Carbon-neutral energy automation & manufacturing at Comau
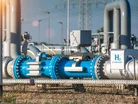
As a safe and highly efficient energy carrier, hydrogen is in an ideal position to boost the adoption of renewables worldwide, helping tackle various critical energy challenges. The reliable, zero-emission power source can fuel passenger cars, light buses, city buses, road buses, trucks, locomotives, forklifts, trailers and many other applications. Hydrogen fuel cell technologies can also be extended to distributed power generation and cogeneration, as well as ships, aviation and other non-automotive sectors.
In addition to acting as a cost-effective energy storage and transport solution, hydrogen offers an effective way to reduce carbon emissions for sectors such as long-haul transport, chemicals, and iron and steel in which other clean feedstock alternatives do not currently exist.
Here, Alessandro Piscioneri, Comau’s Global Head of Strategic Marketing Advanced Robotics & Digital Segments, tells us more.
Manufacturing with hydrogen energy
Electrolyzers are used in the production of hydrogen fuel through a process called electrolysis, when an electric current is passed through water, splitting the water molecules into hydrogen gas and oxygen gas.
“The assembly and production of electrolyzers and fuel cells tends to be slow, expensive, and labour intensive,” says Piscioneri. “From a technical point of view, electrolyzers enable the production of green hydrogen for applications in mobility and other sectors, whereas fuel cells generate electricity from hydrogen, and will be primarily used for mobility.”
To help mobilise the increased production and deployment of these technologies, Comau is working to industrialise manufacturing by developing a proprietary portfolio of solutions that can automate the main production steps, including cell preparation, stacking, compression, welding, leak testing and more.
“This will allow energy providers to scale-up production volumes while increasing the quality of the high-precision process. It will also help lower the production costs by up to 20%, according to internal estimates.”
Automation is important for several reasons despite the relatively low volume of fuel cells compared to batteries (internal projections show that the global demand for fuel cells should reach 200,000 units in 2026, whereas a new Gigafactory in Germany – just to provide a concrete example - is capable of producing battery packs for more than 500,000 vehicles annually).
“The first reason is related to the architecture of a fuel cell,” says Piscioneri. “The core, known as the fuel cell stack, consists of hundreds of repeated elements (100-300 cells per stack), whereas the cells themselves are composed of several layers – from 2 to 4 per cell based on our experience to date. Such intrinsic repetition is a key enabler for automation, as it leads to cycle times of 1-10 seconds per layer (depending on the product and plant productivity) during which each layer is picked, quality-checked and properly placed in the stack.”
The high levels of precision and quality that are required during the assembly process is another reason why automation can help improve fuel cell manufacturing.
“First of all, each cell must be aligned within a tolerance of 0.1mm and each component and layer is quality checked for surface and geometrical defects,” says Piscioneri. “Most manufacturers require full process traceability and until a stack has been sealed, many fuel cells necessitate adherence to clean room standards. Furthermore, fuel cell testing procedures are quite extensive since they have to cover both leaks and electrical operations, with some of the leak tests performed at high speeds.”
However, automation is not limited to the robotisation of the assembly process itself. “Digitalisation also plays a crucial role, as the storing of information at each step of the process (quality gates, visual inspections, field parameters) is vital to creating a database for detailed analytics. In this way, manufacturers can have the information they need to adjust the dynamics, refine the product, and hopefully, create a smarter, more efficient and less complex assembly process.”
Similar problems and opportunities are valid for electrolyzers, and in many cases, the assembly process is largely analogous to that of fuel cells.
“Cycle time is less demanding, as volumes are much lower (according to internal estimates, the global production of electrolyzers is expected to be 10 times less than fuel cells in 2026) but dimensions, weights and the number of layers per cell are much higher. An alkaline electrolyzer, for example, can weigh more than 40 tonnes, with cells measuring 1.5 metres in diameter and composed of more layers than fuel cells.
Given that automation is relatively new in this sector, manufacturers must face multiple challenges, such as how to precisely handle and align floppy components (gaskets, membranes, fabric and metallic meshes) at high speeds.
To address these challenges, Comau has initiated several laboratory tests and customer collaborations in the field.
“We are also applying many of the competencies and skills gained from delivering assembly lines for Body-in- White, battery modules and battery packs, along with specific technologies such as laser and resistive welding, visual inspection, leak testing and high-speed assembly, to design its dedicated solutions.”
Energy: Affordable and carbon neutral
According to the European Environment Agency, more than a quarter of the total CO2 emissions in Europe come from the transport sector. The move toward fuel-efficient vehicles powered by renewable sources is a concrete way to reduce greenhouse gas emissions and move closer to the EU’s goal of total mobility decarbonisation. Achieving this objective will require increasingly advanced skills and constant technological innovation from the industry players contributing to the hydrogen value chain.
“While it can be argued that automating what has traditionally been a manual manufacturing process is one of the biggest challenges for green hydrogen procurement, the careful management of the entire industrial process life cycle, from conceptual engineering to manufacturing and support services, is equally as important,” says Piscioneri. “Here, for example, Comau’s Simultaneous Engineering approach is key to helping its customers design their products in a way that will be easier and more cost effective when assembling them with automation.”
Comau won its first hydrogen fuel cell project in China for Shanghai Hydrogen Propulsion Technology (SHPT), a subsidiary of SAIC Motor to provide an advanced production line for a P4 hydrogen Fuel Cell stack, earlier this year.
“Featuring a proprietary high-speed, high-precision multi-axis stacking technology, the innovative solution simultaneously performs a series of pole piece stacking operations to manage the pick-up, code scanning, secondary positioning, and shell loading within 4 seconds. Similarly, the company recently implemented a project in EMEA that assembles fuel cells for light and commercial vehicles, and is collaborating with major manufacturers in various sectors, in other Regions, to support their product development and industrialisation plans via providing consulting and technology services.”
Based on internal estimates, Comau estimates the market will grow exponentially, from a few thousand fuel cell units deployed in 2020 to 1.2mn units by 2030, equivalent to more than 100 GW of hydrogen energy.
“To sustain such demand, two things have to happen: the number of manufacturers will need to increase and cycle times will need to decrease. Indeed, some of the world’s most well-known manufacturers are already planning a ten-fold increase in long-term productivity – from around 2 seconds per cell today to 0.2 seconds per cell in the future,” says Piscioneri. “To achieve this, however, automation will have to change significantly. If the current state-of-the-art for building stacks is high-speed, low payload robots, the market will move toward accelerated processes and the first stacking machines (similar to the roll-to-roll equipment used in packaging, electronics and li-ion manufacturing) within 5 years or so.”
In all cases, the goal is the same. Speed up the production of reliable, emission-free energy and reduce the cost of manufacturing fuel cells and electrolyzers.
- Digitalisation as a Strategy to Attract and Retain WorkersDigital Factory
- UPDATED VENUE & DATE – Manufacturing LIVE Chicago 2025Sustainability & ESG
- ABB Cuts Industrial E-Waste in Quest for CircularitySustainability & ESG
- Why Are Manufacturers Doubling Down On Digital Twins?Digital Factory