let’s explore the impact of resolution efforts. First, there’s the cost of extra labor to resolve the errors. There’s time involved in receiving the not-so-pleasant call from Bill, as well as reviewing the sales order, comparing it to the original customer order, and identifying the mistake. And since this is an emergency, the situation also requires you pressing pause on entering other customer orders until the matter is resolved.
Once the correct items have been put together in a rush order and verified twice (because you can’t afford to make another mistake), the order goes to the warehouse for picking and packing. Then there’s the cost of rush freight. After all, you have to get the right products there without any further delays. Making Bill wait a moment longer than necessary will only aggravate him, so price is no object.
Then there’s the decision on what to do with the incorrect product. That may involve return shipping fees or writing-off materials. Then sometimes there’s a price adjustment on the invoice, either for the correct goods or sometimes out of goodwill to earn a second chance. Then it’s time to return to processing the bottleneck of orders that have been piling up while you dug yourself out of this mess.
In short, the penalty costs add up. Fast. Whereas with touchless, automated data entry and order processing that is 100% accurate, the opposite is true. Without errors, there are no spiraling extra costs. And Bill is kept happy. But more than that, you actively unlock savings. When you modernize the process of transforming incoming electronic documents into 100% accurate and-machine consumable transactions, you capitalize on a massive amount of untapped business value.
Data Entry Improvements: Conexiom & Diversey:
For example: With Diversey, the Conexiom platform has eliminated the manual entry of 87% of order lines (1.9-million in total). Previously, 57 FTEs had been required to manually enter orders. Now, 50 of that 57 can focus instead on activities that increase the level of customer service, and boost market share. Meanwhile, the data entry and order processing is happening faster than before, with fewer errors.
Data Entry Improvements: Conexiom & Grainger:
At Grainger, the Conexiom platform has brought the time between order emailed and shipment dispatched down to 15 minutes. 95% of orders are processed in under two minutes, with no errors. 83% of the orders required zero intervention from human staff, and the cost per order has come down from $4.50 to $.96. Conexiom's case study goes into more detail on how Conexiom worked for Grainger.
When it comes to data entry and order processing, error resolutions are expensive. They dissolve any hope of profit on a transaction, and cost you money. Worse, you could lose a customer. New customer acquisition costs are far higher than retaining existing customers, so it’s a losing proposition. And this is exactly why choosing a solution with anything less than 100% accuracy is unacceptable for the modern business.