AVEVA: The future of manufacturing post COVID-19
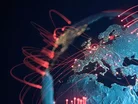
The global supply chain has experienced an unprecedented level of disruption and forced manufacturers to think about their operations in an entirely new way. Manufacturers are still under a significant amount of pressure to produce essential products like hand sanitizer, protective face shields, respirators and ventilators. Despite all these efforts, it has proven difficult to keep up with rapidly changing demand.
Digital transformation in the supply chain has to be about more than just cost-effectiveness. The ability to continue operating and fulfilling customer and partner obligations even under the most unexpected and challenging market conditions is equally important in an age where agility and resilience are paramount.
According to McKinsey1, digital manufacturing technologies will transform every link in the manufacturing value chain, from research and development, supply chain, and factory operations to marketing, sales, and service, and “advances in virtual and augmented reality, next-level interfaces, advanced robotics, and additive manufacturing are all opening the gates to digital disruption.”
Manufacturing Operations Transformation (MOT)
Many industrial manufacturing companies have started their transformation journey with plant and machine automation and the gains of productivity and process repeatability that brings. Plant equipment automation minimizes the amount of manual operations and maximizes the physical throughput. To further improve the utilization of equipment, plant operations have matured into using IT and software applications as the basis for improvement strategies such as replacing paper-based work instructions and data collection.
The use of software and IT, such as manufacturing execution systems (MES) has provided more benefits than increased operational efficiency through core application functionality. Historical data and modern big data analytics offer additional payback opportunities by providing optimization insights and facilitation of continuous improvement.
Visibility of operational execution and inventory status based on automatic data exchange with enterprise systems in near real-time enables better decision making and collaboration between plant and enterprise functions – and this advancement is also helping manufacturers to make faster changes and to adapt.
Collaboration across people and systems
A key factor for future manufacturing operations improvements is the effective collaboration of people and systems in a digital, automated and integrated fashion. Digital transformation of operational processes captures and transforms best practices into electronic workflows, to connect assets and systems, establish systematic people and system collaboration and to empower the mobile and next generation workforce.
Connecting systems together can also orchestrate process across functional domains (horizontal integration) and can integrate with business functions (vertical integration). Enforcing consistency of operational procedures and the automation of workflows with electronic records of manufacturing execution activities and data preserves the investments in existing plant systems while offering significant operational efficiency improvement potentials.
Adaptability through data
The primary enabler of an effective multi-site Manufacturing Operations Transformation is the enterprise-wide standardization of operational processes, enabled through the standardization of information technologies. Such IT harmonization is the foundation to digitally model, integrate, execute, and govern operational processes and related information flow consistently across multiple plants. Standardization of operational processes is possible with the following components:
- An open engineering and runtime platform, hardened for industrial use and designed for enabling integration of business, manufacturing operations and production processes and data.
- A broad suite of industrial applications scaling from rapid ROI equipment performance optimization to full manufacturing operations management functionality.
- A reusable operations process modelling approach, which standardizes all operations, simplifies deployment of processes to equipment, systems and people.
The role of a manufacturing IT platform is to provide adaptability to local plant nuances and a plant asset model which applications can use to blend human and automated activity in the execution of standardized processes and business rules. The platform adapts to individual local physical equipment and automation, while maintaining the data and information models of the processes and flow of data to other applications and towards the enterprise.
This transformation establishes a sustainable digital twin of the manufacturing plant which offers to further optimize execution of demand which is allowing manufacturers to shorten their lead times and reduce inventory and improve supply chain performance.
When consistently implemented across multiple sites the digital twin of the plant becomes the enabler for agility, velocity and traceability that can support the new business models, product and customer engagement that digital transformation is enabling at the business level.
Enabling empowerment and future proofing
From optimizing asset performance, to raising productivity, to elevating quality, there are countless reasons to pursue Manufacturing Operations Transformation. It is the continuation of transformational activities that align manufacturing IT systems across the business to provide both operational and business improvements. Improvement requires changing processes and systems, and continually training the workforce. This often requires replacing paper and legacy systems with software that provides automation, and ensures work processes are in-line with targets.
Modern Manufacturing Execution Systems deliver the platform for this transformation with agnostic connectivity to business systems, data lakes and automation and IIoT systems to deliver the next level of benefits though predictive analytics and prescriptive planning and scheduling.
While this digital transformation of the $10-trillion-plus global manufacturing sector will play out over a decade or more, pioneers are moving to drive bottom-line and top-line impact in the near term. Cloud computing–based tools also will allow suppliers to collaborate faster and more efficiently: an engine maker can share three-dimensional models of component design within its network, and each supplier in turn can share information about price, production timelines, quality and delivery.
Connectivity is the future – and available now. Having a built-in connectivity to existing plant floor systems, devices and equipment will eliminate inefficiencies, maximize profitability, and empowers your team to respond to future external disruptions.