Next level 3D-Printing developed by the University of Tokyo
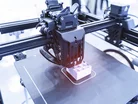
Complex in nature, 3D printing typically takes a long time due to the large number of 2D layers built up to form an object. With this process, a lot of material is wasted to support the unfinished object.
While there are some rudimentary concepts for self-folding 3D shapes, they often have shortcomings. For the first time, the University of Tokyo has combined 2D printing, origami, and chemistry to create a method of rapid 3D object fabrication without creating waste materials.
Enter a new wave of printed materials - 4D printing
Previously used for prototype products, 3D printing today is frequently used in the fabrication of commercial items including parts for jet engines. But it doesn't come without limitations, traditional 3D printing methods often come with long production times.
Enter 4D printing…
A concept aimed at mitigating these issues with minimal materials used, 4D printing uses materials with special properties to create self-folding 3D products. The concept is called 4D printing as it makes use of ‘time’ which is said to be the ‘fourth dimension’.
“My team and I discovered how to use accessible tools and materials to create self-folding 4D objects. Essentially, we’re creating flat sheets with origami patterns on them, and these patterns can be complex, taking even a skilled origami artist hours to form. But thanks to our special process, you can pour hot water over these flat sheets and watch as they spring into complex 3D shapes in a matter of seconds,” said Professor Koya Narumi, Project Assistant, from the Department of Electrical Engineering and Information Systems at the University of Tokyo.
By utilising special inkjet printers made for printing with UV-reactive materials the printer prints a 2D origami design onto both sides of a plastic sheet that shrinks with heat. The university explains that while the base sheet shrinks when heated, the ink resists the shrinking, leaving gaps between sections of ink allowing the designer to control which way a certain section of the sheet folds. Hot water is then used to apply heat across the flat sheet so that the product spontaneously folds into an origami construction.
“Our biggest challenge was refining the options for hardware and materials, which took over a year to narrow it down to the final choices. But all the trial and error was worth it; compared to previous research around this same basic idea, we’ve improved the output resolution by 1,200 times, meaning the designs we can create are not just novelties but can be used for real applications. In the future, we may explore functional materials, such as conductive or magnetic inks, that could allow for machines and other functional devices,” added Narumi.
******
For more insights into the world of manufacturing read the latest edition of Manufacturing Digital and be sure to follow us on LinkedIn & Twitter.
Other magazines that may be of interest: Procurement Magazine and Supply Chain Digital.
******
BizClik is a global provider of B2B digital media platforms, for leaders across: Sustainability; Procurement & Supply Chain; Technology & AI; Cyber; FinTech & InsurTech; Manufacturing; Mining; Energy; EV, Construction; Healthcare; and Food. Based in London, Dubai, and New York, Bizclik offers services including content creation, advertising & sponsorship solutions, webinars & events.