Wolfmet Tungsten Alloys announces new 3D additive manufacturing capability
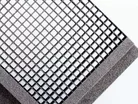
Manchester (UK) based Wolfmet Tungsten Alloys today announced the launch of its new Selective Laser Melting (SLM) capability (patent pending) on October 6.
SLM will enable the company to produce pure tungsten components and parts at a higher level of complexity and accuracy, primarily for the nuclear imaging sector. Michael Anderson, Product Group Director for Wolfmet said “The launch of our SLM service complements our existing expertise in manufacturing tungsten alloys across the nuclear, aerospace and motorsport industries. SLM can produce complex collimators with extremely fine grids. This enhances the quality of the image, as the photons are channelled more accurately through the collimator to the detector and scatter is reduced.”
Using data from a 3D file, SLM comprises a high powered laser that fuses successive layers of tungsten powder until a complex component is produced. Wolfmet SLM delivers clear advantages in the design and manufacture of parts such as collimators, for example:
· Production of highly complex component designs
· The ability to make shapes not possible with traditional milling and turning
· Improved resolution via thinner septa and smaller apertures
· No tooling costs for new designs and prototypes
· No cost penalty for short production runs
· Non-magnetic – MRI compatible
· Reduced delivery times
Steve Jeffery, Wolfmet’s Business Development Manager commented "With more than forty years’ history of producing tungsten alloy components, we are always focused on improving the performance of tungsten components for our customers. We’re excited to now deliver collimator designs which would not have been possible through conventional milling and turning, and with finer tolerances than before.”
Wolfmet will be sharing more information about its SLM capability at the EANM Congress in Hamburg, Germany, 10-14 October 2015 (Stand 224, The Pavilion).