How can 3D printing combat industry changes in manufacturing?
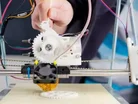
Manufacturers are increasingly facing new challenges as they look to stay competitive in the global market place. From changing market forces to the need for increased production efficiency, the issues are broad. And all whilst trying to ensure that the quality of their goods is exceptional and customer response times are kept to a minimum.
It’s clear that manufacturers must innovate in order to tackle these difficulties, and while many are keen to change the way their businesses run for the better, they are also concerned about the mounting pressures around cost and volume of materials used. Today, 3D printing can help tackle some of these challenges, offering transformative advantages at every phase of creation, from initial concept design to production of final products and the steps in between.
Why use 3D printing?
3D printing uses layer based manufacturing techniques which allows any shape or size to be printed using CAD system technologies. This unique way of manufacturing can transform business models by unlocking competitive advantage, and generate new revenue streams as companies can get products to market quicker. It can open up new possibilities such as printing parts on demand therefore reducing the need for high inventories and tooling, as well as helping to reduce waste because it only uses the materials needed.
Manufacturers are already utilising this technology to test new prototypes and reduce time to market, with the global 3D print market expected to grow significantly from $5.9 billion in 2015 to $49.1 billion in 2025, according to PIRA.
Faster product development
3D innovation allows manufacturers to improve their design productivity as well as ensure faster product development cycles, overall reducing the time to market. Compared to traditional manufacturing processes, 3D printing can also open up new avenues in enabling the creation of components that were previously impractical or impossible to produce, such as electrical connectors and bespoke sensor housing created by Canon’s customers. Tool making is also being revolutionised for manufacturing companies as 3D printing can enable the rapid progression and deployment of customised tooling. From short jigs and fixtures to pre-production tools, a range of items can be crafted, delivering a more efficient and cost effective production process. By utilising 3D printing in the product development process, more frequent and improved testing can be delivered earlier in the cycle, meaning the cost for change decreases as the design advances.
Quality improvements
In addition to cost savings, the multiple test cycles will allow for quality and efficiency improvements, giving manufacturers the ability to form perfect designs through agile but precise testing. As the product begins to take shape, designers need to verify and test design elements to ensure the new product will function as intended. 3D printing allows design verification to be an iterative process where designers identify and address design challenges to spur new inventions or quickly identify the need for design revisions. Thanks to in-house production, intellectual property for products and parts can also be kept safe.
With PwC estimating that 67 percent of manufacturers are already embracing 3D printing, the technology is creating a platform for innovation in manufacturing and is setting the stage for enhanced productivity, advanced design capabilities and business agility in the years to come.
Sav Jeyendran is Application Specialist 3D Printing, Canon UK