Balancing Technology & Employee Engagement in Manufacturing
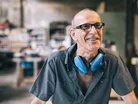
In fast-paced industries like manufacturing, leaders may feel the pressure to innovate and roll out the latest technology update as soon as it’s available. But when it comes to technology investments and implementations, it’s important for manufacturers to take a crawl-walk-run approach.
“New technology is coming out at an accelerated pace and many times the tech is oversold or pushed out before it’s fully ready,” says Bill Remy, CEO of TBM Consulting Group. “With a crawl-walk-run approach that’s methodical, companies can make sure the technologies they’re investing in are a true value add.”
Investing in people is the key to successful technology adoption in manufacturing
TBM Consulting Group is a team of lean manufacturing operations and supply chain consultants, which helps clients enable technologies and lean process rigour to enhance operational speed. The company is dedicated to building flexible companies which can solve problems and respond to opportunities faster than their peers.
After joining Vanguard Software Corporation’s growing network of channel partners, the company explored the merits of lean manufacturing with Manufacturing Digital.
While Remy absolutely acknowledges that technology adoption is essential for sustainable growth, it is even more important to remember that technology investments are not mutually exclusive to investments in people.
“Technology only works when the people are there to implement it, so leaders must continuously invest in their people – the investment in people is also the investment in tech.”
When manufacturers implement new technology and automate tasks, they are automatically going to need less people, so Remy recommends a ‘no layoff policy’, when new tech changes are on the horizon.
“With a no layoff policy, employees have the assurance that regardless of whether their tasks are offloaded, they won’t be let go,” he explains. “Instead of laying off these employees, come up with a roadmap for them.”
This can look like reducing overtime, slowing down hiring and reskilling or cross training employees to work in areas that drive top line growth and increase customer intimacy, something technology cannot achieve.
Balancing tech investment and employee engagement
With investments in tech, communication is also essential. Remy advises that a strong message to employees which lets them know that investments into automation will not result in layoffs is imperative.
“Otherwise, you’ll end up with unhappy employees who fear for job loss and passively resist the tech advancements,” he explains. “Manufacturers' communication should include why the change is being implemented, the call to action and the impact of the new technology.”
There have been many headlines over the past few months around cutting costs through layoffs or closures, citing over-investing in technology. According to Remy, it’s time to take a step back and re-evaluate how investing in technology and not employees will hurt manufacturers in the long run.
In this exclusive byline, André Smaal, TBM Vice President for Europe, discusses how Precision of Execution enables organisations to drive sustainable change and breakthrough performance.
“However urgent the case for change may be, companies still need a dedicated team of top management, including the COO and other high-level operations leaders, to fully commit to the concepts of operational excellence and lean manufacturing,” he said.
Read it here.
******
Make sure you check out the latest edition of Manufacturing Digital and also sign up to our global conference series - Procurement & Supply Chain 2024 & Sustainability LIVE 2024
******
Manufacturing Digital is a BizClik brand.
- Manufacturing Unwrapped: Manufacturing Leader Jeff WinterDigital Factory
- Manufacturing Unwrapped: Inside IKEA, The Wonderful EverydayProduction & Operations
- Manufacturing & Mobility LIVE: Neby Ejigu, FINN PartnersTechnology
- Manufacturing & Mobility LIVE: Beatriz Gutierrez KeynoteSmart Manufacturing