JLR Invests US$654m To Upgrade Halewood Facility For EVs
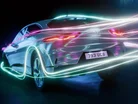
Jaguar Land Rover (JLR) has embarked on a transformative journey with a significant US$654m investment to upgrade its historic Halewood facility.
The transformation aims to transition the site into a state-of-the-art EV production hub, aligning with JLR's ambitious sustainability goals.
With this investment, JLR plans to eliminate 40,000 tonnes of CO2e from Halewood's industrial footprint by 2031, pushing the boundaries of automotive innovation and green manufacturing.
Driving towards a sustainable future
This bold initiative is part of JLR's Reimagine strategy, a comprehensive plan to electrify all its vehicle brands by 2030.
The ultimate aim is to achieve carbon net zero across its entire supply chain, products, and operations by 2039. As JLR continues to reshape its business model, sustainability remains central to this evolution.
A key component of these efforts is the adoption of renewable energy.
JLR plans to install 18,000 photovoltaic panels at the Halewood site, which will generate an impressive 8,600 GWh of energy.
Renewable energy will supply about 10% of the site's energy needs. JLR aims to generate over a third of its global energy requirements from self-produced renewables as part of its broader strategy.
The installation of solar car parks at Halewood offers low-carbon charging solutions for employees and visitors, representing another significant step towards a sustainable future.
Reducing emissions via innovation
Halewood's paint shop has undergone a major upgrade, leading to a daily reduction of 2.4 tonnes of CO2e and an annual savings of 565 tonnes.
The introduction of a new hydrogen-enabled boiler sets a strong precedent for future decarbonization initiatives at the plant.
To further its sustainability efforts, JLR is transferring thousands of refurbished pieces of equipment from its Castle Bromwich site to Halewood, including robots, automated vehicles, and various joining and calibration tools.
This redeployment initiative has already saved the company over US$21m.
By repurposing 44 SCA adhesive pump systems alone, JLR anticipates savings of US$1.9m, reducing costs by 62% compared to purchasing new systems and cutting CO2 emissions by 77%, which is roughly equivalent to saving about 207 tonnes of carbon.
Commitment to circular economy principles
"At JLR Halewood, we're driving transformation through circular principles: use less, extend the life of what we have and reuse wherever possible," says Reuben Chorley, JLR's Sustainable Industrial Operations Director.
"By repurposing equipment from other sites, we're not just cutting costs but making smarter, more sustainable choices.
"We're ramping energy efficiency and embracing renewables with exciting plans to integrate hydrogen into our operations. With cutting-edge technology and a highly skilled team, Halewood is set to be a game-changer in our journey to net zero."
Empowering the workforce
JLR's transformation goes beyond infrastructure, focusing on upskilling the manufacturing workforce.
The company invests US$26m annually in its Future Skills Programme, providing employees with essential knowledge in emerging systems and technologies.
The new training center at Halewood emphasizes High Voltage Training (HVT), preparing workers for battery assembly processes vital to EV production.
Nearly 25,000 JLR employees have completed sustainability training, with over 500 participating in specialized manufacturing immersion sessions.
An advanced training program centered on circularity will soon launch to further integrate sustainability into the company’s culture.
A holistic approach to emissions reduction
JLR's extensive energy optimisation projects have achieved a 24.1% reduction in operational emissions over the last four years. B
y adopting renewable energy, upgrading equipment, and implementing innovative fuel-switching strategies, JLR aims to reduce emissions by 46% across its operations by 2030.
With these transformative changes, the Halewood facility is poised to become a cornerstone of JLR's electrification and sustainability strategy, establishing it as a leader in the green automotive revolution.
As JLR continues to innovate in sustainable manufacturing, Halewood will be pivotal in advancing the company's vision for a greener, more sustainable future.
Make sure you check out the latest edition of Manufacturing Digital and also sign up to our global conference series - Manufacturing & Mobility LIVE
Manufacturing Digital is a BizClik brand
- Tata & JLR: Supercharging Next Gen Automotive ConnectivityTechnology
- Manufacturing & Mobility LIVE: The Future of EVs & MobilitySustainability & ESG
- Saab: Automotive Repurposing for Sustainable SuccessSustainability & ESG
- Stellantis & CATL Boost EV Manufacturing CapacitySustainability & ESG