BEAMIT: Additive Manufacturing for More Resilient Alloys
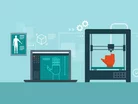
Outperforming components made with traditional processes, additive manufacturing promises to play a major role in manufacturing digitalisation and disruption. In the ‘HP AM Trends in EMEA’ report, 96% of companies agreed that additive processes sped up their time-to-market. Moreover, 50% of British manufacturers intend to spend over €1mn on it over the next five years. In this respect, the BEAMIT Group will lead the market: as of right now, the company has created an ultralight aluminum alloy—the 2024-RAM2C—that could upend the aerospace and motorsport industries.
Why BEAMIT?
Based in Fornovo di Taro, Italy, the BEAMIT Group is one of the most advanced additive manufacturers in the world. It holds the top quality certifications, including IATF Automotive, NADCAP heat treatment and welding, and AS/EN 9100:2018 aerospace accreditations. The group has also recently added new capabilities to its repertoire. In 2019, the Sandvik Group—a leader in hi-tech engineering and AM printing—took a major stake in the company; in 2020, BEAMIT invested in PRES-X, a specialised 3D post-production firm; and in 2021, it acquired 3T Additive Manufacturing. With this expertise, the Group developed a new, stronger, more impressive alloy.
How Was The Alloy Developed?
Up to now, 2000 series aluminium alloys couldn’t be made with additive manufacturing. Each metal that went into the alloy solidified at different temperatures, which made it almost impossible for manufacturers to melt and form parts. Consequently, BEAMIT collaborated with Elementum 3D to add 2% of a ceramic phase into the initial alloy material, modifying it for better additive manufacturing results. ‘It’s very difficult to process 2000 series aluminum alloys via L-PBF (Laser Powder Bed Fusion), so developing this material really motivated us’, said BEAMIT Group Material and Special Processes Manager Alessandro Rizzi.
Next came the task of optimising the heat process. With BEAMIT’s fully integrated value chain—essentially, oversight of all parts of their manufacturing process—the Group put together a multidisciplinary research group. By studying and applying what they learned, its team members found the optimised window for the 2024-RAM2C’s heat treatment, thus improving its durability. As Group General Manager Andrea Scanavini explained: ‘We can safely say [this alloy] is decidedly extraordinary’.
Finally, PRES-X—BEAMIT’s innovative startup subsidiary—developed a process named HIP Quench, a post-production process that helped eliminate moulding flaws. It cooled materials at over 3,000°C/min, helping maintain the alloy’s geometric properties even as it was formed into customised parts and pieces.
What Makes It Better?
For motorsport, automotive, and aeronautical industries, stronger is superior. Critical parts must hold up to high temperatures, weather corrosion, and unexpected damage, all while remaining lightweight. As a 2000 series alloy composed of aluminum, copper, magnesium, and that small bit of ceramic phase, the 2024-RAM2C meets all these specifications. In motorsport, it will likely be used for suspension, chassis parts, and the structural components of the powertrain, all of which sit in close proximity to a white-hot engine. Structural integrity, in this case, is a coup de grâce.
And as British and foreign companies continue to invest in additive manufacturing, BEAMIT projects a bright future. The Group will keep expanding and developing its alloys for aeroplanes and automotives, drawing on its ties to its expert 3D partners. ‘The 2024 alloy perfectly embodies what we mean when we talk about the integrated development of the additive process’, said Scanavini. Added Group President Mauro Antolotti: ‘This continually evolving advancement is an integral part of the Group’s long-term strategy’.
- Sandvik Celebrates 50 Years of Manufacturing Osprey ProductsProduction & Operations
- Angela Grigonis Regan: Creating Manufacturing’s 3D FutureSmart Manufacturing
- Stratasys’ 3D printing journey & the impact on healthcareTechnology
- Top 10 3D printing manufacturing companiesLean Manufacturing