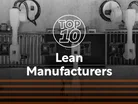
As technology advancements and consumer demands develop almost every day, lean manufacturing is essential to adopt to increase the efficiency and productivity of the global industry.
Not only does lean manufacturing catalyse greater product quality and higher customer satisfaction, but the adaptability of lean practices means companies can meet changing market demands effectively and innovate alongside them.
With consumer demands changing to include greater sustainability efforts, lean manufacturing allows sustainability efforts to be enhanced by reducing environmental impact and waste.
Here, Manufacturing Digital takes a look at the top 10 lean manufacturers that are enhancing efficiency and sustainability throughout the global industry.
10. Caterpillar
Founded: 1925
Employees: 113,200
CEO: Jim Umpleby
Revenue: US$67.1bn
Caterpillar, a global construction and mining equipment manufacturer, leverages lean manufacturing principles to minimise waste and improve efficiency.
The company utilises lean tools, such as value stream mapping, through its Caterpillar Production System (CPS). The system aims to enhance efficiency, quality and safety through minimising waste and process transformation.
Caterpillar also displays its exceptional dedication to remanufacturing through its system, Cat Reman. By doing this, the company can return used components to customers, after restoring its condition, at a reduced cost. Caterpillar applies lean principles like total productive maintenance to highlight its commitment to a sustainable future.
9. Honda
Founded: 1948
Employees: 194,993
CEO: Toshihiro Mibe
Revenue: US$141bn
Honda relies on lean production at its Yorii factory in Japan to create the hybrid Fit. The company reduces its production cost and energy consumption by improving the speed of stamping, using fewer robots and minimising paint coats.
Honda continues to reduce its waste by implementing a just-in-time (JIT) inventory system to its supply chain. By doing this, the company ensures that components and parts are only ordered when it is necessary.
8. John Deere
Founded: 1837
Employees: 82,200
CEO: John May
Revenue: US$52.58bn
John Deere has implemented lean manufacturing processes to adapt to the ever changing nature of the heavy equipment industry.
John Deere has formed ‘Scrum teams’, cross-functional, small teams that drive rapid development and feedback by working in short cycles.
In addition to this, the company began to develop a mindset of openness, continuous learning and collaboration to implement lean manufacturing effectively.
By adopting these methods, John Deere was able to enhance its collaboration with teams, reduce the time to market and increase employee satisfaction.
7. Boeing
Founded: 1916
Employees: 170,000
CEO: Kelly Ortberg
Revenue: US$73.15bn
Boeing implements lean manufacturing processes to enhance productivity and enhance its safety and on-time commitments.
For the CST-100 Starliner crew seats, technicians use templates to measure and trim the fabric. By ensuring this accuracy, Boeing can save time and improve experience for consumers by improving the quality of seats for astronauts on the Starliner.
Boeing also strives to improve its efficiency by reducing the time it takes to complete certain tasks. For example, the task of installing sidewall pockets on the 737 MAX was standardised by the 737 team in Washington. By doing this, the installers can now make holes in the sidewall and put in place a pocket in less than ten minutes by using a safer, cleaner and faster drill.
6. Intel
Founded: 1968
Employees: 124,800
CEO: Pat Gelsinger
Revenue: $54.23bn
Intel focuses its lean manufacturing efforts on semiconductor fabrication.
To enhance productivity within the organisation, Intel adopts a culture of ‘Kaizen’. By doing so, employees are committed to continuous improvement in its workforce and drive processes and innovation.
Intel has also enhanced its production efficiency by reducing the time it takes to create a semiconductor chip. Because of this, the company has been able to manage changing customer demands with ease.
The company continues to eliminate any defects in its manufacturing process to ensure it can maintain its competitive advantage in technological advancements.
5. General Electric
Founded: 1892
Employees: 125,000
CEO: H. Lawrence Culp Jr.
Revenue: US$67.95bn
General Electric has enhanced lean manufacturing solutions across manufacturing, services, office operations and inventory management to reduce its costs and enhance its efficiency.
A group of engineers from GE Aviation and GE Additive have applied lean manufacturing to reduce the cost of four parts to transform a power plant by up to 35% in 10 months.
FieldCore, GE's service subsidiary, has also cut the time to replace a critical turbine component from 25 to 13 hours through lean practices.
By applying these principles, the company has enhanced its productivity and minimised unnecessary expenditure.
4. Danaher Corporation
Founded: 1984
Employees: 63,000
CEO: Rainer M. Blair
Revenue: US$24bn
Danaher Corporation leverages lean manufacturing through its Danaher Business System (DBS).
The system promotes continuous improvement and sustainable processes in the workplace.
Leica Biosystems, one of Danaher Corporation’s businesses, have utilised DBS for its Aperio GT450 product and have experienced significant benefits, including a 1.5x growth in revenue and 33 patents generated.
DBS allows the organisation to adapt to the evolving business environment. By applying this method, Danaher Corporation can minimise time to market, reduce lead times and produce innovative solutions and products.
3. Nike
Founded: 1964
Employees: 83,700
CEO: Elliott Hill
Revenue: US$51.4bn
American athletic footwear and apparel corporation, Nike, has implemented lean manufacturing principles in its work to enhance the sustainability and efficiency of its production methods.
The organisation’s ‘Move to Zero’ campaign ensures that its global operations achieve zero waste and zero carbon. In addition to this, Nike applies this effort to its supply chain to improve the efficiency of distribution and production processes.
Nike utilises its Sourcing & Manufacturing Sustainability Index (SMSI) to ensure sustainability lies at the forefront of its work.
The index rates each carrier the company uses on carrier on environment, human resources, safety and community standards. By adopting this holistic approach to sustainability, Nike can enhance its efficiency and track compliancy across the organisation.
2. Ford
Founded: 1903
Employees: 177,000
CEO: Jim Farley
Revenue: US$176.2bn
Henry Ford is often considered the ‘father of lean manufacturing’ due to his work of integrating lean into a manufacturing system.
To enhance customer value and improve efficiency, Ford has implemented several lean manufacturing techniques.
The organisation leverages a just-in-time (JIT) inventory system to reduce excess inventory and waste by making sure the correct materials are to hand when needed.
In addition to this, Ford invests significantly in robotics and automation to enhance its manufacturing processes, such as utilising cameras and smart sensors for quality control and using robots to enhance speed and accuracy.
Ford also ensures its value chain is consistently analysed to identify any weaknesses. By doing so the organisation can dissect every step of the process to discover areas that can be fixed to improve efficiency and reduce costs, whilst also applying lean principles to distribution and supplier networks.
1. Toyota
Founded: 1937
Employees: 370,000
CEO: Koji Sato
Revenue: US$298bn
Toyota implements lean manufacturing initiatives through its Toyota Production System (TPS).
The system, which strives to reduce waste and enhance efficiency, operates through two principles - Jidoka and ‘Just-In-Time’.
The company detects and solves issues that could reduce the quality of its products through Jidoka (a Japanese word that means ‘intelligent automation’).
When an issue is identified in the manufacturing process, the production line is immediately stopped. By doing this, the company can avoid creating products that malfunction.
To enhance efficiency further, every member of the team on the production line will stop their current work to fix the issue that was identified to ensure normal work can resume along the assembly line.
Just-In-Time coordinates and refines all of the production processes. By doing so, Toyota minimises waste and only creates what is necessary in the next stage of production.
Make sure you check out the latest edition of Manufacturing Digital and also sign up to our global conference series - Manufacturing & Mobility LIVE
Manufacturing Digital is a BizClik brand.