Schneider Electric: Benefits of Software-Defined Automation
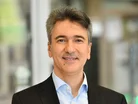
After National Manufacturing Day last Thursday, it's clear that software and automation will play a critical role in driving the sector's development in the UK.
With this in mind Manufacturing Digital spoke to Ali Haj Fraj, SVP Digital Factory, Industrial Automation at Schneider Electric, to learn more about the benefits of software- defined automation to wider manufacturing.
How can digital transformation transform operations in the manufacturing sector?
The manufacturing industry has faced a wave of challenges in recent years. There is a skills shortage, supply chain challenges and changing customer demands.
One of the greatest challenges, however, is the sectors' reliance on legacy technology systems which were often installed decades ago.
Today many manufacturers find themselves with little flexibility and a great deal of complexity - managing hundreds if not thousands of pieces of hardware, all of which must work together seamlessly in production.
This is a lot to manage and even more to maintain. But times are changing.
In today’s technical ecosystem, digital transformation is no longer a buzz word, it is progressing at pace and has the power to transform the industrial ‘design,’ ‘optimise,’ and ‘operate’ cycle, maximising efficiency, and minimising errors.
Industrial enterprises must embrace digital transformation to accelerate their productivity and enhance flexibility.
With manufacturers and engineers now seeking technology that helps them to streamline tasks, reduce costs and enables them to prepare for a smoother transition into the digitalised future, digital transformation is of the upmost importance in helping manufactures prepare for the industry of tomorrow.
What is Software-Defined Automation (SDA) and how does it impact industrial operations?
Software-defined automation (SDA) is an approach that aims to transform operational technology by decoupling hardware and software.
Under SDA, industrial companies can choose the automation technology they want and mix and match the applications into one seamless system.
This approach, brought along with industrial digitalisation, allows devices and equipment to be freely connected across architecture layers regardless of manufacturer.
Hardware and software can be selected independently of each other, and this fundamentally changes the approach to automation and design.
If adopted widely, SDA will have a huge impact on accelerating innovation and improving operations across the globe.
What are the business benefits of Software-Defined Automation (SDA)?
Once leveraged, SDA enables manufacturers to enhance the scalability, adaptability and resiliency of their operations, whilst opening new opportunities to attract, retain and grow top talent – a crucial component given today’s current skills shortage.
Firstly, SDA technologies, like virtual controllers, are more scalable than traditional hardware-based tools, enabling manufacturers to easily update them when needed. Given that during SDA hardware and software are decoupled, this removes the need for updates to require a system shutdown like they would in traditional hardware architecture.
This reduces downtime and increases staff productivity as operations can continue to run smoothly.
In turn, this also enhances the adaptability of tools as manufacturers can simply update and reprogram functions to keep up with changing market demands.
SDA also boosts the resiliency of tools as it allows engineers to easily add on additional automation workloads without downtime. For example, if a controller was to fail, the automated system would switch over to another containerized virtual controller and continue operations as normal, allowing manufacturers to grow beyond the basic primary and backup model.
Finally, when looking at the wider industrial landscape, SDA also supports workforce transformation, empowering a highly skilled, and engaged workforce. The automation engineers of today are used to working with modern tools and in IT-focused environments that promote efficiency, they expect to work using such tools over legacy technology and outdated systems.
As such, the manufacturers that embrace SDA will welcome in the manufacturing talent of the future, boosting employee retention and satisfaction – this is a vital factor to future-proofing the industry.
How does SDA help to promote the practice of ‘virtualisation’?
In a traditional sense, the term ‘virtualisation’ is used to describe a scenario where several virtual machines (VMs) are set up on a single server. But in the industrial sense, the premise is much the same – a move from physical to virtual.
A software defined automation model allows automation (e.g. PLC) functions to run on various platforms instead of being tied to proprietary hardware. This has given rise to ‘Soft PLC’s’ and the capability to use almost any available computing resource to execute automation functions.
