ScreenCloud’s Mark McDermott: manufacturing & new technology
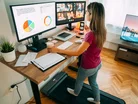
Mark McDermott, CEO and co-founder of ScreenCloud, leads a global team of 150+ people, who are dedicated to enabling brands to truly connect with their customers, and workplaces to design and provide a whole new approach to internal communications.
Here, Mark tells us more.
What is ScreenCloud?
“ScreenCloud is an all-in-one digital signage platform that powers the most effective and successful employee communications and engagement channels to date, and enables IT and Operations to transform their deskless workplaces into digital workplaces of the future. We create connected workforces across 9,000+ organisations including Coca-Cola, Walmart, and UPS.
“In an era of crowded and 'always-on' communication, screens can help companies simplify and broadcast information through a visually compelling, easy-to-use platform. Our company is committed to supercharging the way they display, interact with, and action on key news and information – by using our digital signage and hardware solutions to get the right content, to the right people, at the right time.”
Tell us about the seasonal challenges manufacturers face?
“The challenges surrounding frontline and deskless worker engagement and retention isn’t anything new to organisations. But, in the past year these challenges have been exacerbated as we have seen the impact of the pandemic, a worker shortage due to an aging population and lack of desire to take on deskless jobs, especially in the younger generation.
“Seasonal changes such as intense holiday demand on the supply chain – which can cause resourcing, fatigue and compliance issues in particularly busy times – growing customer expectations, a shrinking workforce, seasonal employees who need training/onboarding, and the tumultuous economy further worsen these issues to crisis-levels. Plus, manufacturers may need to perform seasonal maintenance on their equipment and facilities, which can disrupt production.
“With all these potential fluctuations and operational changes, communication becomes even more business-critical. If the ‘communications gap’ between head office and frontline/deskless workers continues to grow, this will be a massive driver of lower productivity, performance and retention; if not addressed properly.”
If manufacturing executives don't prioritise the frontline workforce in 2023, what might the impact be?
“There is currently an impeding gap between deskless employees and their corporate counterparts. Employees feel burnt out, overworked, and feel that their voice doesn't matter. In fact, nearly 68% of workers believe they have opinions on how to make their organisation better or more profitable, however a lot of the time they are not given the opportunity to share these ideas. Clearly, there’s much work to do in 2023 in building what we like to call a ‘frontline-first’ culture.
“Looking ahead, those that carefully curate their communication landscapes to meet their employees where they are and with the information they need will more effectively bridge that gap between all parties, and find the most success down the line.
“If not addressed properly the majority of today’s deskless workers will be more willing to quit their job causing a large mass exodus resulting in talent shortages and ultimately, will hinder an organisation’s ability to scale and meet customer demand/expectations.”
Tell us about the anticipated role of data in 2023.
“As leaders look for ways to address the acute mismatch between supply and demand, data will be essential in 2023. The manufacturing industry can no longer rely on outdated means to update their factory floor employees. In order for organisations to stay informed and continue to meet customer demands, it's critical that this data is visible and accessible to the people that need it, especially employees who are working on the floor. With that, software platforms that focus on business intelligence help provide visibility that’s needed across all manufacturing operations.
“To take it a step further, manufacturers can leverage data visualisation tools coupled with digital signage to significantly improve performance. Data also shows that deskless employees with sufficient technology are more likely to be very satisfied with their job (44%) and plan to stay with their current employers the next five years (35%).”
How can manufacturers embrace technology for the frontline workforce?
“While frontline employees are typically in technical environments, 83% of these workers don’t even have a corporate email address. Organisations need to offer a way for employees to provide constant feedback, continuous learning opportunities, surveys, and sentiment analysis; as well as opportunities to provide input into procedures, policies and regulations. One solution to this is digital signage, which allows real-time updates broadcasted to the entire organization, including the deskless workforce.”
- Digitalisation as a Strategy to Attract and Retain WorkersDigital Factory
- UPDATED VENUE & DATE – Manufacturing LIVE Chicago 2025Sustainability & ESG
- ABB Cuts Industrial E-Waste in Quest for CircularitySustainability & ESG
- Why Are Manufacturers Doubling Down On Digital Twins?Digital Factory