How manufacturers can navigate the supply chain crisis
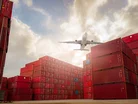
The days of cheap overseas production may be over. Manufacturers are now returning to the US in droves, hoping to reduce their reliance on international suppliers. Most US companies with production operations in China have either moved back to the US or plan to do so in the next three years, according to Kearney's 2021 Reshoring Index.
However, no factory is immune to global supply chain disruptions, making it imperative for manufacturers to be adaptable and agile in responding to raw material variability. Berk Birand, founder and CEO of Fero Labs, says new technologies can help manufacturers to continue to produce items of the same quality, reducing their vulnerability to supply chain disruptions.
Frequent supply chain disruptions and the manufacturing sector
Variability has always been a challenge for factory owners to contend with, as real-life plants rarely measure up to the ideal ones. But with today’s frequent supply chain disruptions, the industry is seeing the pervasive trend of raw materials becoming more scarce. As a consequence, prices are rising at staggering rates.
“Manufacturers are forced to choose between losing out on profits—making them less competitive—or substituting lower-cost alternatives or alternatives from different suppliers, even when they may have different characteristics that affect the ultimate product quality,” says Birand. “Traditional process optimisation techniques, such as Six Sigma, are unable to help manufacturers address these real-time production threats. It takes months to optimise a plant via Six Sigma, as well as significant labor on the part of plant personnel and teams. In order to be best equipped to handle today’s variability in raw materials, manufacturers need some way to monitor product quality in real time and pivot immediately in the face of these continuous disruptions.”
Today, factory optimisation technology is powered by machine learning algorithms that constantly monitor quality across any production process. If there are any unforeseen variability that might affect final quality tests, the technology can detect it and instruct plant engineers and operators on how to adjust manufacturing processes to bring goods back to the “normal” level. As a result, manufacturers are able to maintain the ideal product consistency and quality, even with different ingredients constantly being added.
“There are several different forms that the optimisation process might take, depending on whether a factory employed batch or continuous production methods,” says Birand. “During a steel manufacturing process, for example, alloys are added to recycled steel at a certain stage in order to ensure it meets quality specs. Optimisation technology is able to see what metals are being added and predict the final result, then tell operators exactly how much of the alloys to add, minimising dependence on raw materials. In a continuous production case, the technology might analyse the viscosity of a shampoo and tell operators how many ingredients to add in order to ensure that the final product met quality specs.
“Broadly speaking, the result of all this is to transform the production process, essentially allowing manufacturers to operate successfully in this changing world. Traditionally, ingredients and recipes have been paramount, with factories using a specific amount of certain ingredients to produce a specific item. This made variability a huge threat. However, with technology giving them the ability to adapt to variability, the threat posed by ingredient variance becomes significantly diminished.”
The recent supply chain disruptions have changed the manufacturing sector forever
Birand knows that the ongoing supply chain disruptions have left their mark on the manufacturing industry.
“Agility and adaptability have now become not just buzzwords, but crucial assets for manufacturers hoping to remain competitive in today’s global markets,” he says. “Many are turning to technology to fill in the gaps. In a recent ABB survey, more than 40% of business leaders said that they anticipated using automation and robotics to make their supply chain more resilient.
“With rising energy prices, optimisation has never been more important. Running plants more optimally leads to drastically lower operating costs—crucial for enterprises seeking to stay competitive in today’s environment.
“Given the ongoing variability in the supply chain, manufacturers may fear the worst. However, this is a ripe opportunity for new technology that, when used correctly, can turn uncertainty into your competitive advantage.”
- The University Manufacturing Circuit Boards from LeavesSustainability & ESG
- Schneider Electric's Commitment to Sustainable ManufacturingSustainability & ESG
- Lenovo & Saudi Alat Building Green Manufacturing FacilitySustainability & ESG
- Aggreko: UK Energy Manufacturers must Shore Up Supply ChainSustainability & ESG