How R&D Disappeared from American Electronics Manufacturing
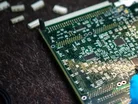
Ever since the beginning of commercial computing, the U.S. has been a leader in both design and manufacturing of electronic systems. The U.S. brought the world Moore’s Law and the technology that put a man on the moon. A technology ecosystem emerged that balanced companies developing and manufacturing for government and commercial customers. Defence, space, and other government applications drove the latest innovations, while commercial applications provided the volume to make such investment practical.
In the 1990s, computing hardware started moving towards commodification. As differentiation became more difficult, several innovative computing companies shifted out of hardware altogether, and those that remained were in an existential battle to drive down costs. Manufacturing processes were not seen as a source of value creation and differentiation, only a cost centre.
Until that point, computer manufacturers owned manufacturing facilities, including circuit board fabrication plants. One such leading computing OEM had approximately a dozen and was spinning them off or shuttering them one by one in favour of an outsourcing model that, per common perception within the industry at that time, de-risked their financial balance sheets. The independent board houses continued to use similar processes to those developed by the large OEMs through decades of research and development, so the results were comparable at a better price.
But one operations executive was sceptical, and he conducted a survey of sourcing professionals within his organisation and the board houses. In the survey, he asked who would be responsible for R&D costs for circuit board manufacturing processes in the new, outsourced future. And the response was telling: the sourcing professionals at the OEM answered that the board houses would be responsible, and the board houses responded that it would be the OEM.
The gap was glaring; clearly, a portion of the savings achieved through using board houses was simply that no one would be conducting expensive R&D. But immediate cost savings were essential to the survival of these OEMs as established market players struggled against lean new market entrants. The OEMs paid cut-rate prices, effectively barring the board houses from any investment. The result: electronic circuit board manufacturing process technology in America was essentially frozen in time.
The same pattern occurred across electronics manufacturing. Outsourcing activities typically considered the cost of manufacturing a single product, and outsourcing companies could not win business if they incurred R&D expenses. OEMs found existing manufacturing processes to be sufficient for most consumer products. But the symbiotic ecosystem was breaking down, affecting products that required U.S.-based manufacturing due to security concerns, proximity to regulators, or other reasons.
Aerospace and defence OEMs, which often required U.S.-based manufacturing for sensitive products, found the sclerotic advances in the manufacturing process to be an Achilles' heel when addressing frequencies above 5 GHz and extreme SWaP challenges. Very High-Density Interconnect (VDHI) is a clear example; defence primes and the U.S. Department of Defense have both identified VDHI as a key technology to enable the next generation of electronic warfare, but the U.S.-based capacity for building these circuits is limited.
During the same time period, companies in Asia were adding technical capacity to take on more complex products, moving beyond merely low-cost assembly. The lower labour price point left space in budgets for R&D expenses. Government industrial policies supported capacity development through tax breaks, subsidies, and workforce development programs. Soon a virtuous cycle was born; the demand for manufacturing engineering expertise drew talent, and the talent drew business, giving the well-educated workforce essential hands-on experience. Tim Cook drew America's attention to this often-overlooked fact in 2017 when he said, "In the U.S., you could have a meeting of tooling engineers and I'm not sure we could fill the room. In China, you could fill multiple football fields.”
All major EMS providers have sophisticated operations in Asia for precisely this reason. Benchmark is no different; our sites in Thailand, Malaysia, and China feature highly advanced capabilities. Across the industry, global teams of U.S. and international professionals develop and produce advanced electronics for many applications in a cost-effective manner. However, some industries are not able to leverage Asian manufacturing expertise for every product due to requirements regarding proximity to customers, regulators, or export controls. For these markets, U.S.-based manufacturing is essential. Several leading OEMs moved towards in-sourcing some manufacturing to meet these requirements. This has proven challenging due to a shortage of manufacturing engineering expertise in the U.S., and for any individual OEM, it is difficult to spark a virtuous cycle of talent development and ever-increasing process complexity.
What if the solution to this problem lies not with returning process development R&D to the OEMs, but instead to the outsourcers? Some smaller, specialised electronics manufacturing service providers began innovating in specific niches. Their services are highly valuable but don’t solve the overall problem of reliably fabricating advanced designs in the U.S. at reasonable volumes.
A more practical solution is to cultivate manufacturing process R&D within the larger U.S.-based EMS providers. By targeting investments towards specific technology realisation problems and spreading the costs across several OEM programs, these providers can bring innovation back to the U.S. and meet OEM’s onshore manufacturing needs.
One of the ways our company, Benchmark, is addressing this is by using a combination of licensed IP from innovative startups and processes developed by talented engineers from across defence, computing, and telecommunications, to develop a unique set of innovative manufacturing processes and the ability to continuously adapt processes to new challenges.
American electronics manufacturing is moving into a new phase of R&D-driven innovation, and it begins with companies like ourselves who are willing to lean in and make the investments necessary to make OEMs’ cutting-edge products a reality.
Brian Sinclair, Manufacturing Engineering Manager Benchmark Phoenix
- The University Manufacturing Circuit Boards from LeavesSustainability & ESG
- Schneider Electric's Commitment to Sustainable ManufacturingSustainability & ESG
- Lenovo & Saudi Alat Building Green Manufacturing FacilitySustainability & ESG
- Verizon Business’ London hub: Where Innovation ThrivesDigital Factory