Q&A: Data Management in Manufacturing with Informatica
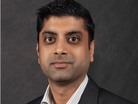
Siddharth Rajagopal is the Chief Architect for EMEA-LATAM at Informatica, boasting more than 17 years of expertise in data management.
He has partnered with industry giants such as Unilever, Subaru, Rolls Royce and GSK, revolutionising their data strategies.
As a seasoned Solution Architect, Siddharth is certified in AWS Solution Architecture, TOGAF® Foundation, Informatica, Teradata, Tableau and holds SAFe Agilist and Scrum Master credentials.
His proficiency spans cloud modernisation and metadata-driven data architecture. Adept at engaging varied audiences, Siddharth excels in delivering both strategic business insights and in-depth technical solutions to meet complex challenges effectively.
Here, he speaks to Manufacturing Digital about the role data plays in the future of manufacturing.
What role does data management have to play in the future of manufacturing? Why should companies make the transition?
In essence, the better your data management, the more accurate your data-driven insights will be – and the more competitive advantages you get.
The true value of data management emerges when insights derived from well-managed master data are actively used in frontline business, such as within a manufacturer's supply chain.
Master data focuses on the critical data and business processes, whilst metadata provides a wide view of the business and how applications in manufacturing can be connected to the critical business initiatives of the enterprise.
Together, this combination can power AI and automation needs, for example, creating a Digital Twin for smart manufacturing. By effectively managing material master data, manufacturers can optimise inventory levels, enhance production scheduling and reduce material costs.
Likewise, analysing supplier data enables better supplier selection, more favourable negotiations and improved supplier performance management. And a well-managed compliance data store enables companies to adhere to industry standards and regulations, mitigating risks and preventing costly
disruptions.
Integrating these types of data into supply chain operations drives strategic decision-making, boosts efficiency and fosters a more resilient and responsive supply chain, ultimately contributing to the manufacturer’s competitive edge and growth. But none of this is possible without good data management.
If you can’t trust the quality of your data, you can’t trust the insights it provides.
Are there any examples that stand out to you when you worked with a client to make the transition to data-driven manufacturing?
A recent example is our work with Subaru, a leading global car manufacturer.
Subaru faced challenges with siloed data across various departments, which hindered their ability to integrate critical information throughout the vehicle lifecycle.
To address this, the company implemented Informatica's AI-powered Intelligent Data Management Cloud (IDMC) platform to drive a global-scale data integration project. This allowed Subaru to consolidate data from vehicle development, production and after-sales maintenance, creating a company-wide data integration platform.
As a result, Subaru can now seamlessly link lifetime data such as vehicle development, manufacturing, sales, maintenance and customer information, enhancing both employee productivity and customer experience.
Another example that stands out is KLA – a Fortune 500 company that produces process control and yield management systems used by manufacturers like Intel and Samsung.
It wanted to better serve its expanding customer base, as well as satisfying internal demand for more powerful analytics.
So, along with Snowflake, we worked with them to deliver a cloud-first data strategy that would speed up critical reports and so enable better informed decision-making across their core business teams.
KLA’s business was growing quickly and its expert physicists, engineers, data scientists and business executives depended on real-time insights to predict and meet demand. While their existing on-premises data warehouse performed well most of the time, it had difficulty during critical periods of peak demand, particularly the end of each month or quarter.
Plus, not all its major business units were using the data warehouse, turning to their own systems instead. With all that in mind, KLA wanted to make their data consistently available for reporting and analytics.
It settled on Informatica Cloud Data Ingestion and Replication, a cloud platform that can scale on demand and connect to any on-premises or cloud data source and allows for continuous replication to the cloud data lake.
Over a single weekend, a database administrator and data architect moved approximately 1,000 Oracle database tables (representing 12 years of historical ERP data) to the cloud, where they’re now available for analysis. Incremental changes in Oracle data are automatically captured and integrated directly in the system.
Multiple further data sources were combined in the cloud for analysis, including ERP and CRM, among other sales and manufacturing systems.
As a result, KLA can now execute more detailed and user-friendly reporting, so that teams can predict demand across complex and often customised product groups.
Convenient dashboards built with Microsoft Power BI pull data from the cloud and shed light on sales performance, as well as service contracts and overall customer satisfaction. Previously, these reports took teams of five up to two weeks to pull data from the CRM.
Now, it produces the reports weekly, meeting demand for analytics even at month-end and quarter-end — a feat that was unattainable without a scalable cloud platform
What is a 'golden record' and how can manufacturers achieve this? Can streamlining this improve product standards?
A ‘golden record’ is a master record that includes all location, supplier, factory, customer and product master data from all sources.
This kind of consolidated overview provides easy access to product master data, product structure data, versions and metadata, logistics information, governance and quality management information, such as certificates and regulatory requirements.
By consolidating all this data into a single view, organisations can streamline operations, enhance data quality and improve decision-making processes. This can have obvious positive effects on the end product – but it doesn’t end there.
Things really get interesting when you combine the golden record with large language models (LLMs) – AI language processors like ChatGPT.
Using your golden record as the knowledge base for an LLM means a single text field is enough for extensive research across all sources.
Staff can ask questions like, ‘Which products do we buy from supplier X and where are all the parts installed?’ and get answers quickly and easily.
Rather than having to conduct lengthy and difficult data searches, every employee can use AI to determine the complete company-wide relationship network of products, semi-finished, finished and supplier parts.
What are the biggest challenges involved in going from a more analogue system to data-driven Industry 4.0?
One major challenge of transitioning to a data-driven approach is that data is anything but static: it’s constantly changing.
The total amount of data in companies can change by up to 27% over the course of a year one .
That means providing accurate information on location, supplier, factory information, customer aspects and product features can be an enormously time-consuming process requiring the involvement of many experts.
It’s not easy to identify the data in different sources and create a coherent picture from all the collected data points.
The difficulty of effectively gathering and updating all that data can become a business risk during crucial moments involving things like product recalls, supply chain disruptions or quality issues.
Even developing sustainability strategies or production planning can be very time-consuming and labour-intensive processes without good data management.
Make sure you check out the latest edition of Manufacturing Digital and also sign up to our global conference series - Manufacturing & Mobility LIVE
Manufacturing Digital is a BizClik brand.