UK manufacturing not utilising digitisation enough, compared to global competitors
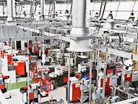
According to a new analysis from PwC’s Strategy&, UK manufacturers are needing to apply more technologies to their operations to keep up with global competitors.
The report, dubbed “Digital Champions: How industry leaders build integrated operations ecosystems to deliver end-to-end customer solutions”, suggests that manufacturers in the UK are currently demonstrating a sound level of digital ecosystem maturity and technology adoption.
However, only 1% of UK companies have qualified as “digital champsions”, compared to 19% of Asian firms, and 11% of American manufacturers.
In the UK, manufacturers expect an average of 10.8% revenue boost and 9.3% in cost efficiencies over the next five years.
32% of UK firms stated their employees have the required qualifications for a digital future compared to just 23% of EMEA manufacturers.
SEE ALSO:
-
HP showcases new 3D production technology at the Additive Manufacturing Users Group
-
Connectivity is driving the manufacturing boom, but beware of unwanted attention
-
35% of UK manufacturers are focusing on providing a digital customer experience throughout the customer journey, compared to only 30% of EMEA firms.
“While the UK's Industrial Strategy reinforces the huge potential technology can offer, making radical shifts across the manufacturing process or supply chain is neither quick nor easy to implement,” commented Darren Jukes, UK Industrial Manufacturing and Services Leader and Industry 4.0 Champion at PwC.
“As this report shows, there is also a risk that if UK companies don't pick up the pace, they could find themselves outmaneuvered by digital champions in other territories.”
“Employees are a crucial cog in this digital evolution - they enable and support the efforts of a company’s strategic direction, solutions, performance and operations.”
“As they navigate this transformational road ahead, firms must not only assess the status quo of their workforce - advancing the best and brightest and most digitally-oriented existing talent while training others to match these skills - but inject new talent into the organization where gaps in people’s skill sets and capabilities are revealed.”
- Nissan: Striving To Safeguard EV Manufacturing InterestsSustainability & ESG
- Be.EV Sheffield Charging Hub Signals EV Manufacturing GrowthSustainability & ESG
- Dassault Systèmes: Driving UK Aerospace Innovation ForwardsProduction & Operations
- Top 4 points why training & development will be a 2023 trendTechnology