A Rundown of Bosch’s Project SDM4FZI
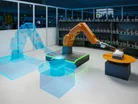
On the 17th and 18th of September the Stuttgart Innovation Days 2024 was held in Germany at the Maritim Hotel of the Baden-Württemberg state capital.
This conference, organised by the Institute for Control Engineering of Machine Tools and Manufacturing Units (ISW) was created for experts in the fields of science and industry.
The 2024 theme was software-defined manufacturing, with the aim to drive digitalisation as a tool to support economic production despite volatile markets.
The Bosch Research team was there, presenting the work of an innovative project: Project SDM4FZI.
What is Project SDM4FZI?
Project SDM4FZI ( Software-Defined Manufacturing for the Vehicle and Supplier Industry) is part of Bosch’s broader push towards Industry 4.0, focusing on making manufacturing process more automated, flexible and adaptable through IoT.
Funded by the Federal Ministry for Economic Affairs and Climate Action, this was a large collaborative project with a broadly based consortium, where around 30 project partners carried out fundamental and applied research. Bosch Research took on the role of consortium lead.
The project focused specifically on the automotive and supplier industry, seeking to enhance them through:
- Software-defined processes
By enhancing hardware through software, manufacturers can more easily scale production based on demand and implement faster changes. This enables greater production line adaptability and flexibility.
- Smart manufacturing
Integrating AI and IoT technologies makes manufacturing more intelligent and interconnected, with the data generated being used for real-time corrections, predictive maintenance, quality control, analysis and the creation of more efficient workflows.
- Tools to improve supplier collaboration
Software-defined solutions can also help streamline supply chain management and enhance communication. The company focuses on improving collaboration between suppliers and manufacturers.
Some of the creations that emerged from the project included a reference model as a blueprint for digital twins and virtualised control technology used to move machine control from the edge cloud to the control cabinet.
During the two days of the conference the Bosch research team also discussed the tool changer they’d created based on asset administration shells on the digital twin. This was developed in cooperation with HOMAG, Bosch Rexroth, ISG Industrielle Steuerungstechnik, and ISW.
The Bosch team also discussed how software-defined manufacturing will be critical to navigating trade crises and unstable supply chains, sharing their findings on how to bring the above applications to market.
“Now we have come full circle; for us, the presentation of our results at the Stuttgart Innovation Days is a nice and successful conclusion to the project,” says Johannes Fisel, SDM Project Manager.
What were the outcomes of the project?
Project SDM4FZI demonstrated the revolutionary power of software-defined manufacturing ( SDM) , particularly showcasing its applications in the automation and supply sectors. It proved that SDM leads to:
- Increased flexibility
Bosch has demonstrated that with SDM4FZI, production systems can adapt faster to new product variants without major hardware changes.
- Enhanced efficiency
Through real-time data analytics and predictive maintenance, Bosch has reported increased uptime and reduced waste.
- Better quality control
AI-driven monitoring systems allow for earlier detection of defects, leading to improved product quality.
SDM4FZI is part of Bosch’s broader move toward a digitally connected factory where software plays a central role in production, helping to optimise costs, enhance productivity, and reduce the environmental impact of manufacturing.
Bosch is continuing to pursue this strategy globally, with Bosch Digital Twin Industries joining forces with the largest Oil & Gas organisation in Algeria to deliver innovative solutions. The company seeks to advance 𝗙𝗶𝘁𝗻𝗲𝘀𝘀-𝗳𝗼𝗿-𝗦𝗲𝗿𝘃𝗶𝗰𝗲 (𝗙𝗙𝗦) and 𝗥𝗲𝗺𝗮𝗶𝗻𝗶𝗻𝗴 𝗨𝘀𝗲𝗳𝘂𝗹 𝗟𝗶𝗳𝗲 (𝗥𝗨𝗟) assessments using digital twin technology powered by physics and AI.
This collaboration seeks to set a new benchmark in integrity for critical equipment and asset performance management, and will be showcased at Stand G24 at NAPEC, the Africa & Mediterranean Energy & Hydrogen Conference which begins today.
Make sure you check out the latest edition of Manufacturing Digital and also sign up to our global conference series - Manufacturing & Mobility LIVE
Manufacturing Digital is a BizClik brand