From Cryogenics to Cleanrooms: Methods to Keep Robots Clean
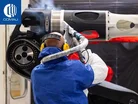
We all know the benefits of industrial robots like greater productivity, efficiency and safety.
But one aspect of maintaining a robot fleet that isn't discussed enough is upkeep-ergo, the need to clean them.
On the one hand, robots make manufacturing cleaner and reduce contamination risks as they decrease the amount of human hands touching products.
On the other, robots create new contamination risks.
These risks must be mitigated, especially in highly regulated environments like food and pharmaceutical manufacturing where contamination can seriously impact product safety and public health.
In such environments, strict hygiene standards must be adhered to as any breach of cleanliness could lead to severe contamination risks, resulting in product recalls, financial losses, or even harm to consumers.
Food & Pharma: cleanliness is no joke
In pharmaceutical manufacturing, robots are often employed in sterile environments where precision is essential. Contamination could compromise the integrity of medications or vaccines, making them ineffective or dangerous.
Even trace amounts of foreign particles or bacteria could spoil an entire batch of pharmaceutical products.
Robots used in this setting must be constructed from materials that are easy to clean and resist corrosion from harsh chemicals, and their design should minimize the risk of harboring contaminants.
Similarly, in food manufacturing, robots are increasingly used to handle raw ingredients and packaged goods.
Ensuring robots are kept clean is vital to preventing bacterial contamination, such as salmonella or E. coli, which can cause foodborne illnesses.
Any residue or bacteria left on robotic arms could easily transfer to food products, putting consumers at risk.
Approaches to keeping robots clean
Regular cleaning and sanitisation of industrial robots are mandatory.
Regulatory standards such as GMP (Good Manufacturing Practice) in pharmaceuticals and HACCP (Hazard Analysis Critical Control Point) in food production exist to enforce this.
To enable industrial robots to be cleaned through washdowns they are typically waterproof and built from non-porous materials like stainless steel.
Some manufacturers invest in comprehensive cleaning services to ensure the cleaning process is thorough.
There are companies that go even further by investing in solutions like protective covers.
Such covers, like the above example by Evotec, protect the product and robot from spillages and contamination (whilst making it look like a giant, very clean blue worm).
Some go even further, looking to cleanroom robots and exploring the benefits of cryogenic cleaning.
Cleanroom robots
ABB’s cleanroom robots are designed for manufacturing environments that need the highest levels of cleanliness and the lowest levels of particle emission without sacrificing speed or performance.
Key features include hygienic paint and a sealed body to prevent leakage of contaminants such as grease, oil and particles, together with a mechanical design that minimizes gaps between the robot’s joints to discourage the growth of bacteria.
Certified to ISO 14644-1, these robots also provide reliable, fast performance to boost productivity and quality manufacturing.
ABB's industrial robots are deployed across industries including life sciences, healthcare, medical devices, biotechnology, pharmaceuticals, semiconductors, and electronics manufacturing.
Comau cleaning through cryogenics
Aiming to enhance the efficiency of industrial processes and create a more comprehensive cleaning process, Comau started experimenting with cryogenics for cleaning robots and spare parts before painting.
The manufacturers pilot project was carried out in collaboration with Cryos, a leader in dry ice blasting and Camic, a supplier specialising in industrial painting.
Comau has discovered from this pilot and internal studies that cryogenics have significant cleaning benefits.
Using dry ice instead of water washing not only better preserves robot performance but also cleans every facility-from parts to gears-far more thoroughly.
This approach also saves water, reduces energy consumption and eliminates the release of harmful substances into the environment.
"By adopting this new process, Comau wants to increase customer satisfaction and offer increasingly efficient, durable and sustainable products. Indeed, quality and sustainability are fundamental foundations of all Comau activities," says Salvatore Lorusso, Quality Manager for Engineering and Sustainability Ambassador.
"The adoption of this technology is part of a sustainability journey that Comau is continually pursuing and integrated within its divisions to achieve increasingly concrete and effective ESG (Environmental, Social, Governance) practices."
Cryogenic blasting captures the CO2 emissions generated by manufacturing plants, liquefying and freezing it into pellets of varying sizes. No chemical agents like degreasers or water is required in this process, leaving no residue on the robots treated surface.
Because dry ice is non-abrasive it doesn't damage the treated parts. Not only that it actually improves the resistance and adhesion of the paint on the robot's surface over a gradual period of time.
By eliminating the whole drying process, a cryogenic approach also saves time, resources and costs.
Finally cryogenic blasting isn't electronically driven, so it allows for comprehensive cleaning without the risk of plant downtime and impacts on production. This approach not only reduces part cleaning but it also shortens project completion times.
"A sustainable future is only possible when concrete action is taken. This is why Comau is firm in reducing GHG emissions, minimising energy and water consumption and integrating its activities into the circular economy." Salvatore explains.
"As an example, Cryogenic blasting with dry ice enhances robot performance over time by thoroughly cleaning facilities without water or harmful chemicals. Using CO2, a by-product from manufacturing, this method leaves no residue, reduces energy consumption, and shortens cleaning cycles.
"Non-abrasive and safe for energised equipment, it prevents damage, improves paint adhesion,and eliminates the need for drying. This process not only preserves the integrity of treated parts but also enhances operator safety and reduces environmental impact.”
******
Make sure you check out the latest edition of Manufacturing Digital and also sign up to our global conference series - Procurement & Supply Chain 2024 & Sustainability LIVE 2024
******
Manufacturing Digital is a BizClik brand.
- ABB & Microsoft Launch Generative AI Copilot for IndustryAI & Automation
- ABB & NKT: Electrifying World's Largest Submarine CableSustainability & ESG
- ABB & Cemex: Bespoke Retrofitting to Drive Energy EfficiencyProduction & Operations
- Top 10: Manufacturing Accomplishments of 2024Procurement & Supply Chain