The benefits virtualisation provides to manufactures are far ranging, enabling them to streamline and automate many standard processes such as consolidating Programmable Logic Controllers (PLC), Human Machine Interfaces (HMI), and Industrial PCs (IPC) on one hardware platform. But this is just the beginning.
Beyond operational benefits, virtualisation can help businesses make significant reductions in hardware costs.
Fewer physical servers mean less hardware to maintain, operate and repair – boosting productivity and allowing staff to focus on more hands-on, value-adding activities and cutting operational costs.
Additionally, ‘virtualisation’ helps organizations strive towards better organisational sustainability.
The consolidation of computing and storage resources into a set of central services reduces and industrial company’s total energy use and Scope 2 Green House Gas emissions.
What role do digital twins play in boosting operational efficiency through SDA?
Digital twin models are a vital component of SDA and play a critical role in improving operational efficiency by reducing costs across the industrial sector.
In essence, a digital twin is a virtual replica of a real-world object or process, created to precisely reflect its physical counterpart.
In the hands of manufacturers, this technology allows for new tools, machines, and processes to be tested and trialed in a virtual setting that mirrors a real one before they are built and commissioned in the physical world.
This process helps to reduce errors and saves both time and money, as all testing occurs in a virtual environment. By testing designs in the virtual world first, engineers can observe how the digital twin performs and review the impact it would have on operations if implemented in the real world.
By investing digital twin models, manufacturers no longer need to experiment with physical hardware to achieve desired results. This can significantly increase efficiency as engineers can experiment with tools digitally instead of taking the traditional lengthy, costly, manual approach. They are free to get on with more fulfilling, valuable work, saving time to market by up to 50% and commissioning time up to 60% when compared with traditional approaches.
How can SDA help manufacturers to transition to soft programmable logic controllers?
Enabled by Software Defined Automation the ‘virtualised’ PLC approach described above offers access to a new way of automating machines and processes, a ‘soft PLC’ or a hardware-agnostic, software-based controller which can be run on any Windows or Linux server, industrial PC (iPC) or microcomputer, no matter the supplier.
Multiple instances of these virtualised controllers can be installed on the same piece of hardware and configured, deployed, and maintained both simultaneously and independently from one another.
This virtualised strategy enables changes to be made to machines and processes without pausing production, therefore reducing downtime, lowering costs, and providing the crucial flexibility and agility needed to succeed in today's demand-driven, consumer landscape.
This process simplifies and streamlines the launch of new processes and the replication or modification of existing ones.
By leveraging proven, reusable engineering to build automation application programs, it significantly reduces time-to-market, enhances engineering efficiency, and provides a competitive advantage.
Can you provide any real-life examples where SDA has helped to streamline business operations?
Companies like the robotics packaging company Unilogo, a robotics company that supply packaging machines to global consumer packaged goods companies, are using software-centric automation to optimise complex processes.
By leveraging Schneider Electric’s EcoStruxure Automation Expert, specifically the Lexium MC12 multi-carrier, the Delta robots, and EcoStruxure Machine Expert Twin, Unilogo have been able to synchronise filling lines at great speed, giving its customers fast changeover times and reach 200 ppm – increasing time to market.
EcoStruxure has also helped Unilogo to program machines, helping the company create digital twins to do simulations, and deliver quality equipment to their customers.
******
Make sure you check out the latest edition of Manufacturing Digital and also sign up to our global conference series - Procurement & Supply Chain 2024 & Sustainability LIVE 2024
******
Manufacturing Digital is a BizClik brand.
- The University Manufacturing Circuit Boards from LeavesSustainability & ESG
- Schneider Electric's Commitment to Sustainable ManufacturingSustainability & ESG
- Lenovo & Saudi Alat Building Green Manufacturing FacilitySustainability & ESG
- Nissan Brings Biodiversity to the Factory through RewildingSustainability & ESG