Framence GmbH: Pioneering Photorealistic Digital Twins
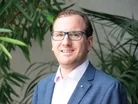
Please Introduce yourself and your role
I’m the CEO and co-founder of Framence.
I've been working in the field of software for real estate and asset management for nearly 20 years now. My background and experience in this industry have provided a strong foundation for what we do at Framence, allowing us to develop innovative solutions that address the unique challenges faced by businesses managing complex assets.
What does Framence do and what inspired its creation in 2019?
Framence specializes in creating digital twins of complex technical installations and assets.
The idea for Framence emerged from our extensive experience in real estate and asset management. We observed that many of our clients faced significant challenges when it came to documenting their complex technical installations in a timely and cost-effective way.
Existing solutions were either not up to the quality standards required or were prohibitively expensive.
We saw a clear need for a better solution, and that’s what led us to create Framence in 2019.
Our goal has always been to provide businesses with a powerful tool that simplifies documentation while maintaining the highest quality at a reasonable cost.
How does creating a photorealistic digital twin work?
The process of creating a photorealistic digital twin with Framence is simple and efficient, making it accessible to virtually any organisation.
It starts with capturing photos of the buildings and facilities using a standard digital camera, smartphone, or even a drone. The method is simple enough that even untrained personnel can handle the task, allowing easy data collection for the creation of the digital twin.
Our team can of course assist customers, if needed. Once the photos are taken, they are uploaded to the software. Our advanced AI-based algorithms automatically position the images to create a photorealistic digital twin, accurately representing the technical assets without manual intervention. After the twin is generated, it allows virtual navigation through the facility, similar to a "Street View" experience.
This reduces the need for on-site visits, improving efficiency and reducing costs by enabling many tasks to be performed remotely. As facilities evolve, the digital twin can be updated by simply taking a photo of new or changed assets with a smartphone. The AI algorithms automatically update the twin in real-time. Moreover, a timeline feature enables the viewing of past states and tracking of changes, making manual updates unnecessary and ensuring a continuously accurate representation.
You offer Framence as a platform, technology and a service. Can you take me through the differences between these offerings and why you provide them?
Sure. The platform serves as the single point of data access. It’s where all the geometric data, along with the location-based information of assets, is stored and accessed. This makes it easy for users to have all relevant data in one centralised space.
The technology refers to what powers the platform behind the scenes. It encompasses not just our own software solutions but also the nearly 40 years of IT and project expertise we bring to the table. We ensure robust data security through features like access controls and user roles, and we make sure our technology integrates seamlessly into existing IT environments, which is critical for many mid-sized and large companies.
Lastly, the service aspect is twofold. First, while our philosophy is that customers should ideally create their digital twins themselves, we can always assist them, either directly or through our global network of partners. Second, we offer services to help customers integrate the digital twin platform into their existing IT infrastructure. Only by embedding the digital twin into the current IT landscape can it truly function as a comprehensive, single point of data access.
How are Framence's data handling and AI capabilities useful to manufacturers?
One of the major issues we’ve seen in manufacturing is that specialised staff often spend 20-30% of their time just searching for information. With our platform, all the relevant data is localised directly to the corresponding asset and is immediately accessible. This streamlines the process, saving a significant amount of time and allowing teams to focus on more critical tasks.
In addition, our AI capabilities are designed to automatically recognize changes, detect deviations, and identify potential problems, such as corrosion, spills, or undocumented new installations.
This proactive approach allows issues to be addressed before they escalate, while freeing up specialised staff to focus on more strategic and value-added activities. Essentially, the AI acts as an intelligent assistant, ensuring the assets and the photorealistic digital twin are always up-to-date and in optimal condition.
How can photorealistic digital twins transform building and plant operations?
Primarily by saving the valuable time of critical staff – which is a resource that nearly all companies are struggling to manage effectively. Photorealistic digital twins streamline processes like onboarding, making it easier for new employees to familiarise themselves with the layout and operations. They also play a crucial role in maintenance and troubleshooting, allowing staff to quickly identify and resolve issues without unnecessary delays.
