Unveiling Business Spend to Unlock Manufacturing Growth
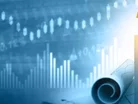
Manufacturing has been one of the hardest-hit sectors during the pandemic – and despite November marking the sixth consecutive month of increased output, there is still a long way to go on the road to recovery. Since March, the sector has been battling a range of challenges – from operating with reduced workforces to implementing social distancing measures in typically worker-dense settings. This is whilst firms have been facing ongoing pressures to innovate and make use of new Industry 4.0 technologies.
Amidst worsening factory slow-down and rising job cuts, normal trading levels are not anticipated any time soon. In fact, findings by Make UK revealed 37% of companies believe it will take longer than 12 months.
The biggest challenges keeping the manufacturing c-suite up at night at present are issues surrounding cash flow and liquidity following a downward turn in demand, production and revenues. In such an uncertain and pressurised economic environment, these business leaders are under increasing pressure to make immediate cost savings. This is where leveraging strategic cost measures will be crucial to mitigate the impact of the short-term pandemic fallout – whilst cost optimisation will be essential to rebuilding the sector and long-term success.
A rocky road ahead
Never before has the industrial world been confronted with so many simultaneous challenges, and options to innovate. Whilst the pandemic has been more than enough for businesses to deal with, ongoing turbulence is set to send further shockwaves through the economy, and for manufacturers in particular. Brexit is likely to bring major global supply chain disruptions – affecting suppliers by driving reduced demand and impacting the ability to fulfil orders on time. Manufacturers will also need to consider potential charges and tariffs for cross-border trading – which are likely to add increased pressure during an already volatile economic climate. And though the UK’s official withdrawal is just weeks away, many warn the UK is nowhere near ready.
Balancing survival with innovation
Focusing on the now is all well and good – and necessary – but ensuring future growth will rely heavily on implementing the right people, skills, and industrial technologies. Never has there been a greater need for manufacturers to embrace a range of industrial technologies to not only navigate current market challenges but to future-proof themselves in a rapidly advancing landscape. IoT, AI, analytics, augmented reality (AR), digital twins, blockchain and cloud computing are just some of the Industry 4.0 technologies available for today’s manufacturer, but current economic fears are seeing some firms turn away from such tools to focus purely on survival mode. Where cost pressures continue to mount, innovation can often be deprioritised – tech-fit manufacturers will be the strongest in the survival of the fittest.
Building agility by minimising and reallocating cost
Even before the arrival of COVID-19, business support functions within manufacturing were under pressure from senior management to shift their modus-operandi from being cost-centres to becoming value-centres. And for manufacturers committed to success in the new normal, uncovering the truths behind current financial and operational situations, and adjusting both spend and strategy in light of that knowledge, will be essential.
To accomplish this, manufacturers need complete visibility of all financial, IT and other business assets, along with operational performance data, and the costs attached to each. Analysing this information must lead to a clear understanding of costs vs value, to inform effective investment planning – which in turn enables the right, data-powered decisions. Responses, whether they be to financial challenges, operational or market changes, customer demands or specific business cases, should be automated where possible – to drive up efficiency while driving down both error and cost.
To build resilience in an uncertain time, it is necessary to have the means to allocate, track and accurately declare costs, while simultaneously transforming the business model, organisational design and staff working patterns to that required of the ‘new normal’.
In uncertain times, data-led decisions are critical
Whilst the solution may seem obvious, cutting costs and fostering transparency is often more complicated than just picking and using one of the many software tools in the market. However, financial management tools for enterprise services are vital in enabling manufacturers to gather vital real-time operational, project and vendor cost data – in essence, to uncover the truth around IT costs and make smart financial decisions. These tools enable fact-based scenario planning and in turn, help ensure that innovation and digital strategies take centre-stage in optimising services and refining processes – ultimately leading to further long-term cost savings.
During the pandemic, supply chain challenges – including the stockpiling of food and the need for vital medical equipment and PPE – have highlighted just how essential manufacturing is to our country’s survival. Firms must therefore buffer themselves against further forthcoming uncertainties – and, rather than just battening down the hatches, prepare for future growth. Because, whilst investment may be the last thing on the agenda for manufacturing firms battling through currently stormy seas, on the agenda, it must be. In these extraordinary times, the benefits of data acquisition and management across the enterprise, and the application of that insight to all business decisions, cannot be overstated. Comprehensive, current and, above all, transparent data, along with decisions and operational pivots made in light of that understanding, can provide a vital lifeline for manufacturers and protect British businesses.
- The University Manufacturing Circuit Boards from LeavesSustainability & ESG
- Schneider Electric's Commitment to Sustainable ManufacturingSustainability & ESG
- Lenovo & Saudi Alat Building Green Manufacturing FacilitySustainability & ESG
- Nissan Brings Biodiversity to the Factory through RewildingSustainability & ESG