Digitalisation in manufacturing & the link to sustainability
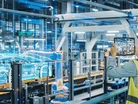
Benoit Wambergue is the VP of cloud products strategy at Forterro, a company which delivers software and services to nearly 10,000 small and midsized manufacturing companies around the world.
Forterro was founded in 2012 with the acquisition of Jeeves Information Systems AB, and has grown to become one of the leading software providers in Europe and the home for specialised ERP companies serving industrial SMEs. While customers interact with a diverse range of solutions tailored to their requirements, the Forterro group provides the know-how, infrastructure and capital to invest and optimise these solutions.
Here, Wambergue tells us more.
Tell us about the evolution of Net Zero.
“Simply put, Net Zero means the same amount of greenhouse gases being emitted into the atmosphere are also being removed. When the UK government committed to achieving Net Zero by 2050 it was a legal commitment for the state, industry and consumers alike to decarbonise.
“Discussions around Net Zero have been around for more than a decade, and pledges now cover more than 90% of the global economy, but as 2050 moves ever closer, the need to turn pledges into action is increasing.
“The manufacturing sector is currently responsible for carbon emissions totalling 81 megatons a year.The future of Net Zero, whilst the government's responsibility, depends on local authorities, companies, investors and the third sector working together to achieve Net Zero targets by 2050.Over recent years, manufacturers of all sizes, their customers, and end-consumers, are increasingly demanding sustainable practices across the supply chain. As regulation and consumer demands for action towards Net Zero increases, sustainable practices have gone from a ‘nice to have’ to being non-negotiable.”
What has been Net Zero's impact on the supply chain?
“As well as the obvious benefits to the planet, and commercial benefits of aligning with customer expectations, Net Zero is also an opportunity to increase efficiency by rethinking and reworking supply chains. This will help ensure firms get the maximum value from energy, materials and components – all of which have seen price fluctuations in recent years due to the ongoing supply chain disruption.
“With the UK and much of Europe on the brink of recession. economic growth has been pushed to the top of the agenda. For smaller manufacturers facing major obstacles around supply chain disruption, material shortages and labour availability, planning for growth while overcoming these challenges may seem like a daunting task.
“Every part of the supply chain is now under scrutiny, from materials to energy consumption, production processes and transport. Logistics and supply chains are a large source of both emissions and operating costs for businesses. While smaller suppliers might be out of the public gaze, their bigger customers are under scrutiny, and their expectations filter down the chain.”
How are logistics companies bridging the gap between intention and reality when it comes to Net Zero?
“Starting the journey towards sustainable manufacturing can seem like an impossible task, especially for SMEs with limited resources and without expert knowledge. But consider the challenge against other big industry changes — such as the Fourth Industrial Revolution — and it’s easy to see the approach that every business should take, regardless of their size.
“It sounds daunting, but the good news is, logistics companies may already be making strides even without realising. Digitalisation in manufacturing, which ramped up during the pandemic, is inextricably linked to sustainability. Effective planning and data usage tell us that what’s good for business and the planet doesn’t have to conflict.
“Insight is key. With accurate data, it’s possible to make small, manageable changes that can soon add up to create a big impact. A lack of insight into the function of your factory will make it difficult to identify where efficiencies could be made.
“A good ERP is central to this, giving you the information you need to make better decisions. Lean manufacturing through an ERP system eliminates waste and increases profits whilst passing on benefits to customers. Waste can be as a result of uninspired workers, poor processes or unused materials.
“The four key benefits to learn are quite simple in theory; Waste is eliminated, costs are reduced, quality is improved, and efficiency is increased. And therefore, manufacturing moves one step closer to Net Zero.
“For any business to truly reduce its emissions, the full supply chain also has to be on board. And as more businesses embrace an Industry 4.0 mindset which favours interconnectivity and automation, this optimistic outlook could soon be a reality for everyone in the industry.”
Tell us about digitalisation in manufacturing and its link to sustainability.
“Adoption of digital technologies can help reduce costs and improve the sustainability and flexibility of manufacturing industries.
“Data-driven analytics can be extremely powerful in solving previously unsolvable problems, and sometimes even unknown ones too, such as hidden congestion, operational stringency, and areas of disproportionate changeability. As companies get better at understanding and utilising their data more quickly and easily, the data flow between processes can also support continuous improvements in quality and production planning.
“By pulling data from internal and external sources, you can not only reveal the cause of issues, but you can begin to identify trends. Forward-thinking companies are also using artificial intelligence (AI) and machine learning (ML) to forecast demand and service quality. Together AI and ML can offer defined planning and preparation for problems, even implementing solutions through automation before something even crops up.
“Companies must take control of their data and processes to make them work seamlessly. By tying together the plethora of processes needed to run a business, you enable the flow of data between them, meaning you gain resilience, real-time agility, growth, and also more sustainable practice.”
What do the next 12 months hold for you?
“Following on from COP26 in 2021, the UK manufacturing sector has been eager to show how seriously it’s taking the transition to a net-zero carbon economy. In addition to cutting greenhouse gas emissions, we’re seeing businesses delivering more innovative products, processes and services.
“Make UK’s research, Decarbonising Manufacturing – Challenges and Opportunities shows that companies are really ramping up their efforts to decarbonise due to rising energy costs and raw materials. Nearly half of manufacturing companies are already implementing their decarbonisation plans, with a quarter looking to start in the next 12 months.
“The UK’s Net Zero commitment and the European Industrial Strategy are recent campaigns, but we’re seeing new targets and guidelines being regularly set out by policy makers. With the increased agility offered by using ERP software, keeping up with the newest sustainability practices, or simply reacting to the changeable business environment, is made more simple.”
- The University Manufacturing Circuit Boards from LeavesSustainability & ESG
- Schneider Electric's Commitment to Sustainable ManufacturingSustainability & ESG
- Lenovo & Saudi Alat Building Green Manufacturing FacilitySustainability & ESG
- Nissan Brings Biodiversity to the Factory through RewildingSustainability & ESG