Boston Dynamics Robot Dog Helps 'Spot' Failures Early on
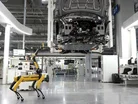
Spot is the four-legged industrial robot that according to its creators, 'never stops learning'.
Designed to streamline maintenance and enhance safety, Spot is the result of a shared goal between Boston Dynamics and Foxmere: to improve manufacturing operations through robotics.
Spot autonomously moves around a range of factory environments, performing safety and maintenance tasks.
The robot can be retrofitted with advanced tools and sensors, enabling manufacturers to monitor equipment health and detect potential failures before they result in expensive downtime.
Using the latest technology, this robot enables manufacturers to improve factory environments whilst safely retaining legacy equipment.
Tom Cash, Director of automation parts supplier Foxmere shared more with Manufacturing Digital.
Sound waves & imaging: spotting the problem with Spot
"Plant maintenance and operations teams currently use various strategies, such as routine inspections and scheduled maintenance, to mitigate against downtime," says Tom.
"However, the challenge remains: How can organisations identify potential problems even sooner?"
Many manufacturing technologies are currently being explored as means to address this challenge, including AI.
Tom proposes another fascinating possibility- using ultrasound inspection.
"This technique involves the use of ultrasonic sound waves — frequencies that are typically above the range of human hearing — to detect early indicators of mechanical failures," he says.
"As equipment operates, it generates sound signatures that can subtly change as wear and tear occurs.
These changes might include variations in pitch, intensity or frequency, which are often imperceptible to the human ear.
"Using advanced tools, like ultrasonic sensors or imaging devices, operators can capture these sound signatures during routine inspections.
"The data collected is then analysed to identify anomalies or deviations from normal operating conditions."
Spot performs these ultrasonic inspections of rotating equipment using the Fluke SV600, which captures data without installing additional inline sensors or requiring more contact sensors.
By tuning in to these sound waves and vibrations, manufacturers will be able to catch when:
- Components have become misaligned.
- Bearings have begin to perish.
- When there's risk of air leaks within compressed air systems.
Using Spot to detect these changes feels especially fitting with its dog-like appearance, as the animal is known for its superior hearing.
Capturing a whole new reality
Tom also highlights another valuable feature spot has: reality capture.
Through reality capture, the robot can render 3D digital models of objects that exist in the physical world by merely capturing their shape.
"Whether using camera-equipped drones or ground-based laser scanners, it captures every detail of a scene by collecting data from billions of reference points," Tom explains.
"This process is consistent across different architectural features, meaning that the complexity of the structure does not affect the time or data generated."
He goes on to highlight the ways in which 3D data can boost manufacturing, leading to broader gains in productivity, efficiency and organisation.
"Using 3D data in industrial settings enhances factory management," he adds.
"By creating accurate visual representations of existing spaces, teams can improve the design of new equipment or production systems, especially in brownfield sites where modifications to current structures are required.
What’s more, accurate modelling aids in effective planning and helps identify potential conflicts during equipment installation, ensuring that projects run more smoothly and efficiently."
Reality capture is also a valuable training resource for employees, mirroring the benefits we've seen with digital twins and AR/VR training solutions.
"Reality capture can provide them with a thorough understanding of the facility before they arrive on-site, leading to a more confident and effective workforce," Tom says.
Integration with legacy systems
Many manufacturers continue to operate within legacy systems.
These systems are often foundational to the manufacturer's process and factories, making rehauling them a major commitment.
For many manufacturers doing so isn't viable or valuable, causing them to face challenges with IT/OT integration.
Spot sidesteps those challenges by integrating itself into the legacy system framework.
"Spot’s new features allow it to capture data about equipment health and apply its laser scanning capabilities through Orbit, a fleet management software," explains Tom.
" This, in turn, allows users to conduct reality capture missions alongside regular inspections.
"Using the Leica BLK ARC payload, operators then record these missions to capture detailed 3D data of the environment.
"After the data is collected, it can be edited, scheduled and monitored through the Orbit platform for better workflow."
Tom explains that Orbit critically supports legacy system integration, meaning manufacturers can keep their existing infrastructure while still benefitting from industrial robots like Spot.
Industrial robots which are providing profound benefits across manufacturing- including in the growing EV sector.
Joining robots like Rover
Spot belongs to a litter of robot dogs that have come out of Boston Dynamics, including Rover.
Manufacturing Digital reported on Rover earlier this year, highlighting the model's role in JLR's EV testing facility.
The robot is being utilised to enhance the battery manufacturing process, performing tasks including removing particles from battery cells, a precise task humans are unable to perform.
Rover does up to 24 daily patrols at JLR's facility, ensuring equipment is operating seamlessly and enabling on-site engineers to focus on tasks like analysis and maintenance.
As industrial robots grow more commonplace across manufacturing operations, we're going to see more intelligent examples on the factory floor- including further robot dogs.
Explore the latest edition of Manufacturing Digital and be part of the conversation at our global conference series, Manufacturing LIVE.
Discover all our upcoming events and secure your tickets today.
Manufacturing Digital is a BizClik brand.
- Taking the industrial metaverse From Concept to RealityDigital Factory
- KUKA-owned Visual Components Enhances 3D Simulation ToolDigital Factory
- Schneider Electric to Showcase 2025 Offerings at SPSDigital Factory
- From Cryogenics to Cleanrooms: Methods to Keep Robots CleanProduction & Operations