Sandvik Celebrates 50 Years of Manufacturing Osprey Products
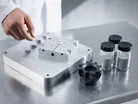
Sandvik is proudly marking 50 years of manufacturing excellence at its Neath production site in the UK.
Over the decades this facility has earned a global reputation for producing the market's most expansive range of gas-atomised metal powders and most unique selection of Controlled Expansion (CE) alloys.
Evolving into a cornerstone of Sandvik’s metal powder manufacturing capabilities, the site showcases immense innovation, precision, and commitment to quality.
"This milestone is a testament to the dedication, hard work, and innovation of all employees, partners, and customers who have been part of the journey," says Andrew Coleman, VP Head of Additive Manufacturing Unit at Sandvik Osprey.
"It demonstrates Sandvik’s long-term experience that makes us a trusted partner for customers in areas such as Additive Manufacturing (AM) and Metal Injection Moulding (MIM), and across a range of demanding industries."
A leader in metal powder manufacturing
The Neath production site’s journey began with modest aspirations, but the site quickly grew in to an industry leader.
Leveraging proprietary atomising technology, the facility has expanded its capabilities to produce over 2,000 different alloys under the renowned Osprey® brand.
This diverse portfolio specialises in fine and mid-fraction sizes, catering to a wide array of industrial applications.
From aerospace to automotive, the Osprey® range has become synonymous with quality and reliability.
Gas atomisation, a process that ensures the production of high-purity, spherical metal powders, has been central to the site’s success.
This advanced technology enables precise control over particle size distribution and composition, meeting the stringent requirements of industries that demand exceptional material performance.
The facility’s ability to innovate and adapt has solidified its standing as innovator in the field of metal powder manufacturing.
Advancing technology with CE alloys
In addition to its extensive range of metal powders, the Neath site is home to the production of Sandvik’s exclusive CE alloys.
These alloys are produced using Hot Isostatic Pressing (HIP) technology and are engineered for applications requiring exceptional stability in extreme temperature variations.
CE alloys are a vital component in industries such as electronics, aerospace, and precision engineering where thermal management and structural integrity are critical.
Sandvik’s investment in research and development has enabled the Neath site to continually evolve and improve.
Meeting the milestone of 50 years underscores the facility’s enduring commitment to manufacturing cutting-edge materials for some of the world’s most demanding industries.
By continuously refining its processes and expanding its product offerings, Sandvik continues to advance manufacturing in these respective industries.
Setting new industry benchmarks
As Sandvik celebrates this milestone for the Neath facility, it also reiterates its commitment to driving innovation and improvement in the metal powder industry.
The Neath facility’s proven heritage and capacity to deliver high-quality materials ensure it will continue to play a vital role in supporting this.
With a steadfast focus on excellence and sustainability, Sandvik is poised to shape the future of metal powder manufacturing for decades to come.
Explore the latest edition of Manufacturing Digital and be part of the conversation at our global conference series, Manufacturing LIVE.
Discover all our upcoming events and secure your tickets today.