Protolabs and GE Additive use 3D printing technologies for Met Gala gowns
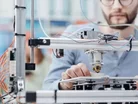
GE Additive and Protolabs have taken their additive manufacturing experience in an unexpected direction via a collaboration with fashion designer Zac Posen.
The three collaborated to construct four gowns and a headdress for showing at the Met Gala.
While the innovation does not herald the imminent arrival of consumer ready 3D-printed clothes, it does demonstrate the possibilities afforded by various materials and techniques.
Three principal additive manufacturing techniques were used in the construction of the pieces. Electron-beam melting (EBM) was used in the construction of sturdy metal frames for the dresses.
Meanwhile, as revealed by their joint press release, “the intricate printed vine headpiece with leaf and berry embellishments is printed as a single piece and made of Nylon 12 plastic and printed on a Multi Jet Fusion (MJF) machine.”
The high level of detail in this case was achieved through the powder based binder jet process, which progressively deposits a binding material on the powder to build up a structure.
Finally, resin setting stereolithography (SLA) technology was used across the items, allowing large segments to be printed in one piece.
SEE ALSO:
The interplay of different technologies necessary to fulfill the design requirements of wearable clothes mirrors the collaboration of the three entities involved, the surprising nature of which they were keen to highlight: “What might seem like an unlikely collaboration of design engineers and Zac Posen - one of the fashion industry's leading lights, at the forefront of innovation - in fact makes complete sense when you consider the transformative impact 3D printing is having on our everyday lives,” the press release states.
Brian Peters, Protolabs’ chief marketing officer, detailed the individual roles of the collaborators, saying that GE Additive was instrumental in designing the CAD files, while Protolabs used “a lot of GE equipment and we have the expertise and design capabilities to actually produce the various items that you’ll see in these dresses and pieces.”
The production of these items demonstrates not just the capability of the technologies GE Additive and Protolabs possess, but also the future possibilities on offer when they are deployed in collaboration.