Uniting manufacturing & modern environmental standards
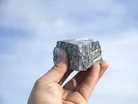
Galvanising, the process of applying a protective zinc coating to steel products, is a crucial step for many manufactured products and has been used for centuries. The British steel industry used 10,000 tonnes of zinc per year to produce galvanised steel as far back as 1850.
“This process is widely appreciated for its excellent corrosion resistance, cost-effectiveness and ease of maintenance,” explains Peter Chifo, President at Superior Technologies, Inc. “However, in addition to the substantial demand it creates for resources and raw materials, galvanization generates harmful by-products, including toxic heavy metals, gases and sludge, during production. The environmental consequences of the galvanization process are not adequately considered by producers and often go unnoticed, despite their severity.”
Here, Chifo dives into the environmental challenges of galvanising methods and possible solutions.
Tools and strategies for improving galvanising processes
While galvanising technologies have been well-established for many years, there are areas where improvements can be pursued to align the process with environmental and government requirements.
“Government agencies are increasingly focused on environmental sustainability, worker safety, and the reduction of hazardous materials,” he says. “By proactively evaluating these categories and seeking guidance from industry experts, manufacturers can adopt more thoughtful and cost-effective approaches to meet these requirements.”
Three key areas which manufacturers can focus on to improve environmental sustainability are zinc consumption, energy efficiency and automation.
Zinc consumption
To promote the sustainable use of zinc, efforts should focus on reducing zinc consumption during galvanisation.
“Optimising coating thickness and efficiently recycling zinc from galvanising byproducts can help extend the lifespan of this valuable resource,” Chifo explains. “Factories can most clearly improve upon this through equipment upgrades; existing processes and equipment in many steelmaking plants can be more than 40 years old and upgrading or retrofitting with more efficient equipment can lead to improved performance, cost savings, and enhanced environmental friendliness. For instance, maintaining high temperatures in large hot dip kettles during steel tube production requires significant fuel consumption and produces high levels of zinc byproducts. In contrast, inline galvanising kettles are smaller, more efficient, and apply more even and consistent coating thickness.
Energy Efficiency
Galvanising processes can be energy-intensive, with certain methods consuming more energy than others. By improving energy consumption in the processes surrounding the actual zinc coating, manufacturers can reduce costs and enhance environmental sustainability.
“For example, surface cleaning and preparation methods, such as acid pickling, mechanical cleaning, high-pressure water jetting, abrasive cleaning, thermal cleaning and chemical cleaning, can all be enhanced to further improve the efficiency and effectiveness of surface preparation, leading to better adhesion and corrosion protection during galvanising itself.”
Automation & AI
Introducing automation and AI can lead to a more efficient, precise and safe galvanising process.
“Automated systems for material handling, coating thickness measurement, quality control and other aspects can enhance production rates, limit scrap and minimise human error. These changes have the impact of higher productivity, accuracy, precision and worker safety.”
Galvanising processes face several challenges in fulfilling environmental requirements, but efforts to optimise zinc consumption, improve energy efficiency and introduce automation can lead to more efficient and environmentally sustainable methods going forward.
“By leveraging tools such as equipment upgrades and automation systems and proactively preparing for government regulations, manufacturing companies can improve their galvanising processes for a sustainable future.”
*************************************************
For more insights into Manufacturing - check out the latest edition of Manufacturing Magazine and be sure to follow us on LinkedIn & Twitter.
Other magazines that may be of interest - Healthcare Digital.
*********************************************
BizClik is a global provider of B2B digital media platforms that cover 'Executive Communities' for CEO's, CFO's, CMO's, Sustainability Leaders, Procurement & Supply Chain Leaders, Technology & AI Leaders, Cyber Leaders, FinTech & InsurTech Leaders as well as covering industries such as Manufacturing, Mining, Energy, EV, Construction, Healthcare + Food & Drink.
BizClik, based in London, Dubai & New York offers services such as Content Creation, Advertising & Sponsorship Solutions, Webinars & Events.