Furthermore, planning processes become much faster, as teams can visualise changes and improvements in a highly accurate digital environment before implementing them.
One of the most powerful aspects of our photorealistic digital twins is that they allow customers to be "on site in seconds." This virtual access reduces the need for physical presence, speeding up decision-making and operational efficiency, whether for inspections, planning, or problem-solving.
Beyond factories and the manufacturing industry- what other applications could photorealistic digital twins have?
We see them being incredibly useful in any industry where complex technical assets are involved. For example, they can be a game-changer in oil and gas, where large-scale, intricate installations need constant monitoring and maintenance.
Similarly, in infrastructure sectors like ports and airports, digital twins can streamline operations, improve maintenance, and enhance safety protocols. They're also highly valuable in the utilities sector, where managing vast networks of assets is crucial for efficient service delivery.
Even municipalities can benefit from digital twins, as they provide quick access to critical information about public infrastructure, helping with everything from emergency response to long-term urban planning.
You were a winner of the 2024 Factory Innovation Award and last year won the ‘Most Advanced Digital Twin’ award at the World of Digital Built Environment conference. Can you tell me about some of the work you’ve done, particularly with your global partners, that has led to this recognition?
We are incredibly proud of these achievements, and they reflect the global impact that our digital twins are having. The core problems that digital twins solve—improving asset management and operations—are universal, and we've noticed that these challenges exist across industries and regions worldwide.
These awards wouldn't have been possible without our fantastic customers. Together, we work closely to identify the most pressing issues in their operations and develop innovative solutions. A great example is our work on fully automated tag recognition using AI. Many critical assets in factories and plants are already tagged in the physical world. We've developed a system where our AI recognizes these tags in photographs, automatically linking them to third-party systems without the need for manual input. This allows us to localise and link important information effortlessly, saving time and reducing errors.
Moreover, our partnerships span various industrial sectors and economies, each with its own unique approach and challenges. Collaborating with such a diverse range of partners helps us identify common themes and problems that we can solve together, driving innovation and ensuring our solutions are adaptable on a global scale. This collaborative approach has been key to the recognition we’ve received.
Framence helps enhance the speed and accessibility of generating digital twins. Do you think it can help address the sector’s digital skills gap?
Certainly. One of our primary goals with Framence is to make the platform and the data it contains as accessible as possible, which directly helps in addressing the digital skills gap. Right now, anyone can access all the relevant information through a standard web browser, whether they're using a workstation, tablet, or even a mobile phone.
This ease of access ensures that employees don’t need specialised training to interact with the photorealistic digital twins, making it simpler for teams across the organisation to benefit from the technology.
We’re also experimenting with AR and VR technologies in some of our pilot projects. These emerging technologies have the potential to make data access even easier by creating more immersive and intuitive ways for people to interact with digital twins.
As AR and VR evolve, they could further reduce the need for specialised digital skills, making digital twins more accessible to a broader range of users across industries.
Digital twins are dramatically changing how manufacturers approach engineering and design. Would you say that photorealistic twins are the next evolution?
I wouldn’t necessarily call them the next evolution, but rather a facilitator for a range of new technologies.
Photorealistic digital twins play a crucial role in breaking down data silos by connecting all the data stored in those silos and making it easily accessible to other processes. This eliminates the need for complex and cumbersome interfaces, enabling seamless data integration across the organisation.
Additionally, autonomous mobile robots (AMRs), like drones or four-legged robots, require a 3D environment to operate effectively.
That’s where our photorealistic digital twins come in—they provide that environment, but without the need for the heavy, time-consuming efforts typically required to create such detailed environments.
******
Make sure you check out the latest edition of Manufacturing Digital and also sign up to our global conference series - Procurement & Supply Chain 2024 & Sustainability LIVE 2024
******
Manufacturing Digital is a BizClik brand.