Alchemie Technology on sustainable textile manufacturing
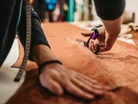
The fashion and textile industries are some of the biggest polluters on the planet, creating 3% of global CO2 emissions and being the second largest cause of water pollution worldwide.
Disruptive technology leader Alchemie Technology is ready to change the industry, by reducing wastewater, energy and carbon emissions during the dyeing and finishing processes, as well as lowering operating costs across the supply chain. The company recently joined the D(R)YE Factory of the Future Project, launched by Fashion For Good to accelerate the shift from wet to dry processing in the textile supply chain. The project has brought together several innovations in textile pre-treatment and colouration with the aim of reducing emissions and cutting water consumption.
Here, Dr Alan Hudd, founder of Alchemie Technology, explains why it is critically important to lower emissions from the fashion and textile supply chain.
10% of global CO2 emissions are caused by the fashion industry
When people think about sustainability and corporate responsibility in the fashion world, their immediate thought is probably sweatshops. The collapse of the Rana Plaza factory in Bangladesh in 2013 still looms in all our minds. The other issue we hear a lot about is recycling and the efforts brands are making to counter increasing global production and consumption of clothes.
What we don’t talk about enough is the environmental impact of the traditional dyeing processes which colour all our clothes, including the ones you are probably wearing right now. The fashion industry as a whole uses huge amounts of energy and water (an estimated 93bn cubic metres a year) and generates up to 10% of global CO2 emissions.
Within the fashion and textile sector, the single worst contributor to climate change is dyeing and finishing – the processes by which colour and other chemicals are applied to fabrics, using chemical baths. These are some of the most polluting industrial processes in the world.
Textile dyeing and finishing is responsible for 3% of global CO2 emissions (predicted to increase to more than 10% by 2050). That is more than the CO2 produced by shipping and aviation combined. It also causes over 20% of global water pollution.
The wastewater makes its way into rivers and into the sea, particularly in those countries which still dominate dyeing like China, Bangladesh, Thailand and Indonesia. It can also be a dangerous industry to work in. In early January, six workers at a dyeing plant in India were killed after inhaling toxic gas caused by an illegal dump of waste chemicals.
At the same time our global passion for fashion and clothes only continues to grow. Apparel consumption is set to rise by 63% to 102mn tonnes a year in 2030, according to a 2017 Pulse of the Fashion report. If we are to honour the recent COP 26 pledges, to reach net zero targets by 2050 and keep 1.5 degrees within reach, the textile industry needs to dramatically reduce energy and water consumption.
The good news is that the textile and fashion industry is one which can reduce its CO2 emissions at the greatest speed and make a huge contribution to the fight against climate change.
Creating sustainable solutions in textile manufacturing
In 2014 I made my own pledge - to apply my experience in industrial inkjet printing to textiles and come up with sustainable dyeing solutions that would transform an industry to reduce its climate impact; Alchemie Technology was founded in Cambridge with that one big idea.
A few years later our digital dyeing Endeavour machine, which produces no wastewater and reduces energy consumption by 85% compared to traditional dyeing, is now in production.
This month we are shipping a machine to Taiwan, where it will form the centre piece of a new Alchemie demo hub and showroom in Asia so textile producers from around the region can see the technology in action. We’re hoping it will kickstart a sustainable dyeing revolution – and will encourage more brands and manufacturers to come on board.
Those countries which are centres of traditional dyeing are also beginning to take environmental issues seriously. In Bangladesh the government is bringing in legislation requiring factories to install water treatment plants. China too has been coming down hard on polluting textile factories.
However, no single country or company can drive change alone. Everyone across the textile supply chain, including brands and manufacturers, needs to work together to move away from wet to dry dyeing.
Real change will be driven by consumers and brands demanding that clothes are produced in less harmful ways. It also requires the support of governments through investment, grants and legislation to complete the change towards sustainable dyeing.
Only this way can we change the colour of our clothes to green, to the benefit of the planet and for future generations.
- Heineken & ENGIE: Brewing a Net Zero FutureSustainability & ESG
- JCB's Texas triumph with new site in manufacturing hubTechnology
- Siemens & BayWa offset manufacturing supply chain emissionsProcurement & Supply Chain
- Sustainability in paper & forest product manufacturingProcurement & Supply Chain