COVID-19: digital twins in the future of manufacturing
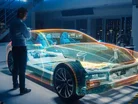
Ali Nicholl, Head of Engagement, Iotics, outlines the need for digital twins and how Rolls-Royce Power Systems demonstrates the manufacturing benefits
We live in a world of data and controls, legacy systems and siloes of information, where infrastructure and architecture are built around internal systems and processes. While it’s true the manufacturing industry was transforming its digital operations pre-the COVID crisis, the current market volatility caused by the virus has brought previous challenges into sharper focus.
Almost universally there has been an acceptance that operating conditions are now having to rapidly change and evolve and to survive, manufacturers must begin to operate more efficiently very quickly. This cannot be by improving the systems that may have worked previously.
In any enterprise there are many moving parts, but we are now starting to realise that the greatest asset any manufacturer needs is real-time visibility across corporate boundaries and down to the supply and demand chain. This will mean moving from siloed, largely fixed interoperation of ERPS, MES, PLM and PDM systems, to event-based digital ecosystems that interrelate data about what your customers care about - the assets - from design to use.
The age of the digital twin
There has been a lot of hype around digital twins in many sectors, but there is the need now for true digital twins as the powerful ‘digital shadows’ that are able to drive smart systems and the next generation of supply chains. These are digital twins that function as ‘white boxes’ interrelating data sources from across an asset’s entire lifecycle as its semantically defined, data-based virtualisation. They are comprehensive, interoperable versions of any business asset – people, places, processes or things – with access to all of its data and controls and structured and tagged, enabling it to be read directly by machines.
The inclusion of controls, as well as data, is integral to a twin’s ability to autonomously interoperate and leverage emergent pattern recognition and for AI to enrich customer-centric services. Their power lies not in what they can physically show us, but how they can securely and meaningfully interact with each other and, in doing so, create secure, scalable, adaptable digital ecosystems.
A digital twin can be made up of separate parts to create twins of components, assemblies, people, or an entire manufacturing plant and can be combined in multiple ways to create a unified access point or gateway to numerous sources of data and information.
This is not copying data, creating new data lakes, or rearchitecting legacy systems, but leveraging them through the creation of events and instances in a twin’s life that provide real-time insight into demand, supply, performance and operations. It is the ability for connected objects to talk to each other and work together to provide entirely new services.
What has a digital twin ever done for us?
To enable the full effect of the technology, manufacturers will need to embrace digitalisation on a far bigger scale, encompassing end-to-end processes throughout plants and across the supply chain. As organisations adopt new technologies and increase the number of endpoints, the volume of data they collect will swell hugely and more importantly, the interactions between them will grow exponentially.
Being able to manage those complex interactions at a granular level, securely and across ecosystems of partners, goes beyond traditional approaches. Investment in multiple siloed point solution apps and platforms has complicated global data estates, shackling innovation and limiting adoption, flexibility and adaptation as a result.
One-time, use-based system integrations are costly and restrictive, while data warehousing simply creates bigger siloes and fails to reflect the required co-operative, multi-party nature of service delivery. Digital twins offer a lightweight solution that deliver the digital transformation required to recover and then thrive in these challenging times.
How digital twins are being adopted and used by world leading manufacturers
Digital twins don’t replace existing technology or legacy investment, rather they extend capabilities, increase flexibility and mitigate the risk of businesses failing. Organisations such as Rolls-Royce are harnessing twin-based interoperable ecosystems to deliver the next generation in customer service: Customer Service 4.0.
Rolls-Royce business unit, Power System, is using digital twin and event data technology from Iotics to unlock over 200 data sources, brokering interactions to create digital twins of their in-field assets and receive real-time event insights across customer, supplier and partner boundaries.
Chief IT Digital Officer of Rolls-Royce Power Systems Jürgen Winterholler said, “Digital twin technology is helping us realise our vision of placing our customers at the heart of everything we do, exploiting digital twin technology to deliver the best service and to enable our customers’ businesses.”
Rolls-Royce Power Systems has a single source of truth for asset information streamline internal systems, enhancing customer service and delivering new digital solutions. Starting within its extensive rail ecosystem, it sees the transformational potential of physical products and assets having their own digital twins that securely capture, share and exchange data and controls and powering solutions that meet the new needs of the company, its customers, partners and suppliers.
“Customer Service 4.0 means seeing the world the way your customers do, collaborating with them, their customers, and our service partners, to deliver greater efficiencies, enhanced insights and new opportunities, without compromising on the quality and security they expect from Rolls-Royce Power Systems,” added Winterholler.
But it is not just manufacturing which will benefit from this brave new world. The use cases are as varied as the twins themselves and the digital twin age is the next evolution of disruption. What is the killer application or use case for the web and internet? There isn’t just one. It is not what the technology can do or what problem it solves, but what it enables us to create and co-create. Liberating us from siloed thinking and approaches enables us to focus on what matters to companies, their customers and their communities.
SEE ALSO:
AWS: smarter manufacturing with cloud and IoT technology
How smart technology is transforming the industrial world
McKinsey: digital manufacturing, preparing for a new normal
Read the latest issue of Manufacturing Global here
For more information on manufacturing topics - please take a look at the latest edition of Manufacturing Global