Stratasys: Being More Sustainable With 3D Printing
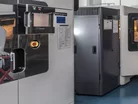
Additive Manufacturing (3D printing), “it can still be perceived as a buzzword,” says Andreas Langfeld, President EMEA, Stratasys “but if we dissect where additive manufacturing is being used today, it becomes more clear as to where the technology plays.”
The History of 3D Printing
Starting as 3D printing - “which many companies have spent a lot of money promoting the term 3D Printing,” says Langfield - has transitioned to what is more commonly known as additive manufacturing “this is because it outlines more of the designated solutions.”
But in the early stages, the approach was: How do you make, in the fastest way, your CAD design into a viable model or product in a digital way? “So from CAD design to printed part layer by layer, the solution was mainly used for prototyping. Many companies wanted to see what the functionality, or the look and feel of a future product may be before bringing it to market. This solution also provided organisations with confidentiality as they can produce prototypes in-house without outsourcing and the risk of confidential data being passed to third parties. This solution also saves time and money compared to prototyping in a conventional way,” continues Langfield.
“And then over time, it went into additional applications and use cases like tooling, jigs, and fixtures, where it's not just prototypes anymore, it's tools or parts that are enhancing the production workflow. Now we are producing parts additively on demand, instead of holding spare parts in inventory. So when a part is breaking, organisations have a catalogue of available spare parts that they order, and then it's printed overnight, or depending on the size, over one to two days. At Stratasys, we have added different technologies to our portfolio in order to make sure that we have the right solution in every step of the product development life cycle, all the way from prototyping and production efficiency, to producing parts additively.
“So all of this customisation is guiding the industry towards additive manufacturing as the solution to be applied because you don't need millions of parts to enhance the production floor, you need maybe a hundred or a thousand. But the big trend that we are seeing, which has been accelerated since COVID, is that companies do not want to be too dependent on global supply chains. They want to be able to have alternatives and to produce spare parts, as an example, on demand when they are needed, and where they are needed without shipping goods across the globe.”
Other trends Langfield is seeing include increased production needs, increased volumes being produced additively and the development of automation. “In general, we are seeing two trends in manufacturing. One is that the needs of production are moving more towards additive manufacturing because the volumes that are being produced are becoming smaller. A) because there is a shift away from keeping large amounts of inventory, to producing on demand which by definition requires a smaller amount of parts, and B) customisations. More and more products are designed to be a lower lot size because they want to meet the exact needs of a certain buying persona. So you want to make sure that your additive manufacturing is fast, reliable, and certifiable against industry standards. You also want to make sure that you have a variety of materials available in order to produce additively.
“Then there are also the technological advancements, automation and workflow. How do you make sure that the process from a cut design to the finished product is as seamless as possible and requires as little touch as possible because you want to reduce the risk of human error. You want to make sure that it's almost an automated process like it is on a real production line. When you have all of the technologies in place as a company to digitise your inventory and your products, you have already made a big step that you are more flexible in terms of how you produce the components and the products that you need in order to run your business.”
Being More Sustainable With Additive Manufacturing
“Sustainability is crucial. At Stratasys we want to be leaders in this,” says Langfeld. Despite this Langfield explains that “additive manufacturing is still being perceived as a new technology, there is not a lot of thought leadership happening in terms of sustainability in this field.” With this in mind, Stratasys became a founding member of the Additive Manufacturer Green Trade Association (AMGTA). “This is basically our statement to say that we want to make sure that mindful manufacturing is being applied in this field. As part of the AMGTA we are influencing the agenda for the years to come, making sure that additive manufacturing brings its value into the world where manufacturing is happening,” adds Langfield.
“In manufacturing today there are a lot of areas that can be improved, for example if you take demand production versus inventory. If you have an inventory, you will always have a warehouse. Those goods need to then be transported to those warehouses, which requires ships or trucks that will then produce CO2 emissions. But if you produce additively on demand, what you need, when you need it, you don’t have excess capacity, there is no unused inventory. So that in itself is more sustainable, when you have less inventories to build and less warehouses to store products or spare parts you reduce your CO2 emissions as a company.
“But that’s just one example of where additive manufacturing can serve real value. Another is in the process itself. When you build something layer by layer it produces less waste compared to traditional processes where you have a block, and from that block you cut until you have the product. To drive this forward we are looking into the recyclability of materials. If you take out soft technology, which is powder based, you can reuse the powder that has not been used in a previous print shop.”
Ultimately, Staratasys aims to demonstrate the capabilities and the benefits of additive manufacturing when it comes to sustainability. “We want to enable our customers to produce only what is needed and not in excess, but also industry innovate innovation and infrastructure. So how do companies benefit from the industrialisation across the globe, making sure that these on demand capabilities empower companies to improve the quality of life."
- Rolls-Royce & TCS: Hydrogen, the Aviation Fuel Of The FutureSustainability & ESG
- Manufacturing & Mobility LIVE: Become a Media PartnerProduction & Operations
- Want to Sponsor Manufacturing & Mobility LIVE in 2024?Production & Operations
- SAVE THE DATE: Manufacturing & Mobility LIVEProduction & Operations