Service - not robots - is central to the re-shaping of the manufacturing industry
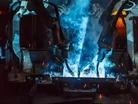
Apple supplier Foxconn last month revealed it has replaced 60,000 factory workers in one of its plants near Shanghai in China with robots. While the manufacturing sector is no stranger to robotics and automation replacing humans (you only have to look back to Fiat’s 1979 prophecy Hand Built by Robots to realise that), Foxconn’s move is definitely dramatic.
The sheer scale of change in just one factory will have sent reverberations across the globe. Certainly the sector, like many sectors, is going through a rapid adoption of new technology as well as coping with increased globalisation, but the biggest impact is not necessarily from robotics. Rather it is in how organisations are re-shaping and re-focussing on data.
The Internet of Things (IoT) is essentially triggering this change and what this data - collected from machinery, products and factories and fed back into analytics software to be reviewed by specialists - is doing, is forming the back bone of manufacturer decision making. It’s a digital revolution that is enabling more informed design, processes and innovation, but only if it has context.
In a manufacturing context, digital goes through the whole piece, from the design concept, to actually modelling the manufacturing process before you’ve even cut metal. And then through to manufacturing environments and collecting performance data, which is all about understanding manufacturing capacity.
What is often overlooked is that digital is in fact driving which products and services manufacturers actually deploy. While he accepted that servitisation is increasingly central, and that a lot of companies are “extracting a lot of value out of delivering a service rather than a product,” the fact is that service should now be integrated within a business and not be viewed as a bolt-on, a nice to have. It should provide the intelligence which shapes and determines the future of manufacturing.
And this is the point. Technology is enabling manufacturers to differentiate through service and even make money. No longer a cost centre but a profit centre, with the ability to upsell, as well as feedback vital customer information, service is now increasingly the vehicle for customer and product intelligence. It puts data into context.
Of course the role of the field service tech is changing too. It has to. As the importance of service grows, so the field service techs have to evolve with it, and develop new skills. That means working with more functionality on their tablets, phones and even their clothes, as well as handling data collection, reporting and keeping customers happy.
Interestingly, according to the 2016 KPMG Global Manufacturing Output report, 49% of global manufacturing executives plan to significantly change the range of services they offer in the next two years, while 45% are concerned about the relevance of products and services they offer. With 44% concerned about customer loyalty, it’s easy to see how service techs can play an increasingly essential role within the manufacturing sector. Data, and the intelligence surrounding that data, are the lifeblood for innovation and growth.
Joe Kenny is Vice President of Global Customer Transformation/Customer Success for field service management leader, ServiceMax.