How are global supply chain issues impacting manufacturing?
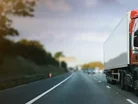
In January 2020, the industry was hit with yet more uncertainty as Wuhan in China went into the first coronavirus lockdown. Other countries soon followed, and by March 2020, the UK was also in a national lockdown. Manufacturers had been trying to prepare for various 'deal' or 'no-deal' outcomes since the 2016 referendum; no one expected this scenario.
The pandemic was the catalyst for the massive shift in the worldwide economy, changing people's spending habits, working patterns and everything in between.
From the restricted transport of goods and services to the semiconductor shortage that has devastated the automotive industry and held up production across many others, COVID-19 exposed the fragility of the current global supply chain structure.
Unfortunately, we are still riding out this wave, but it remains to be seen if global supply chains as we once knew them — which are sensitive to international geopolitics and change — will still be suitable for a post-pandemic, post-Brexit world.
An unprecedented challenge
The past year's events have devastated global supply networks and raised questions about how to make the 'just-in-time' supply model viable for the 'new normal'.
Many manufacturers have long been reliant on low-cost supplies from countries in eastern Europe and Asia. When the worst of the pandemic hit China — which supplies a large percentage of products such as mouldings and PCBs to manufacturers in Europe — the ripples were felt worldwide as the supply of products and materials from this region came to a halt.
A combination of problems related to both COVID and Brexit have instigated this widespread disruption and delays to supply networks. The pandemic has had a knock-on effect on the availability of many essential resources — perhaps most significantly, labour. From the retrieval of raw materials to the shipment of goods, everything from sourcing and productivity to manufacturing and logistics has taken a significant hit.
But COVID is not the only issue here. Brexit's Trade and Cooperation Agreement (TCA) with the EU, which came into effect on 1 January 2021, comes with compliance requirements that are likely to cause further delays at borders, at least temporarily. Plus, Brexit has contributed to the loss of some of the workforce forced to leave the UK. A shortage of lorry drivers combined with a lack of available shipping containers and these new Brexit rules and regulations will further contribute to delayed trade between the UK and the EU — and to supplier lead times, as a result.
At the same time, demand has accelerated, and almost all industries have struggled to keep up. Suppliers of plastic, steel and copper — integral elements of most products used by contractors in many sectors — have stated that lead times for some products are being pushed to eight to 16 weeks. Additionally, many have recorded price hikes from suppliers of up to 40%, with no accurate view of how long these will endure.
So, while we tackle the short-term consequences of the pandemic and Brexit, what can be done in the future to avoid another supply chain breakdown?
Designing a more robust supply network
Although the vaccine roll-out might lead to a kickstart of the UK economy, many manufacturers are still reliant on incoming supply from other countries at different recovery stages. As a result, industries are looking to diversify product sourcing and bring the manufacture of essential products and materials home to bypass reliance on external suppliers.
For example, the Made in Britain organisation aims to support and promote British manufacturing, enabling buyers and consumers at home and abroad to identify British-made products.
However, it will take years to build the infrastructure necessary to support the manufacture of components such as microchips at the level of sophistication and scale required — in short, it would not be a quick-fix solution. It is, therefore, all the more vital that manufacturers assess their supply chains and where their goods originate from so that they can remain transparent and reduce additional costs or complications.
The shortage of materials — especially copper, a material widely used by manufacturers — will also remain a pressing issue for many industries. There has been some investigation into potential alternatives, but ultimately none have provided a viable solution.
In the meantime, manufacturers and suppliers can embrace widespread digitisation, as we see increasing requests for wireless (or 'smart') controls and systems. Ironically, the more web-based and 'connected' the world becomes, the fewer plastics and cabling we will need to connect solutions together