Roto Dynamic’s clean manufacturing technology
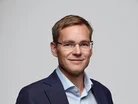
Efforts to decarbonise global manufacturing must spread throughout supply chains, from the final delivery of goods down to the sourcing and processing of raw materials. Industrial production of cement, steel, petrochemicals and chemicals — in other words, the stuff the modern world is made of — accounts for a quarter of all CO2 emissions and demand for raw materials is rising year on year.
Despite the scale of industry’s emissions problem, the IPCC says that net zero is “challenging but possible” for the sector: “Reducing industry emissions will entail coordinated action throughout value chains … as well as abatement technologies and transformational changes in production processes. Progressing towards net zero GHG (greenhouse gas) emissions from industry will be enabled by the adoption of new production processes using low- and zero-GHG electricity, hydrogen, fuels, and carbon management.”
This is an introduction to two of the abatement technologies in development that will provide industrial manufacturers with an electricity-powered alternative to replace combustion of fossil fuels; a major milestone towards emissions-free materials.
RDH and RDR: Massive temperatures through direct electrification
At Coolbrook, we combined technology from space science, turbomachinery, and chemical engineering to create the Roto Dynamic Heater (RDH) and the Roto Dynamic Reactor (RDR). By running on electricity alone, the high-efficiency RDH and RDR can generate the extreme temperatures required for the manufacturing of cement, steel, petrochemicals, and chemicals without the need to burn fossil fuels. Both technologies are being piloted and brought to market in collaboration with ABB.
While the application of these technologies to generate heat is novel, its underlying principles are well-established; in the most simplified terms, they are gas turbines running in reverse. Instead of using hot gas to rotate blades and generate power, electric motors rotate blades to accelerate gas and generate heat for various industrial processes. By accelerating the heated gas to supersonic velocity and then rapidly slowing it down in a diffuser to subsonic velocities, Coolbrook’s rotodynamic technology transforms kinetic energy to thermal energy and can generate temperatures of up to 1700 °C and thereby replace coal, gas and oil-fired burners that are currently in use.
The RDH technology is the only electric technology capable of providing a high enough temperature level required for cement production, which currently accounts for around a third of global industrial CO2 emissions, while the RDR technology is best suited for CO2-free steam cracking in petrochemical processes. Combined, it is estimated that RDR and RDH can reduce global industrial CO2 emissions by over 2 gigatonnes (Gt) a year and such technologies have the potential to propel these processes towards net zero.
Existing plants can be retrofitted with RDH or RDR without significant structural changes as the commercial units will have a footprint of just a few metres and can be used for a variety of applications, allowing for a gradual rather than wholesale switch to electric power. Coolbrook’s RDR and RDH technologies are now being piloted on a large scale and will be ready for commercialisation around 2024.
Electrification future-proofs manufacturing for the clean energy revolution
Direct electrification is the most energy and cost efficient way to achieve deep decarbonisation in heavy industry processes. Renewable electricity production, despite its challenges, can be scaled up to meet the needs of industrial actors. Electrification also builds on the existing infrastructure which society and industrial actors have more than 100 years of operational experience with.
Today’s electricity mix in Europe is already more than 60% CO2-free and by 2030 CO2 free sources will dominate the global electricity mix which is expected to be almost fully de-carbonised by 2040. CO2-free power is cost competitive and can also reduce the import dependency related to fossil fuels.
Once electricity generation is emission-free, any processes powered by electricity will become fully emission-free as well. And plants that are looking to transition from fossil fuelled to electric power are increasingly seeing their local electric supply being generated by renewable sources, at which point its manufacturing processes become CO2-free.
While the challenge facing manufacturers is unprecedented, the industrial sectors have always altered and optimised processes over time to improve efficiency and bring down costs. Achieving net zero will require the same approach to decarbonisation but the approach needs to be more ambitious and forward looking. Thanks to RDR, RDH, and various other emissions abatement technologies, there are many exciting opportunities for industry to invest in a new era of clean manufacturing.